Phone: +86-755-2357-1819 Mobile: +86-185-7640-5228 Email: sales@ominipcba.com whatsapp: +8618576405228
Aluminum PCB
Omini is a leading manufacturer specializing in high-quality aluminum PCBs, offering competitive pricing and reliable solutions for various applications. Our aluminum PCB products meet the highest industry standards, ensuring optimal performance and durability.
Layer Count: Available in 1-10 layers to meet the specific requirements of different projects.
Thermal Conductivity: Excellent thermal management with values ranging from 1.0-3.0W/(m⋅K), ensuring heat dissipation for high-power applications.
Stack-up Options: Both normal stack-up and thermoelectric separation designs available for optimal heat management.
Certifications: ISO9001:2015 certified and UL listed for guaranteed quality and safety compliance.
Comprehensive Testing: 100% E-test, AOI testing, and visual inspection to ensure flawless performance and reliability.
IPC Standards: Manufactured according to IPC-A-600 Class 2 and Class 3 standards for enhanced durability and performance in critical applications.
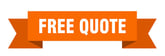
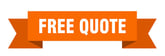
What is Aluminum PCB?
Aluminum PCB is a type of printed circuit board that features a thin layer of material bonded to one or both sides of an aluminum substrate. The materials used in the thin layer are typically heat-conductive and electrically insulating dielectric materials, making them ideal for high-thermal applications. Also known as Metal Core PCBs (MCPCBs), aluminum PCBs offer exceptional thermal conductivity, which is crucial for heat dissipation in various electronic applications.
Due to its superior thermal and electrical properties, Omini offers high-quality aluminum PCB solutions for industries requiring efficient heat management. Common applications include:
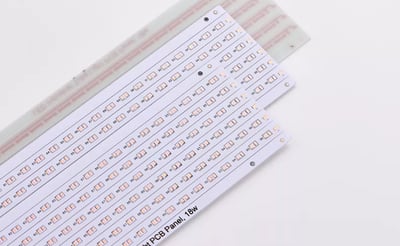
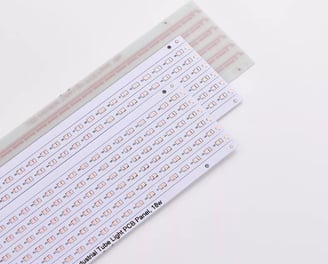
• High-Power LED Lighting: Aluminum PCBs effectively dissipate heat, making them ideal for LED applications.
• Automotive Electronics: Used in automotive circuits where high heat generation is common.
• Consumer Electronics: Devices that require heat dissipation, ensuring reliable performance.
With Omini’s advanced manufacturing capabilities, we deliver aluminum PCBs that meet the stringent requirements of high-performance industries while ensuring competitive pricing and reliable product quality.
Common Types of Aluminum PCB
Aluminum core PCB boards are essential in applications where efficient thermal management is crucial. Based on their intended application, there are three main types of aluminum core PCBs, each offering distinct advantages for specific needs.
1. Single-Layer Aluminum PCB
Single-layer aluminum PCBs consist of one layer of aluminum substrate with a copper conductive layer bonded to one side. These PCBs are simple in design and are primarily used in applications where heat management is critical. Common uses include:
• LED lighting
• Automotive electronics
• Power supplies
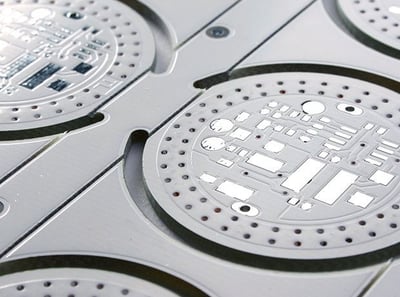
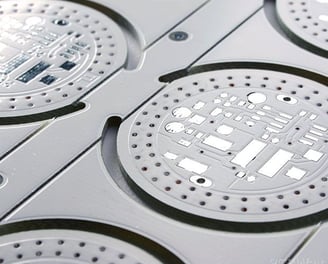
2. Double-Layer Aluminum PCBDouble-layer aluminum PCBs feature two layers of aluminum substrate with copper conductive layers bonded to both sides. This configuration enhances design flexibility and functionality, allowing components to be placed on both sides of the PCB. Benefits of double-layer aluminum PCBs include:
• Higher component density
• Complex circuit designs
• Applications such as power converters and motor drivers, which require improved thermal performance and electrical isolation.
3. Metal-Core Printed Circuit Boards (MCPCBs)
Metal-core PCBs (MCPCBs) are made with a metal core, typically aluminum or copper alloy, sandwiched between dielectric material and copper foil layers. MCPCBs offer superior thermal conductivity and heat dissipation compared to standard FR-4 PCBs. They are ideal for high-power applications and are available in:
• Single-layer
• Double-layer
• Multi-layer configurations
Omini, as a trusted aluminum PCB manufacturer, offers these types of aluminum PCBs to suit various applications, ensuring efficient heat dissipation and reliable performance. Whether you need high-performance LED lighting solutions, automotive electronics, or complex multi-layer designs, Omini provides innovative solutions with competitive pricing and superior manufacturing standards.
Key Factors in Aluminum PCB Manufacturing
For optimized thermal conductivity and better performance, aluminum PCBs undergo several critical manufacturing steps. Omini, with its expertise in PCB production, ensures the highest quality in each phase of the process.
1. Aluminum Material Selection
The first step in aluminum PCB manufacturing is the selection of the substrate. Omini uses high-quality aluminum alloys such as 6061 and 5052, known for their excellent thermal conductivity. These materials ensure that the PCB performs efficiently in heat dissipation applications.
2. Dielectric Bonding
After selecting the aluminum substrate, Omini bonds a dielectric material, such as polyimide or epoxy resin, to the aluminum layer. These materials are thermally conductive and electrically insulating, ensuring effective heat management. The bonding process is carefully controlled to guarantee the strong adhesion between the aluminum core and the dielectric layer, contributing to the overall reliability of the PCB.
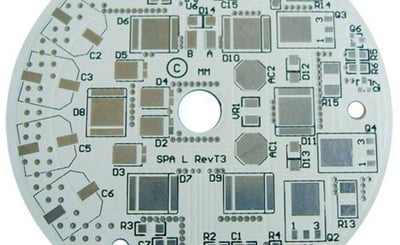
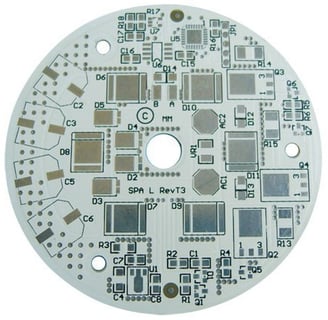
3. Maintaining Suitable Copper Thickness
To ensure efficient heat dissipation and optimal electrical performance, Omini pays close attention to the thickness of the copper layer. The right copper thickness is essential for both thermal management and the reliable operation of the aluminum PCB.
4. Conductive Traces Etching
The final step involves etching the conductive traces onto the aluminum PCB. This process is similar to traditional PCB manufacturing but requires precision to ensure the highest quality and performance. Omini employs state-of-the-art etching techniques to create precise traces, ensuring the board’s functionality and reliability.
Advantages of Aluminum PCB
Omini offers a wide range of advantages when it comes to aluminum circuit boards, including:
1. Improved Heat Dissipation
Aluminum is an excellent conductor of heat, which enables effective heat dissipation from heat-generating components. This reduces the risk of overheating and enhances the lifespan of devices in which aluminum PCBs are implemented. Omini’s aluminum PCBs are designed to optimize heat transfer, making them ideal for applications requiring efficient thermal management.
2. Enhanced Electrical Performance
By combining an aluminum substrate with copper traces, Omini’s aluminum PCBs achieve low thermal resistance and superior thermal conductivity. This results in excellent electrical performance and reliability, particularly in high-power applications. The combination of materials ensures that Omini’s aluminum PCBs consistently meet high standards for electrical reliability.
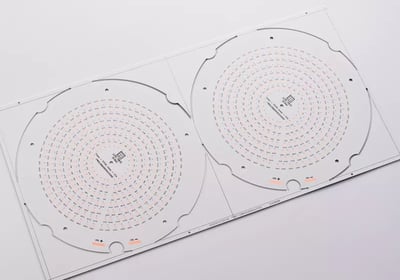
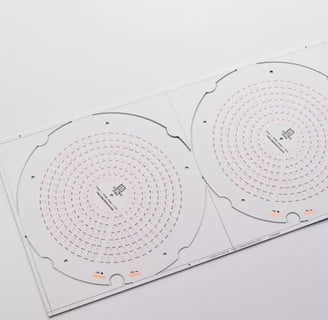
3. Compact and Lightweight
When space and weight are critical considerations, Omini’s aluminum PCBs provide a compact and lightweight solution. The lightweight nature of aluminum allows it to fit into small, confined spaces without sacrificing performance. This feature makes Omini’s aluminum PCBs ideal for applications where size and weight are key factors, such as in automotive or portable electronic devices.
4. Good Mechanical Strength
Aluminum substrate PCBs from Omini are known for their excellent mechanical strength and durability. This makes them suitable for use in harsh environments and challenging weather conditions. The robustness of Omini’s aluminum PCBs ensures long-term performance and reliability even in demanding applications.
5. Cost-effective Solution
Compared to more complex solutions like liquid cooling or heat sinks, Omini’s aluminum PCBs provide a highly cost-effective thermal management solution. Their simple design and ease of manufacturing make them an affordable option, without compromising on performance. This cost-efficiency is particularly beneficial for mass production and high-performance applications.
Disadvantages of Aluminum PCBs
While aluminum PCBs offer numerous advantages, they also come with some limitations and challenges in their overall design and composition.
1. Limited Layer Count
Aluminum PCBs are typically limited to single-layer or double-layer fabrication due to the production process involved. This limitation restricts their application in more complex, multilayer designs. Omini ensures optimal performance within these constraints, but for multilayer requirements, other PCB solutions may be more suitable.
2. Poor Flexibility
Compared to flexible PCBs made from materials like polyimide and polyester, aluminum core PCBs are relatively rigid. This lack of flexibility can be a challenge in applications requiring repeated bending or flexing. Excessive mechanical stress can result in PCB failure. Omini carefully designs its aluminum PCBs to minimize this issue, but flexibility remains a limitation in some applications.
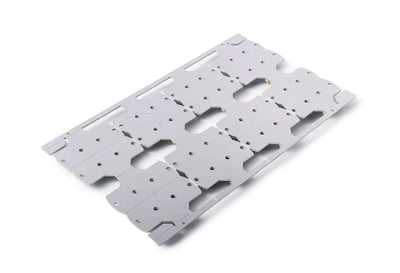
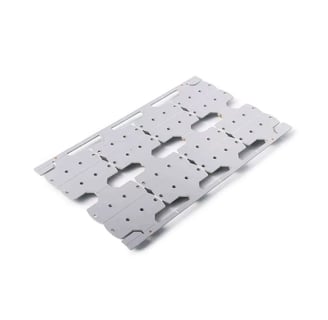
3. Thermal Expansion Mismatch
The coefficient of thermal expansion (CTE) of aluminum is higher than that of many electronic components and solder materials. This mismatch can lead to mechanical stress, solder joint failures, and potential delamination, compromising the overall reliability of the PCB assembly. Omini takes these factors into account during design and manufacturing to mitigate these risks, ensuring the longevity and functionality of its aluminum PCBs.
4. Metallic Substrate Consideration
The metallic nature of aluminum substrates requires special considerations during the manufacturing and assembly process. This can add complexity and increase the cost of production. However, Omini employs state-of-the-art manufacturing techniques to efficiently handle these challenges while keeping production costs competitive.
5. Cost Consideration
While aluminum PCBs are an excellent choice for thermal management, they are generally more expensive than traditional PCB substrates like FR-4. This cost is due to the aluminum substrate material, the specialized fabrication process, and additional surface finish options required for optimal performance. Omini offers aluminum PCBs with competitive pricing, balancing quality and cost for its customers.
Application of Aluminum PCB
Omini provides high-quality aluminum PCBs for a wide range of applications, where efficient thermal management and reliability are crucial. The primary uses of aluminum PCBs include:
1. LED Lighting: LEDs generate significant heat during operation. Omini’s aluminum PCBs are implemented in LED lighting systems to effectively dissipate heat, maintaining optimal performance and extending the lifespan of LED products.
2. Power Supplies: Power supply units, such as switch-mode power supplies (SMPS), require PCBs with excellent heat management capabilities. Omini’s aluminum PCBs help dissipate the heat generated by components like transistors and diodes, ensuring efficient performance.
3. Electronics in Automotive: Aluminum circuit boards are widely used in automotive electronics, including engine control units (ECUs), motor controllers, battery management systems, and LED headlights. Omini offers reliable aluminum PCBs for high-performance automotive applications.
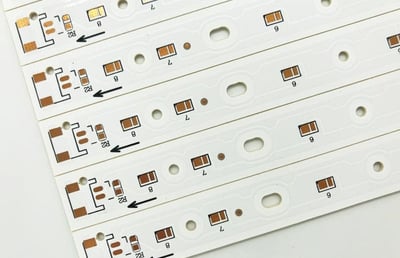
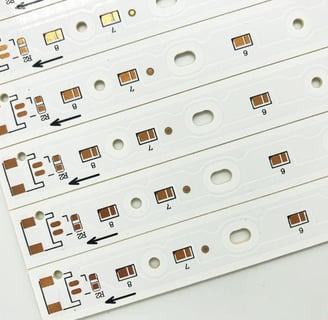
4. Industrial Electronics: Omini’s aluminum PCBs are used in various industrial applications, such as motor controllers, programmable logic controllers (PLCs), automation systems, and power delivery units, ensuring efficient thermal management and durability.
5. Telecommunication Equipment: Aluminum core PCBs are essential in telecommunication equipment, including antennas, routers, and network switches, where thermal performance and reliability are critical. Omini provides high-quality solutions for these applications.
6. Renewable Energy Systems: Omini supplies aluminum PCBs for renewable energy applications, including solar inverters, battery management systems, and wind turbine controllers, ensuring efficient heat dissipation and reliable performance.
7. Consumer Electronics: High-performance consumer electronics, such as audio amplifiers, gaming consoles, and computer graphics cards, benefit from Omini’s aluminum PCBs. These PCBs protect devices from overheating while maintaining excellent performance and reliability.
Future of Aluminium Circuit Boards
The future of Omini’s aluminum circuit boards (Alu PCBs) looks highly promising as the electronic system industry continues to evolve. Ongoing research and development are focused on improving the thermal conductivity of dielectric materials, which will lead to enhanced manufacturing processes for better efficiency and cost-effectiveness. These improvements will drive the application of aluminum PCBs in emerging fields such as:
1. 5G Technology: The demand for faster, more reliable communication networks creates a need for advanced heat dissipation solutions, which aluminum PCBs can effectively provide.
2. Telecommunications: With the growth of telecommunications infrastructure, Omini’s aluminum PCBs will play a critical role in ensuring thermal management in high-performance equipment.
3. Internet of Things (IoT): As IoT devices proliferate, Omini’s innovative aluminum PCBs will support their compact designs while maintaining optimal performance through efficient heat dissipation.
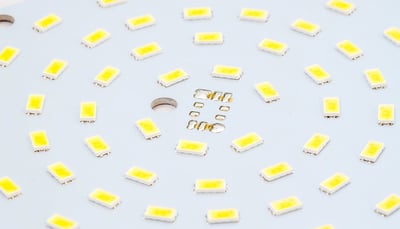
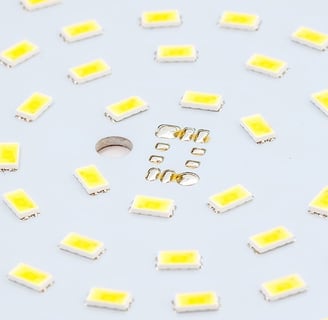
4. Renewable Energy Systems: Aluminum PCBs will continue to be essential in applications like solar inverters and wind turbine controllers, where heat management is crucial for performance and reliability.
Omini is committed to advancing the future of aluminum PCBs, making them a go-to solution for cutting-edge technology in various industries.
Omini: Your Best Choice for Aluminum PCB Supplier in China!
As a leading aluminum PCB manufacturer, Omini has been dedicated to providing high-quality aluminum PCB solutions since 2007. We have consistently delivered products that meet the highest international standards and provide exceptional service to customers worldwide. Here are the reasons why Omini should be your preferred aluminum PCB supplier:
1. Proven Expertise
With over 16 years of experience in the PCB industry, Omini has earned the trust of more than 1,000 customers globally. Our extensive knowledge and commitment to quality make us a reliable partner for your aluminum PCB needs.
2. Competitive Pricing
As a leading aluminum PCB supplier in China, Omini offers competitive pricing that helps you optimize your project budget without compromising on quality. Our cost-effective solutions are designed to meet your specific requirements while maintaining exceptional standards of performance and reliability.
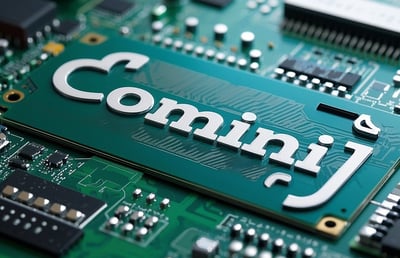
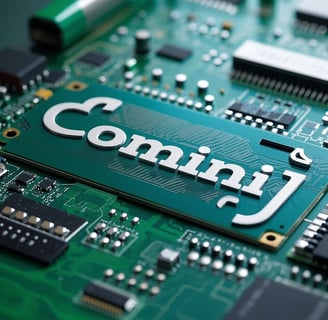
3. Quality Assurance
Omini follows strict quality control measures in every phase of production. We are ISO9001:2015 certified and our aluminum PCBs meet UL and other industry standards. Our commitment to precision ensures that each PCB we manufacture is reliable, durable, and performs at its best in any application.
4. Fast Delivery
At Omini, we prioritize efficiency. Our systematic product flow management ensures that from material procurement to final shipment, every step is streamlined to meet delivery deadlines. With contingency plans in place for any unforeseen circumstances, we guarantee fast and reliable delivery of your aluminum PCB orders.
Contacts
Email: sales@ominipcba.com
Mobile: +86-185-7640-5228
Copyright © 2007-2025. Omini Electronics Limited. All rights reserved.
Head Office: +86-755-2357-1819
Products & Services
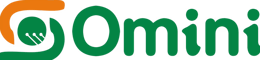
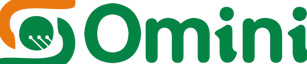
Office Address: No. 605, Tongxin Technology Building, Bao’an Avenue, Bao’an District, Shenzhen, Guangdong, China.
SMT Plant: A Building, Longwangmiao Industrial Park, Baishixia Community, Fuyong Street, Bao'an District, Shenzhen, China.
Omini Electronics Limited is an expert in trusted PCB Fabricaton and PCB Assembly in China since 2007. We have served over 1000 global customers with high-quality, low to medium-volume production. Certified by UL (E532498), ISO9001:2015, and ISO13485:2016, we offer expert electronics manufacturing services, including PCB manufacturing, assembly, and contract manufacturing, ensuring top-tier quality and precision in every project.