Phone: +86-755-2357-1819 Mobile: +86-185-7640-5228 Email: sales@ominipcba.com whatsapp: +8618576405228
Energy Meter PCB
High-quality, reliable Omini energy meter PCBs at competitive prices for precision and performance.
Omini uses premium materials like FR4, High TG FR4, high-speed FR4, PTFE, and polyimide to ensure robust and long-lasting performance.
Advanced manufacturing capabilities include impedance control, peelable mask, carbon ink, and back drilling to meet stringent design requirements.
Omini specializes in blind & buried vias, micro vias, and HDI technology to provide superior electrical connectivity and miniaturization.
Conductive and non-conductive via plugging techniques ensure durability, minimizing signal interference, and improving overall board reliability.
Omini is ISO9001:2015 certified, UL listed, and adheres to IPC-A-600 Class 2 & 3 standards, ensuring high-quality production.
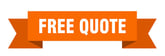
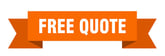
What Is Omini Energy Meter PCB?
If you’re new to energy meter PCBs, it’s time to explore how these crucial components work in energy measurement. An energy meter PCB is a printed circuit board designed to monitor and measure energy consumption in various applications, including residential, industrial, and energy research environments.
Here’s what makes energy meter PCBs essential in energy management:
1. Accurate Energy Measurement: Equipped with advanced sensors, energy meter PCBs monitor critical parameters like voltage and current to provide precise energy usage data.
2. Real-time Monitoring: This data is displayed on a monitor or LCD screen, allowing users to easily track energy consumption in real-time.
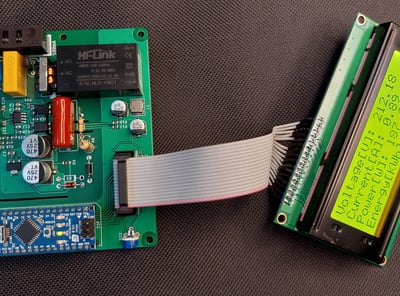
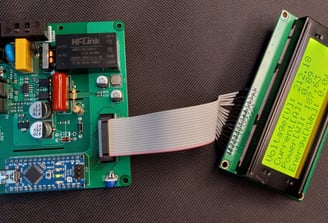
3. Efficiency and Reliability: With Omini’s state-of-the-art technology, energy meter PCBs offer fast, reliable, and accurate energy readings within minutes.
4. Energy Trend Analysis: By tracking energy consumption over time, users can identify trends and make informed decisions about energy efficiency adjustments.
5. Energy Management Applications: These PCBs are indispensable for energy management professionals, ensuring reliable data collection for improved energy conservation.
At Omini, we specialize in manufacturing high-quality energy meter PCBs, providing cutting-edge solutions for energy monitoring across a wide range of industries.
Why Choose Omini for Your Energy Meter PCB
When selecting a manufacturer for your energy meter PCBs, Omini stands out as the trusted choice. Here’s why:
1. Cost-effective Solutions: Choose Omini for your energy meter PCBs and enjoy high-quality, cost-efficient solutions designed to meet the needs of your project.
2. Expertise in Energy Meter PCB Manufacturing: With years of experience in PCB manufacturing, Omini delivers energy meter PCBs with unmatched precision, speed, and accuracy.
3. Reliability and Quality: Looking for energy meter PCBs that you can rely on? Omini is a leading provider in the PCB industry, offering competitively priced, high-quality energy meter PCBs tailored to your specific requirements.
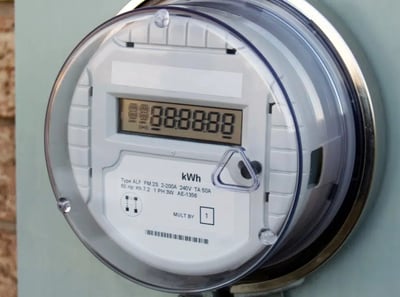
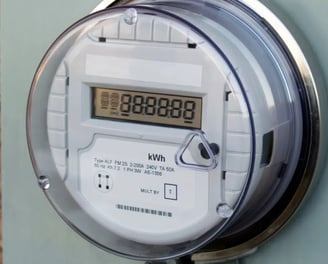
Partner with Omini today for innovative, reliable, and cost-effective energy meter PCBs that drive efficiency and performance in your energy management systems.
Electrical Layout of Energy Meter PCB
The electrical layout of an energy meter PCB plays a crucial role in its overall functionality. A well-designed energy meter PCB ensures accuracy and efficiency, minimizing the risk of errors. Here’s why a proper electrical layout is essential:
1. Isolation of Sensitive Elements: Sensitive components, such as the crystal that controls the clock, must be isolated from other parts of the circuit to prevent interference. The crystal’s low amplitude signal is susceptible to noise, electrostatic discharge, and external influences, so it must be placed in an isolated region away from other traces.
2. Signal Integrity: While analog signal transmission is possible for energy measurement, noise can disrupt the signal. Therefore, a filtering process is crucial to minimize noise. Additionally, circuit decoupling can help prevent electrostatic discharge (ESD), which can disrupt the PCB’s performance.
3. Material Selection: The choice of materials for both conductive and isolation layers is essential. Copper, a commonly used conductive material, offers excellent electrical conductivity, while FR-4 is a popular choice for insulation layers due to its high dielectric and low conductivity properties. Omini utilizes these materials to ensure high-quality energy meter PCBs.
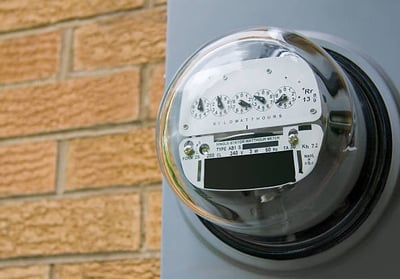
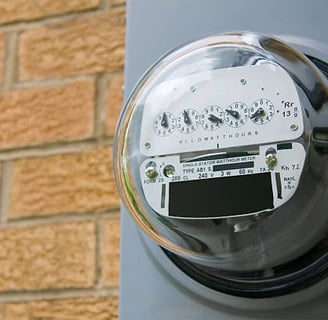
4. Design Considerations: The layout should prioritize adequate spacing, especially for sensitive components. Consideration of factors such as the board’s shape, size, and the number of layers is essential to achieving advanced functionality. A clear and organized layout ensures components are easily identifiable, making the PCB easier to work with.
At Omini, we specialize in designing and manufacturing energy meter PCBs that ensure optimal performance and reliability.
Key Considerations in Energy Meter PCB Design
When designing an energy meter PCB, various factors must be taken into account to ensure proper functionality. Here are the key design considerations:
1. Form Factor and Size: It is essential to select the correct size and form factor for the energy meter PCB. Proper placement of critical circuits, such as power sources, digital components, and current return lines, ensures electromagnetic compatibility and minimizes interference.
2. Layer Material: Many may ask, “Do energy meter PCBs contain conductive materials?” The answer is yes—without conductive materials, there can be no wiring on the board. Copper is commonly used due to its excellent conductivity, while an insulating layer of FR-4 provides necessary electrical isolation.
3. Component Placement: The positioning of components on the PCB is vital for ensuring reliable performance. Critical circuits, digital components, and power sources should be positioned carefully, with adequate spacing between components to ensure efficient soldering and functionality.
4. Trace Layout: The routing of traces is crucial for signal integrity. The space between traces should be at least twice the width of the trace itself. Shielding traces can help block external noise, and different grounding mechanisms can further minimize electromagnetic interference (EMI).
5. Electromagnetic Interference (EMI) Control: EMI can significantly affect the operation of an energy meter PCB. However, by incorporating various shielding techniques and components, such as ferrite cores, decoupling capacitors, and EMI filters, Omini ensures that energy meter PCBs function smoothly even in high-frequency electromagnetic environments.
The following measures are recommended to minimize EMI in the design of energy meter PCBs:
1. Use ferrite cores for power lines
2. Shield cables and tracks effectively
3. Implement ground planes
4. Increase trace widths and design symmetrical layouts
5. Optimize board stack-up design
6. Utilize EMI filters and suppressors
7. Properly use bypass capacitors
8. Appropriately place and size decoupling capacitors
9. Isolate sensitive components from noise sources
At Omini, we prioritize the quality and performance of energy meter PCBs by considering all these factors in our design process, ensuring a reliable and efficient product for energy management applications.
What Kinds of Components Are Required in Energy Meter PCB?
When designing an energy meter PCB, various components are required to ensure the board functions efficiently and reliably. Each component has a specific role, and no component can be substituted for another. Here’s a look at the essential components used in energy meter PCBs:
1. Voltage Regulator: Voltage stability is critical in energy meter applications. A voltage regulator ensures a steady voltage supply, even if the incoming voltage fluctuates.
2. Transducer: A transducer is essential for converting current values into voltage values, enabling accurate energy measurement.
3. Transistor: Transistors are crucial for switching applications, controlling the flow of electrical current in the energy meter circuit.
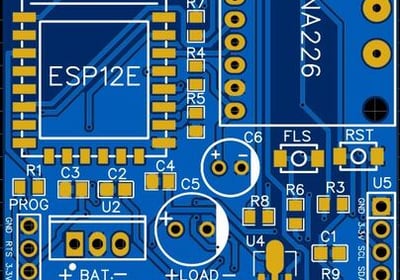
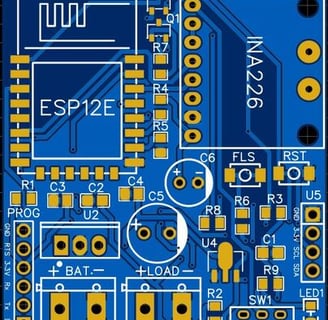
4. Transformers: Transformers are used to adjust the voltage in specific areas of the PCB, ensuring that different parts of the circuit receive the appropriate voltage.
5. Capacitor: A capacitor is used to store electrical charge, which helps regulate power supply and stabilize voltage within the energy meter PCB.
At Omini, we ensure that each of these components is selected and placed with precision to optimize the performance of energy meter PCBs.
Why Does An Energy Meter PCB Need Microcontrollers?
An important consideration in the design of energy meter PCBs is managing noise and interference, which can affect measurement accuracy. Microcontrollers play a key role in this process. Here’s why microcontrollers are crucial for energy meter PCBs:
1. Noise Elimination: Microcontrollers help to reduce noise generated within the energy meter, ensuring accurate readings even in the presence of electromagnetic interference.
2. Electrostatic Discharge Protection: By incorporating microcontrollers, the impact of electrostatic discharge (ESD) on the energy meter PCB is minimized, preventing misreadings and maintaining the integrity of the circuit.
3. Stable Operation: With the microcontroller managing noise and ESD, the energy meter PCB operates smoothly, ensuring reliable energy measurements over time.
At Omini, we leverage advanced microcontroller technology in our energy meter PCBs to ensure high performance and reliability in energy measurement applications.
How Can You Control the Quality of Energy Meter PCBs?
To ensure the energy meter PCBs we manufacture are of the highest quality and reliability, Omini employs several rigorous testing methods. These tests guarantee that our energy meter PCBs meet safety standards and perform reliably in all conditions. The four primary tests include:
1. Impulse Voltage Test: This test subjects the energy meter PCB to a high-voltage pulse for a short duration. The PCB must continue to function normally after the pulse is applied, ensuring it can withstand transient voltages without failure.
2. ESD (Electrostatic Discharge) Testing: Static electricity can cause significant damage to sensitive components in energy meter PCBs. Omini conducts ESD testing to ensure our energy meter PCBs can handle electrostatic discharge without being damaged, ensuring safe and reliable operation.
3. AC Voltage Insulation Test: Before installation, Omini performs the AC voltage insulation test to detect potential insulation failures that could be caused by external factors like dust or moisture. This test ensures the energy meter PCB is safe and free from insulation defects.
4. Burst Test: The burst test is designed to assess the energy meter PCB’s ability to handle high levels of electrical energy before failure. This test helps Omini identify potential weak points in the design and make necessary improvements to ensure the product meets safety standards.
At Omini, these rigorous testing methods help us deliver energy meter PCBs that are both reliable and safe, meeting the highest industry standards for energy management applications.
Why Do You Need to Control Mutual Inductance in Energy Meter PCBs?
Controlling mutual inductance in energy meter PCBs is crucial for ensuring accurate and reliable energy measurement. As emphasized by Omini’s experts, mutual inductance creates a voltage across a conductor when there is a change in current in a nearby coil. This phenomenon plays a significant role in allowing energy meters to measure energy consumption accurately. Here’s why it’s essential to control mutual inductance in energy meter PCBs:
1. Accurate Energy Measurement: By managing mutual inductance, energy meter PCBs can deliver precise energy readings, ensuring that energy usage is measured correctly across appliances, buildings, and other energy-consuming systems.
2. Reliable Performance: Proper control of mutual inductance ensures that energy meter PCBs maintain reliable operation over time, avoiding measurement errors and inconsistencies.
3. Enhanced Energy Efficiency: Effective mutual inductance control helps to minimize energy waste, allowing energy providers to better manage energy usage. This leads to more efficient energy distribution and consumption.
4. Compliance with Industry Standards: By incorporating the right components, such as resistors and capacitors, Omini ensures that energy meter PCBs meet widely accepted energy measurement standards, delivering high-quality, accurate readings.
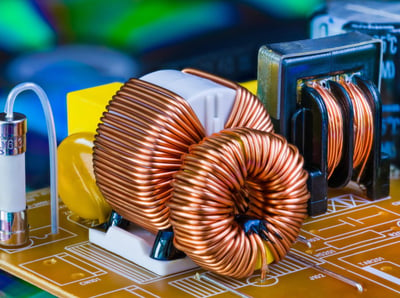
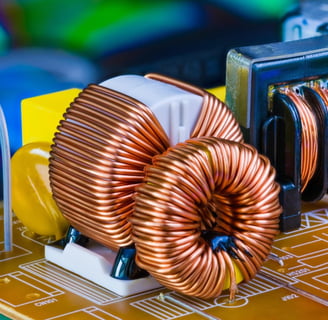
At Omini, we focus on precise control of mutual inductance in energy meter PCBs to provide superior energy measurement solutions for our customers.
What Materials Are Used to Make Energy Meter PCBs?
When it comes to manufacturing energy meter PCBs, the choice of materials is crucial for ensuring both performance and durability. As noted by industry experts, Omini uses a combination of high-quality materials in the production of energy meter PCBs. Here’s an overview of the materials commonly used:
1. Copper: Copper is a primary material in energy meter PCBs due to its excellent electrical conductivity and cost-effectiveness. Copper traces are essential for transmitting electrical signals efficiently.
2. Epoxy: Epoxy is used as an insulating material to protect the copper traces from external forces, ensuring the energy meter PCB remains functional and durable.
3. Other Metals: In some cases, metals such as silver, gold, and platinum may be incorporated into the energy meter PCB design to enhance energy efficiency and reduce energy losses. These metals provide superior conductivity and performance.
4. Compliance with Industry Standards: All materials used in energy meter PCBs must meet strict industry standards to ensure high-quality, reliable, and safe performance. Omini ensures that the materials used in every energy meter PCB we produce conform to these standards.
At Omini, we carefully select the best materials for energy meter PCBs to ensure longevity, efficiency, and accuracy in energy measurement.
How to Make a Correct LCD Layout on an Energy Meter PCB?
Designing an effective LCD layout on an energy meter PCB is essential for ensuring the meter provides accurate and easy-to-read energy usage data. According to Omini’s experts, the layout must be designed carefully to display energy readings clearly and accurately. Here are the key considerations when designing an LCD layout for energy meter PCBs:
1. Microcontroller Integration: The microcontroller plays a central role in processing energy measurement data and sending the information to the LCD for display.
2. Power Supply Management: A stable power supply is crucial to ensure that the LCD and other components function correctly. Proper voltage regulation is necessary to maintain consistent readings.
3. Component Placement: Proper placement of resistors, capacitors, and other supporting components ensures smooth operation and prevents interference, enabling the LCD to display accurate energy readings.
4. Protection Circuits: To avoid inaccurate readings or potential damage, the design should include protection circuits that safeguard the energy meter PCB and ensure the LCD displays correct data consistently.
At Omini, we specialize in designing energy meter PCBs with optimized LCD layouts, ensuring accurate, easy-to-read energy consumption data for users.
Omini Energy Meter PCB Assembling
When assembling energy meter PCBs, both surface mounting and through-hole mounting techniques can be used to place each component. However, before the components are assembled onto the PCB, it is crucial to mark the exact locations where each component will be attached. Once the electronic parts are properly positioned, the soldering process can begin.
There are two common soldering methods:
1. Manual Soldering: This involves a skilled worker soldering components by hand. Manual soldering requires expertise to ensure precision and reliability.
2. Reflow Soldering: The PCB board passes through an oven where heat is applied to solder the components.
After soldering, a thorough inspection of the soldering quality is essential. Any defective boards must be identified and removed to maintain the high standards of your energy meter PCBs.
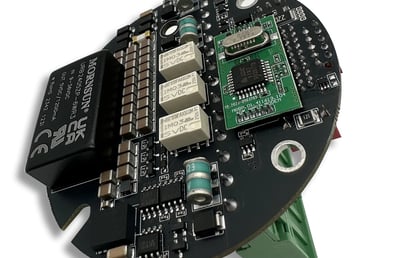
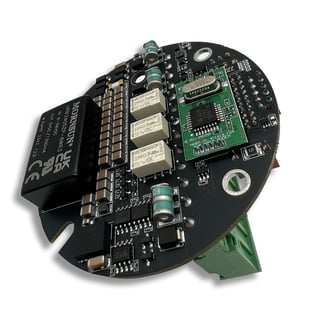
Omini Energy Meter PCB Performance Factors
Several key factors impact the performance of Omini energy meter PCBs. Understanding and optimizing these factors are crucial for designing energy-efficient and reliable systems.
1. Inductance of Coils
• The inductance of coils is a critical factor influencing energy meter performance. Coils can be made from various materials, and their efficiency depends on limiting the air space around the electrical conductors, known as the fill factor.
• Using round wires results in a central gap in the coil, but increasing the number of turns can compensate for this gap. To further enhance the fill factor, rectangular or square wires can be used.
• The material of the coil also affects inductance. Higher permeability materials result in greater inductance, which can improve the performance and resistance capabilities of the energy meter.
2. Electrostatic Discharge (ESD)
• ESD is a crucial factor in the overall performance of energy meters. Several factors, such as voltage, gap width, and discharge time, can influence ESD testing.
• An electrostatic discharge (ESD) is an electrical discharge that affects the PCB of an electrical appliance. The required voltage for an ESD discharge is directly related to the applied voltage and the strength of the electric field.
• In most cases, the arc length plays a more significant role in creating higher voltages, which can potentially harm the PCB and impact the meter’s performance.
3. Power Source
• The power source is an essential element of Omini energy meter PCBs, supplying the necessary energy to accurately measure and manage energy consumption. Power sources can vary, including electricity, solar energy, wind energy, or fuel cells.
• Depending on the specific application, the power source must be tailored to provide the required voltage, current, and power levels to meet the energy meter’s needs.
4. Design Complexity
• The design complexity of energy meter PCBs is a critical consideration. According to experts at Omini, the complexity of the design is determined by the number of components and layers required in the energy meter PCB.
• For example, an energy meter may need more components to measure voltage levels accurately or additional layers for better heat dissipation and energy management.
5. Copper Layers in Construction
• The number of copper layers used in the construction of energy meter PCBs plays a significant role in the board’s performance. Omini has vast experience in designing PCBs with multiple copper layers, which are crucial for establishing electrical connections between components.
• More layers enhance the PCB’s ability to manage power, support complex circuits, and improve overall energy metering functionality. The more layers a PCB has, the more sophisticated the design and manufacturing process becomes.
Contacts
Email: sales@ominipcba.com
Mobile: +86-185-7640-5228
Copyright © 2007-2025. Omini Electronics Limited. All rights reserved.
Head Office: +86-755-2357-1819
Products & Services
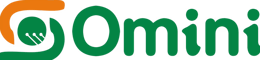
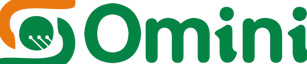
Office Address: No. 605, Tongxin Technology Building, Bao’an Avenue, Bao’an District, Shenzhen, Guangdong, China.
SMT Plant: A Building, Longwangmiao Industrial Park, Baishixia Community, Fuyong Street, Bao'an District, Shenzhen, China.
Omini Electronics Limited is an expert in trusted PCB Fabricaton and PCB Assembly in China since 2007. We have served over 1000 global customers with high-quality, low to medium-volume production. Certified by UL (E532498), ISO9001:2015, and ISO13485:2016, we offer expert electronics manufacturing services, including PCB manufacturing, assembly, and contract manufacturing, ensuring top-tier quality and precision in every project.