Phone: +86-755-2357-1819 Mobile: +86-185-7640-5228 Email: sales@ominipcba.com whatsapp: +8618576405228
Omini: Your One-Stop Electronic Manufacturing Solution
Omini specializes in delivering comprehensive solutions for all your PCB needs. From design to production, we provide top-notch services tailored to meet industry standards and exceed customer expectations.
PCB Fabrication: High-quality circuit board manufacturing tailored to your specifications
Component Sourcing & Turnkey PCB Assembly: End-to-end solutions for seamless production
Box Build Assembly & Functional Testing: Complete product assembly with rigorous performance testing
Repair, Rework & Reverse Engineering: Expert support to optimize and extend product life cycles
Certified Excellence: ISO9001:2015, ISO13485:2016 Certified, and UL Listed for safety and quality
Advanced Testing Capabilities: 100% E-test, AOI, X-RAY, ICT & FCT to ensure flawless products
Flexible & Affordable Solutions: No MOQ with competitive pricing to fit your budget
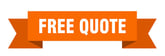
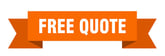
Driving Innovation in PCB Manufacturing: The Future of Electronics
Offering PCB fabrication, assembly, testing, and repair services with competitive pricing and no MOQ.As electronic technology continues to evolve, the demand for advanced manufacturing solutions in electronic devices and components has skyrocketed. The trend toward miniaturization has revolutionized the industry—components are becoming smaller, yet more powerful, enabling devices to deliver greater functionality, portability, and flexibility.
Bulky, single-purpose electronics are a thing of the past. Today, sleek, compact devices perform multiple tasks simultaneously, transforming the way we live and work. This shift has not only redefined electronic devices but has also driven significant advancements in the electronics manufacturing sector, particularly in PCB technology.
At Omini, we stay ahead of the curve, offering cutting-edge PCB manufacturing solutions to meet the ever-changing demands of modern electronics.
What is Electronics Manufacturing?
Electronics manufacturing refers to the complete process of producing electronic devices, encompassing every stage from design to distribution. It includes critical processes such as PCB fabrication, PCB assembly, electromechanical assembly, testing, inspection, and quality assurance. Beyond production, electronics manufacturing also covers electronic design, packaging, and final distribution to market.
As a key player in the industry, Electronics Manufacturing Services (EMS) providers like Omini deliver full turnkey solutions tailored to the needs of brand owners and Original Equipment Manufacturers (OEMs). From precision PCB production to streamlined assembly, Omini ensures high-quality, reliable solutions for modern electronics manufacturing.

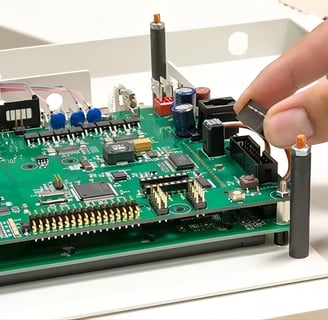
Parts and Components in Electronics Manufacturing
Before diving into the processes involved in electronics manufacturing, it’s important to first explore the essential materials and components that form the backbone of every electronic device.
Printed Circuit Boards (PCBs)
The Printed Circuit Board (PCB) is one of the most critical components in electronics manufacturing. It serves as the foundation that physically and electrically connects various electronic components. Since their introduction in the 1950s, PCBs have evolved significantly, particularly after World War II, when consumer electronics saw a surge in demand.
A typical PCB consists of a substrate made from dielectric material, with copper conductors laminated onto it. These copper layers create the electrical paths and provide the medium for soldering components.
PCBs can be classified into several types based on their structure:
• Single-Sided PCB: Featuring a single conductive layer on one side, single-sided PCBs are the simplest and most cost-effective option for many applications.
• Double-Sided PCB: Double-sided PCBs have conductive layers on both sides of the board. Vias (small holes) are drilled to connect the two sides electrically, offering more versatility for complex designs.
• Multi-Layered PCB: The most complex of the three, multi-layered PCBs consist of multiple copper layers stacked together with insulating substrates. These layers are interconnected using vias and conductive tracks, enabling highly advanced designs for intricate electronics.
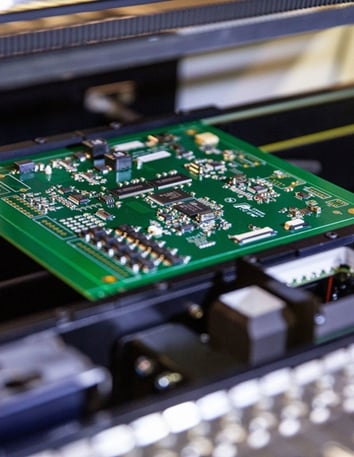
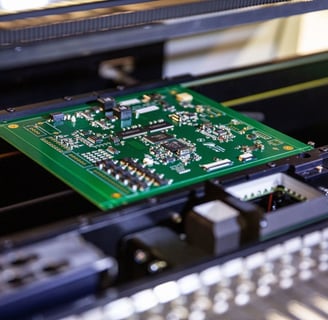
Electronic Components
Various electronic components with specific functions make up a complete electronic device. These components are broadly categorized into two groups: passive and active components.
• Passive Components: Examples of passive components include resistors, capacitors, and inductors. These components don’t amplify electrical current but can store, dissipate, or filter energy.
• Active Components: Active components are essential for circuit operation, as they amplify or control the flow of electrical current. Common active components include diodes, integrated circuits (ICs), and power supplies.
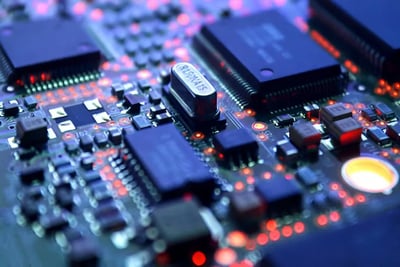
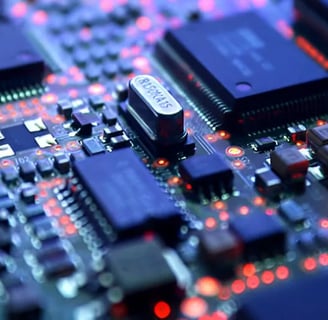
Mechanical and Electromechanical Parts
In addition to essential electronic components, electronics manufacturing also involves the integration of mechanical and electromechanical parts. These components perform both mechanical and electrical functions, ensuring the smooth operation of modern electronic systems. Key examples of these critical parts include actuators, motors, solenoids, and pneumatic components. Each plays a vital role in enhancing the performance and functionality of complex electronic devices, helping to drive innovation in industries ranging from consumer electronics to industrial automation.
At Omini, we specialize in providing precision manufacturing solutions for both electronic and electromechanical components, ensuring that your devices are built to meet the highest standards of performance and reliability.
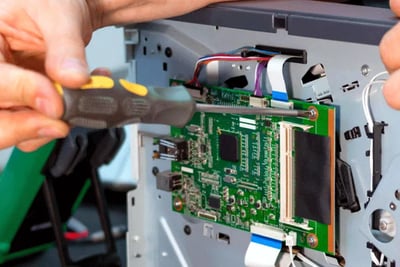
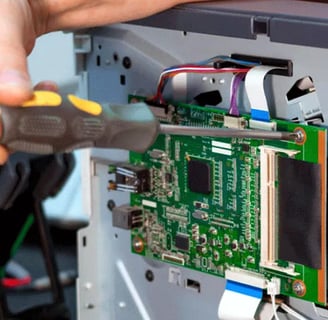
The Basic Electronics Manufacturing Processes
Electronics manufacturing is a multifaceted process, encompassing everything from PCB fabrication and assembly to electromechanical integration and comprehensive testing. Only experienced manufacturers can deliver high-quality Electronics Manufacturing Services (EMS) that meet the stringent requirements of modern devices. In this guide, we will walk you through the fundamental processes involved in electronics manufacturing.
PCB Fabrication Process
The PCB fabrication process is a critical step in electronics manufacturing. This process involves multiple stages to create the printed circuit boards that serve as the foundation for electronic devices.
• Inner Layer Fabrication: Using a virtual design file, the inner layers of the PCB are exposed to UV light through a photoresist process. The copper areas not part of the circuit are etched away, leaving the conductive traces.
• Lamination: For multi-layer PCBs, the inner layers are bonded together with prepreg, a fiberglass material with partially cured resin, at a specific temperature and pressure to form a rigid stack-up.
• Drilling: Holes are drilled into the PCB using automated equipment, following reference drill data. This step ensures accurate hole placement for component leads and vias.
• Through-Hole Plating: The drilled holes are cleaned and copper-plated to create conductive paths that connect different PCB layers and components.
• Outer Layer Imaging: Similar to inner layer fabrication, a photoresist film is used to expose the outer copper layers to UV light, then developed and etched.
• Solder Masking: A solder mask is applied to the PCB to prevent unwanted solder bridges. The most common method is Liquid Photo Imageable Solder Mask (LPI), which uses UV exposure to create a protective layer.
• Surface Finish: To protect copper pads from oxidation, surface finish techniques like Hot Air Solder Levelling (HASL), Organic Solderability Preservative (OSP), and Electroless Nickel Immersion Gold (ENIG) are applied.
• Silkscreen: Printed alphanumeric codes, component labels, and fiducials are added to the PCB using a silk screening process, ensuring accurate assembly and placement.
• Testing: Once fabricated, the bare PCB undergoes testing for continuity and to detect any potential electrical faults, such as opens and shorts.
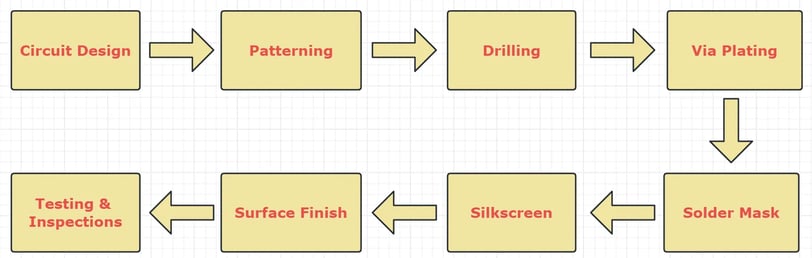
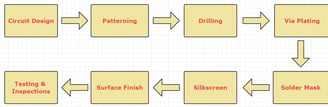
PCB Assembly Process
As electronic devices become increasingly complex, the assembly process has evolved to incorporate various methods. The main assembly techniques used in electronics manufacturing include Through Hole Technology (THT), Surface Mount Technology (SMT), and Mixed SMT and THT Assembly.
Through Hole Technology (THT)
involves inserting leads or pins through holes in the PCB to attach components. The leads are then soldered using wave soldering, a traditional method in which the PCB is passed through a molten wave of solder to secure the components.
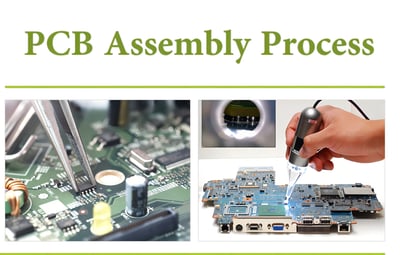
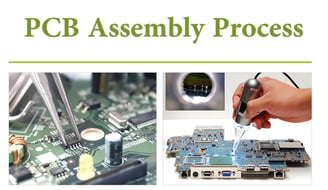
Surface Mount Technology (SMT)
is a modern technique where components are mounted directly onto the surface of the PCB. SMT allows for high-speed automated assembly, improving efficiency. Key processes involved in SMT include:
• Stencil Printing: A solder paste is applied to the PCB through a stencil, ensuring uniform distribution.
• Solder Paste Inspection (SPI): The quality of the solder paste application is inspected to ensure proper volume and placement.
• Component Placement: Using Pick and Place machines, components are rapidly placed on the PCB. These machines are programmed to place components with high accuracy, even for small and complex parts.
• Solder Reflow: The PCB is passed through a reflow oven where the solder paste melts, creating electrical connections between the PCB and components.
Mixed SMT and THT Assembly
For some designs, both SMT and THT technologies are used. This often occurs in double-sided PCBs, where one side uses through-hole components and the other side uses surface-mount devices. The assembly process requires both reflow and wave soldering, and the steps are carefully managed to ensure precision and performance.
Electromechanical Assembly
In electromechanical assembly, the PCB is integrated with other mechanical components, such as connectors, power supplies, and sensors, to form a complete system. These systems are then enclosed in custom or off-the-shelf housings to protect the internal electronics. The final assembly can involve the use of advanced robotic machines for precise positioning, or manual assembly for more complex tasks, which may require highly skilled technicians.
Testing and Inspections
Testing and quality control are essential to ensure that electronic devices perform as expected. Below are the primary testing and inspection processes in electronics manufacturing.
Automated Optical Inspection (AOI)
AOI uses advanced imaging systems to visually inspect PCBs for defects. This method has replaced manual inspection due to its superior accuracy and ability to detect even the smallest issues.
Functional Testing
Functional testing simulates the product’s operational environment to ensure it responds correctly under real-world conditions. It uses custom test fixtures, hardware, and software to perform comprehensive evaluations.
Burn-In Testing
Involves subjecting finished products to extended stress tests in a controlled environment, typically with elevated temperature and voltage. This process helps identify latent defects by stressing the components, ensuring the reliability of the final product.
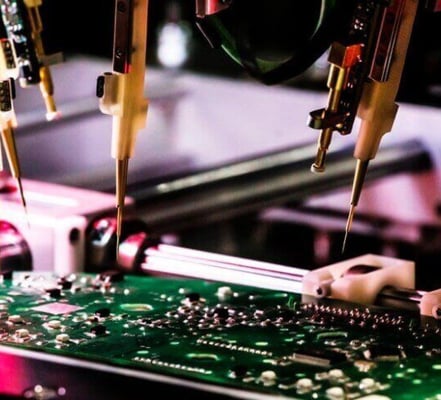
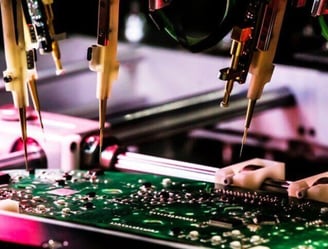
At Omini, we leverage years of experience and advanced technologies to provide high-quality PCB manufacturing and electronics assembly services. Our commitment to precision, quality, and efficiency ensures that every product meets the highest standards. Whether you need PCB fabrication, SMT assembly, or electromechanical integration, Omini is your trusted partner in the electronics manufacturing industry.
Contacts
Email: sales@ominipcba.com
Mobile: +86-185-7640-5228
Copyright © 2007-2025. Omini Electronics Limited. All rights reserved.
Head Office: +86-755-2357-1819
Products & Services
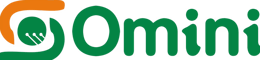
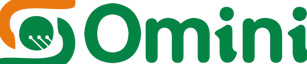
Office Address: No. 605, Tongxin Technology Building, Bao’an Avenue, Bao’an District, Shenzhen, Guangdong, China.
SMT Plant: A Building, Longwangmiao Industrial Park, Baishixia Community, Fuyong Street, Bao'an District, Shenzhen, China.
Omini Electronics Limited is an expert in trusted PCB Fabricaton and PCB Assembly in China since 2007. We have served over 1000 global customers with high-quality, low to medium-volume production. Certified by UL (E532498), ISO9001:2015, and ISO13485:2016, we offer expert electronics manufacturing services, including PCB manufacturing, assembly, and contract manufacturing, ensuring top-tier quality and precision in every project.