Phone: +86-755-2357-1819 Mobile: +86-185-7640-5228 Email: sales@ominipcba.com whatsapp: +8618576405228
HDI PCB
At Omini, we specialize in providing top-tier HDI PCBs designed to meet the most demanding requirements of modern electronics. Our HDI PCBs deliver exceptional performance, precision, and reliability, making us your trusted partner for high-quality solutions.
Rigid HDI & Rigid-Flex HDI: Omini offers Rigid and Rigid-Flex HDI PCBs, optimizing space and performance with high-density interconnections.
i+N+i (i≥2) HDI, Any Layer HDI: Our HDI PCBs support i+N+i designs for multi-layer configurations in complex circuits.
Blind & Buried Vias, Stacked & Staggered Vias: We provide advanced via technologies for high-density designs and optimal electrical performance.
Conductive & Non-Conductive Via Plugging: Omini offers Conductive and Non-Conductive Via Plugging for precise control and enhanced mechanical strength.
Min. 1.5/1.5 mil Line/Space: We ensure 1.5/1.5 mil line/space for high-performance HDI PCB designs.
Back Drill, Backplane, Embedded Devices, IC Substrate: Omini delivers Back Drill, Backplane, Embedded Devices, and IC Substrate solutions for HDI PCBs.
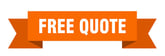
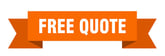
What is HDI PCB?
HDI PCB, which stands for High-Density Interconnect Printed Circuit Board, is a type of PCB that utilizes advanced techniques to achieve higher component density and smaller trace widths. At Omini, we specialize in providing high-quality HDI PCBs that are designed to maximize the functionality and efficiency of modern electronic devices.
1. Smaller Traces and Drills: HDI PCBs feature thinner traces and smaller drill holes, which allow more components to be packed into the same area. This results in more efficient use of space for routing and other purposes.
2. Micro Via, Blind Via, and Buried Via Technology: Omini leverages advanced via technologies, including micro vias, blind vias, and buried vias, replacing traditional through-hole vias. This enhances the overall density and reliability of the HDI PCB design.
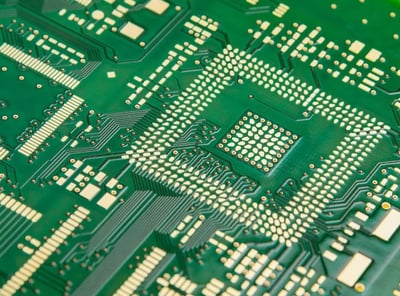
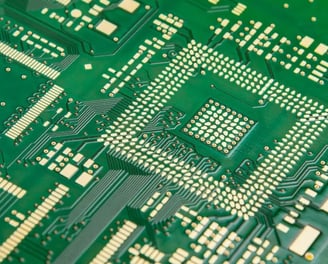
3. Higher Component Density: The HDI PCB technology enables the integration of more components, such as ICs, into the same board, allowing for smaller and more powerful electronic devices.
4. Low Current Carrying and High Performance: The HDI PCB design features very low current-carrying traces, which are essential for high-performance applications in a variety of industries, from consumer electronics to medical devices.
5. Compliance with IPC Standards: Omini ensures that all of our HDI PCBs are designed and manufactured according to the strictest industry standards, including IPC-2315, IPC-2226, IPC-4104, and IPC-6016, ensuring quality and reliability.
Main Features of HDI PCB
HDI PCBs are known for their advanced design features, which include a higher layer count, smaller trace widths, and unique via technologies such as blind vias and buried vias. At Omini, we specialize in providing high-quality HDI PCBs that meet the demands of modern electronic applications. Below are the main features of HDI PCBs:
1. Higher Layer Count: More Than 4 Layers
Omini designs HDI PCBs with a higher layer count, typically ranging from 6 to 12 layers. This enables complex functions and more interconnections in a compact space, with at least 4 layers being standard for HDI PCBs.
2. Small Trace Width and Spacing: Less Than 4 mil
For HDI PCBs, smaller traces and tighter spacing are essential to fit more components into a small area. Omini ensures trace width and spacing of 4 mil or below in most HDI PCBs, and even down to 2 mil in some designs, providing high-density routing for sophisticated circuit requirements.


3. Used Micro Vias, Blind Vias, and Buried Vias
Omini leverages micro vias, blind vias, and buried vias in HDI PCBs, enhancing circuit density and performance. These advanced via technologies replace traditional through-hole vias, allowing for more effective routing and compact board designs.
• Micro Via: Small vias (less than 0.15mm or 6 mils) used for high-density applications.
• Blind Via: Vias drilled from the top or bottom layers to inner layers, visible from one side only.
• Buried Via: Vias located within the inner layers, invisible from the sides of the PCB.
• Staggered Via: Micro vias arranged step-by-step in a staggered configuration.
• Stacked Via: Micro vias stacked vertically in multiple layers to save space and enhance density.
4. Multiple Stack-ups and Lamination
Omini uses multiple stack-ups and lamination rounds to achieve the high-density designs required for HDI PCBs. This process allows us to incorporate multiple blind and buried vias in HDI PCBs, enhancing routing flexibility.
• Layer Construction: Several rounds of stack-ups and lamination are used to achieve the required design specifications.
• Etching Process: The non-conductive parts of the traces are etched away using ferric chloride, leaving behind the conducting parts.
• Vias Drilling: Vias are drilled with mechanical or laser methods, using a chemical process for high-density areas.
• Metallization and Interconnect: The inner interconnects are formed through metallization, ensuring excellent electrical conductivity.
Omini ensures that all HDI PCBs are manufactured to the highest standards, optimizing them for performance, durability, and compactness.
Advantages of HDI Printed Circuit Board
HDI Printed Circuit Boards are integral to complex system-based applications, including PCs, smartphones, tablets, cameras, and advanced technologies like space stations and supercomputers. At Omini, we provide high-performance HDI PCBs that offer a range of significant benefits:
1. Size and Weight: Compact Design with Lightweight Features
One of the main advantages of HDI PCBs is their compact size and light weight. Omini’s HDI PCBs are designed with a small footprint while maintaining all the essential functional features, making them ideal for space-constrained applications in consumer electronics and aerospace.
2. Low Cost: Reduced Overall Costs for Complex Designs
While the initial manufacturing cost of HDI PCBs may seem high, the overall cost is reduced when considering the smaller board size, fewer components, and more efficient design. This makes HDI PCBs from Omini a cost-effective choice for modern electronic products, optimizing both production and assembly costs.
3. Performance & Reliability: Enhanced Signal Integrity
HDI PCBs deliver superior performance with reduced noise and minimal signal integrity issues. By using advanced technologies like micro vias and buried vias instead of traditional through-hole vias, Omini ensures higher signal quality, longer life cycles, and increased reliability. The reduced form factor and improved aspect ratio also enhance performance in high-frequency applications.
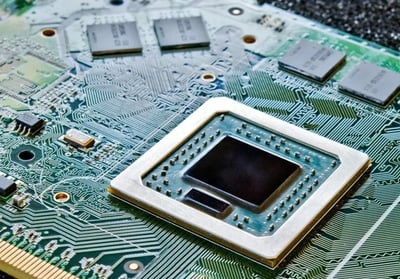
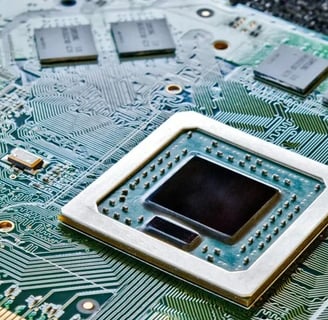
4. Time to Market: Faster Production and Testing
The production process for HDI PCBs at Omini is optimized for efficiency, allowing for faster time-to-market for compact applications. With our state-of-the-art manufacturing processes, we provide rapid production cycles and thorough testing to ensure high-quality, reliable boards.
Applications of High-Density Interconnect (HDI) PCB
High-Density Interconnect (HDI) PCBs are widely used in various industries due to their compact size, superior performance, and reliability. At Omini, we specialize in providing HDI PCBs for a diverse range of applications:
1. Automotive Applications and Subsystems
HDI PCBs are essential in automotive systems, such as Vehicle Control Units and display driver designs. These systems require high-speed processors and RAMs, demanding high-density routing for seamless operation. Omini’s HDI PCBs ensure precise data transmission, avoid crosstalk, and support complex telematics and computing systems in modern vehicles.
2. Commercial Products
In commercial electronics, products like smartphones, tablets, smartwatches, augmented reality (AR), and virtual reality (VR) devices rely on HDI PCBs for their high-performance, high-definition displays. Omini provides HDI PCB solutions that optimize performance and space utilization for cutting-edge consumer electronics.
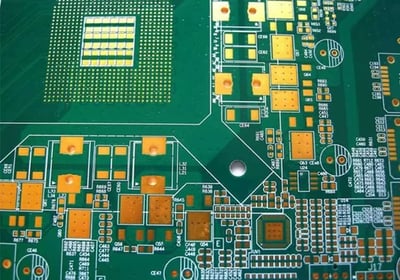
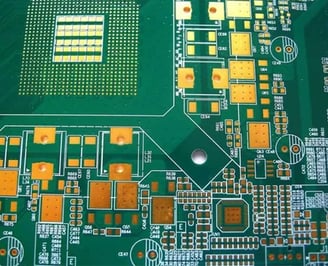
3. Defense and Aerospace Applications
In defense and aerospace systems, HDI PCBs are used to power supercomputing systems and integrate highly sensitive devices. These HDI PCBs are lightweight and compact, making them ideal for use in aviation and other high-performance environments. Omini ensures that our HDI PCBs meet the rigorous demands of precision data and communication systems in these industries.
4. Healthcare and Medical Devices
HDI PCBs play a critical role in medical devices, such as robotic arms, colonoscopy instruments, and precision ophthalmic devices. These devices require small, compact HDI PCBs to ensure high precision, reliability, and safety. Omini provides HDI PCBs that meet stringent medical standards, ensuring that medical tools are both precise and safe for use in sensitive environments.
Challenges of HDI Circuit Boards
Designing HDI circuit boards presents a number of unique challenges due to their high-density, complex nature. These challenges include:
1. Limited PCB Area
The compact size of HDI PCBs requires efficient use of space to accommodate high-density traces and components. Omini addresses these constraints with precise, optimized layouts that maximize available board space.
2. Smaller Components and Tightly Packed Arrangements
In HDI PCBs, components are smaller and arranged more densely than in traditional PCBs, making precise placement and routing more difficult. Omini ensures that these challenges are met through advanced design techniques and careful component placement.
3. Both Sides of the PCB Are Packed with Components
With both sides of HDI PCBs often densely populated with components, the complexity of routing increases significantly. Omini’s expertise in HDI PCB design enables us to efficiently manage component placement and routing for optimal performance.
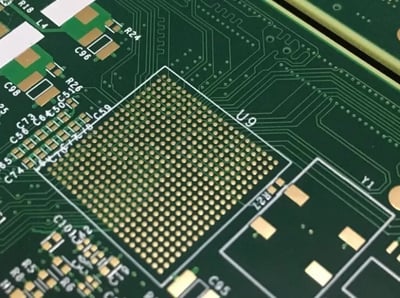
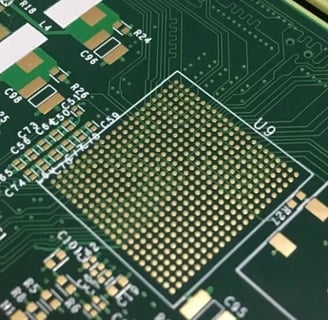
4. Longer Trace Lengths and Increased Delay Time
Due to the complexity of HDI PCB designs, trace lengths may be longer, which can result in higher signal delay times. Omini minimizes these issues by optimizing trace lengths and using advanced materials for faster signal transmission.
5. Complex Routing and Increased Number of Nets
HDI PCBs require more intricate routing, with a larger number of nets to manage. Omini employs state-of-the-art PCB design software and routing techniques to handle these complexities and ensure signal integrity and reliability.
To overcome these challenges, Omini utilizes advanced PCB design software and adheres to strict component placement and routing rules. Our experienced team ensures that all constraints are met, delivering HDI circuit boards that are high-performing and reliable.
Key Considerations of HDI PCB Design and Manufacturing
Designing High-Density Interconnect (HDI) PCBs requires careful consideration of various factors, including components, stack-up, material properties, design rules, and manufacturing capabilities. Below are the key considerations when designing and manufacturing HDI PCBs:
1. Layer Count Determination: The layer count of an HDI PCB is often dictated by BGA IC recommendations and depends on net crossover, trace length, and specific application requirements.
2. Design Rules for Manufacturing (DFM): Omini ensures that manufacturing capabilities are aligned with the design rules to meet the required PCB stack-up. This includes designing for manufacturability and ensuring the board meets all pre-requisites.
3. Via Properties and Usage: The selection and placement of vias across all layers are critical for interconnecting nets. This determines the thickness and layer count of the HDI multilayer PCB, impacting both performance and reliability.
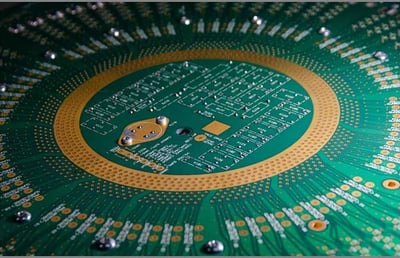
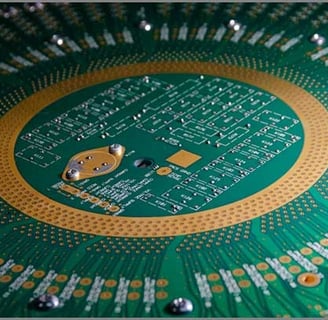
4. Environmental Stress and Reliability: The assembly process must ensure that the HDI PCB can withstand real-world environmental stress. Omini emphasizes thorough reliability testing to ensure that the board will not fail under operational conditions.
5. Printing and Component Assembly: Omini focuses on precision in trace width, teardrops, and component assembly. These factors ensure that the design is manufacturable, routable, and reliable, leading to a high-performing final product.
Manufacturing Constraints in HDI Circuit Boards
There are several key differences in the manufacturing processes of standard PCBs and HDI printed circuit boards. The manufacturing capability of these designs must align with the feasibility requirements to avoid performance and accuracy issues. While PCB design software can handle smaller components and design constraints, the design must meet Design for Manufacturing (DFM) requirements to ensure compatibility with the manufacturing process. Here are the key substrate considerations that Omini keeps in mind before designing the board:
1. Core Material Selection: The core material of an HDI PCB must support both electrical and mechanical performance requirements, ensuring the substrate’s properties are suitable for the application.
2. Copper Adhesion and Reliability: The adhesion of copper to the dielectric material must be stable and reliable, as it impacts the overall performance and longevity of the PCB.
3. Dielectric Spacing: The dielectric spacing between conductive layers should be stable and consistent to maintain signal integrity and prevent electrical failure.
4. Thermal Properties: Dielectric materials must meet the thermal requirements of the PCB, including the ability to withstand high temperatures during operation and manufacturing processes.
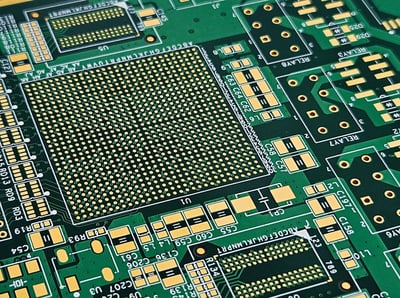
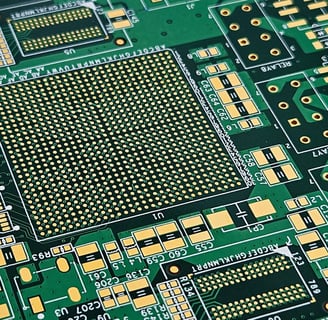
5. Thermal Shock Resistance: The dielectric material must be capable of handling thermal shocks and cycles, especially in applications that undergo frequent temperature changes.
6. High TG Requirements: The material should offer high glass transition (TG) properties, which are essential for applications involving metal contact, wire bonding, or rework.
7. Handling Thermal Vias: The dielectric material must support the manufacturing of thermal vias, micro vias, buried vias, and blind vias, all of which are crucial for high-density interconnect (HDI) designs.
Omini ensures that all HDI circuit boards comply with industry standards, including IPC – 4101B and IPC – 4104A. We use a range of materials such as photosensitive liquid dielectrics, polyamide flexible films, thermally cured dry films, and resin-coated copper foil to ensure high-quality manufacturing.
Why Choose Omini as Your HDI PCB Partner?
As the HDI circuit board industry has rapidly developed globally, China has become a major hub for HDI PCB manufacturing. Among the top HDI PCB manufacturers in China, Omini stands out for delivering high-quality, reliable HDI printed circuit boards, leveraging cutting-edge technologies to meet diverse customer needs. Here’s why you should choose Omini as your trusted HDI PCB partner:
1. Highest Industrial Quality Standards
Omini ensures that all production processes comply with the latest quality management systems, including ISO9001, ISO13485, and TS16949 certifications. We meet IPC-A-600 Class 2 standards and, for specialized industries like medical, automotive, and aerospace, we adhere to Class 3 and 3A standards.
2. Advanced Equipment and Technology
At Omini, we continuously invest in advanced equipment and technologies to meet the evolving demands of the HDI PCB market. Our capabilities include manufacturing complex designs such as staggered and stacked blind vias, VIPPO technology, any-layer connections, and via plugging.
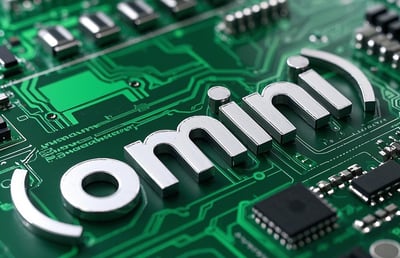
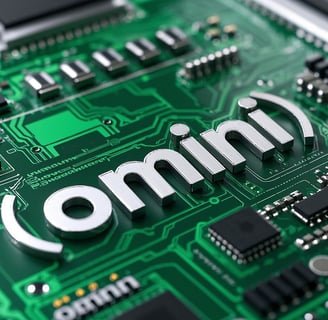
3. Accepting Orders as Low as One Piece
Unlike many other HDI PCB manufacturers, Omini has no minimum order quantity requirements, allowing you to order as few as one piece. This flexibility ensures you can collaborate with us for both small and large-scale projects.
4. One-Stop Turnkey Services
Omini offers a seamless one-stop service, handling the entire process from material selection, PCB design, and HDI PCB manufacturing to assembly, packaging, and shipping. With Omini, you can sit back and wait for your products to arrive without worrying about any details.
5. Perfect Pre-Sales and After-Sales Services
Our dedicated customer service and technical teams are available to assist you at every step. From pre-sales consultations to post-sales support, Omini ensures a smooth and hassle-free experience. If any issues arise with product quality, we’re committed to rework or compensation to maintain your satisfaction.
Contacts
Email: sales@ominipcba.com
Mobile: +86-185-7640-5228
Copyright © 2007-2025. Omini Electronics Limited. All rights reserved.
Head Office: +86-755-2357-1819
Products & Services
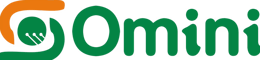
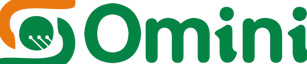
Office Address: No. 605, Tongxin Technology Building, Bao’an Avenue, Bao’an District, Shenzhen, Guangdong, China.
SMT Plant: A Building, Longwangmiao Industrial Park, Baishixia Community, Fuyong Street, Bao'an District, Shenzhen, China.
Omini Electronics Limited is an expert in trusted PCB Fabricaton and PCB Assembly in China since 2007. We have served over 1000 global customers with high-quality, low to medium-volume production. Certified by UL (E532498), ISO9001:2015, and ISO13485:2016, we offer expert electronics manufacturing services, including PCB manufacturing, assembly, and contract manufacturing, ensuring top-tier quality and precision in every project.