Phone: +86-755-2357-1819 Mobile: +86-185-7640-5228 Email: sales@ominipcba.com whatsapp: +8618576405228
PCB Manufacturing – Over 16 Years of Expertise
Omini offers advanced PCB Manufacturing services with over 16 years of experience in the industry. We specialize in producing high-quality, reliable PCBs tailored to meet the most demanding requirements
1-40+ Layers – Rigid, Flex, and Rigid-Flex PCBs to Suit Diverse Applications: We provide 1-40+ layer PCBs in rigid, flexible, and rigid-flex designs for various applications.
Impedance Control, Back Drilling, and Heavy Copper (40 oz) for High-Performance Needs: Our services include impedance control, back drilling, and heavy copper (up to 40 oz) for performance.
Materials: FR4, High-Speed, High-Frequency, Metal Core, Ceramic, PTFE to Match Your Specific Project Requirements: We use materials like FR4, high-speed, metal core, ceramic, and PTFE to suit project needs.
Blind & Buried Vias, Micro Vias, and Any-Layer HDI for High-Density Interconnect Solutions: We offer blind/buried vias, micro vias, and any-layer HDI for compact, high-density designs.
VIPPO, Conductive & Non-Conductive Via Plugging for Enhanced Reliability: Our VIPPO, conductive, and non-conductive via plugging solutions enhance PCB reliability and durability.
Backplane Design, Embedded Devices, and IC Substrate Manufacturing for Advanced Electronic Systems: We specialize in backplane design, embedded devices, and IC substrates for advanced electronic systems.
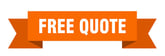
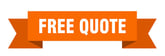
What is PCB Manufacturing?
PCB stands for Printed Circuit Board, the essential component found in nearly every electronic device. Typically green, white, or black in color, PCBs serve as the foundation for connecting various electronic components. They use copper traces to electrically link components, enabling devices to function properly.
In a narrow sense, PCB manufacturing refers to the process of producing printed circuit boards. However, PCB manufacturing is a complex field that encompasses a wide range of knowledge, including the history of PCBs, PCB terminologies, base laminates, manufacturing processes, acceptance standards, PCB classifications, and cost factors involved in PCB production. The PCB industry also includes insights into current trends and future developments.
At Omini, we specialize in PCB manufacturing and bring over 16 years of experience in producing high-quality PCBs for a range of industries. We focus on small to medium-volume PCB production and ensure that every project meets the highest standards. Our factory is UL Listed (E358677), ISO 9001, and ISO 13485 certified, guaranteeing quality and reliability.
Whether you need simple single-layer PCBs or complex multi-layer HDI boards, Omini provides precise and cost-effective solutions to meet your specific requirements.
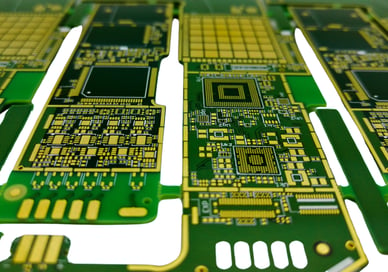
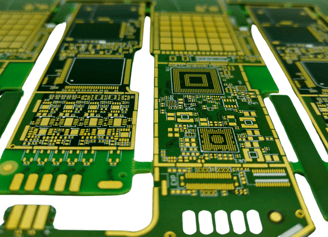
Our PCB Manufacturing Capabilities
At Omini, we provide a wide range of PCB manufacturing services, tailored to meet the complex demands of various industries. Our advanced capabilities include:
• Rigid PCBs: High-quality, durable boards for a wide range of applications
• Flexible PCBs: Lightweight and flexible solutions for compact and complex designs
• Rigid-Flexible PCBs: Combining the advantages of both rigid and flexible technologies for advanced applications
• Blind & Buried Vias: Efficient interconnections for multi-layer boards
• Staggered & Stacked Vias: Optimized for high-density interconnect (HDI) applications
• Via-in-Pad (VIPPO): Advanced via technologies for improved signal integrity and board space optimization
• Via Plugging: Using materials such as S/M, epoxy, or copper to enhance board reliability
• i+N+i Structure HDI: Any-layer HDI technology for compact, high-performance circuits
• FR4, Polyimide, Ceramic, Alumina, and PTFE for diverse thermal, electrical, and mechanical needs
• Aluminum Base PCBs: Excellent thermal conductivity for power electronics and LED applications
• Copper Base PCBs: Enhanced heat dissipation for high-power applications
• RF & Microwave PCBs: Precision-engineered for high-frequency, low-loss applications
• High-Frequency and High-Speed PCBs: For applications requiring superior signal integrity and minimal delay
• Impedance Control PCBs: Essential for high-speed data transmission and signal integrity
• Extreme Copper (up to 20 oz): For high-power applications requiring thick copper layers
• PCBs with IC Substrate: Specialized designs for integrated circuit applications
• Backplane PCBs: High-density interconnect solutions for complex systems
• Back Drilling: Enhanced signal integrity for high-speed designs
PCB Material Types
At Omini, we offer a wide variety of materials for PCB manufacturing to meet the specific needs of different industries and applications.
1. FR4 Materials
• High TG FR4 – Designed for high-temperature environments, ensuring durability and reliability
• Halogen-Free FR4 – Environmentally friendly option with no halogens, ideal for eco-conscious projects
• High-Speed FR4 – Engineered for high-speed signal transmission, minimizing signal loss
• Reinforced FR4 – Offers enhanced mechanical strength and resistance to thermal stress
2. Flexible Materials
• PI (Polyimide) – Known for its excellent thermal stability and flexibility, suitable for flexible circuits
• PET – Lightweight and durable material used in flexible and semi-flexible PCBs
• Semi-Flex Material – Provides a balance between flexibility and rigidity for unique design requirements
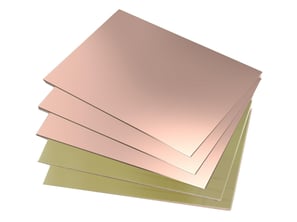
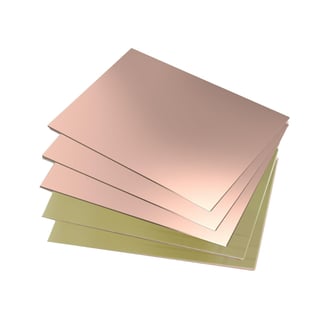
3. Metal-Based Materials
• Aluminum – Excellent thermal conductivity, ideal for high-power and LED applications
• Copper – High thermal and electrical conductivity, used for high-performance PCBs
• Alumina Ceramic – Used for applications requiring high dielectric strength and heat resistance
• Special Alloys – Tailored materials for specific applications that require unique properties
4. Microwave & RF Materials
• RO4350B, RO4003C, RO3003 – High-frequency laminates for superior electrical performance in microwave and RF applications
• Arlon 85N, 33N – Excellent for high-frequency and high-speed circuits with minimal signal loss
• MEGTRON 6 (R-5775) – Designed for ultra-low-loss applications in high-speed digital circuits
• TU-872 LK, Isola Tachyon 100G, ITEQ IT-968TC – High-performance materials used in advanced microwave and RF applications
Other PCB Manufacturing Capabilities
Omini offers a wide range of advanced PCB manufacturing capabilities, designed to meet the specific needs of your electronic projects. From high-layer count designs to custom surface finishes, we ensure high-quality, reliable PCBs for diverse applications.
1. Layer Counts: We provide PCBs with 1-40 layers for mass production and up to 100 layers for prototype development, ensuring flexibility for various project complexities.
2. Board Thickness: Omini manufactures PCBs with board thickness ranging from 0.1mm to 15mm, accommodating both standard and specialized requirements.
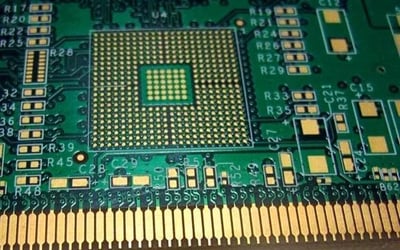
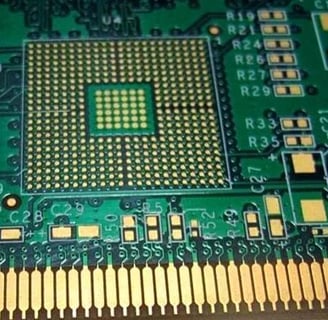
3. Max. Board Dimensions: Our PCBs can be produced in large dimensions, up to 20 x 59 inches, ideal for high-performance applications and large-scale designs.
4. Max Aspect Ratio: We support a maximum aspect ratio of 16:1, providing flexibility in PCB design for compact and complex layouts.
5. Solder Mask Color: We offer a variety of solder mask colors, including green, black, blue, red, and white, with custom colors available upon request.
6. Silkscreen Color: Choose from standard silkscreen colors such as white, black, and yellow, or opt for custom colors based on your specific design needs.
7. Outline Methods: We use precision CNC routing, V-cut, and punching methods to outline your PCBs, ensuring accurate, clean cuts and smooth edges.
8. Surface Finish: Omini provides a range of surface finishes, including HAL, ENIG, immersion tin/silver, ENEPIG, gold finger, gold plating, and selective hybrid, ensuring durability and performance.
By choosing Omini as your PCB manufacturer, you gain access to cutting-edge capabilities that support your project’s specific requirements, whether it’s for prototype or large-scale production.
The History of PCB Manufacturing
The history of PCB manufacturing is marked by continuous innovations that have transformed electronics. From early wire connections to today’s complex, multi-layer PCBs, Omini continues to lead the industry with advanced manufacturing capabilities.
1. 1925: The Beginning of PCB Manufacturing: Charles Ducas in the US created printed wire on an insulating substrate, replacing traditional wire connections. This laid the foundation for modern PCB manufacturing.
2. 1936: The Creation of Printed Circuit Boards: Austrian inventor Paul Eisler developed the first printed circuit boards and used them in radio devices, marking a significant advancement in electronics design and production.
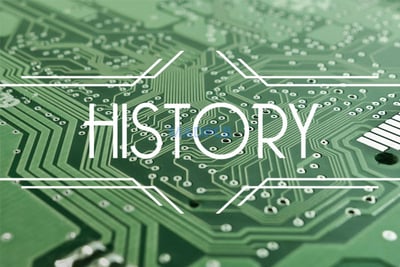
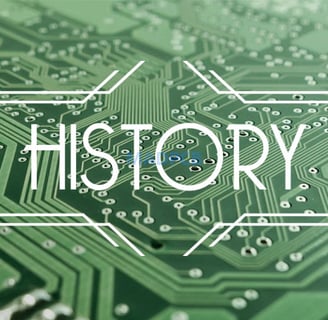
3. 1947: Use of Epoxy Resin in PCB Manufacturing: Epoxy resin was introduced as a substrate material in PCB manufacturing, improving durability and making PCBs more reliable for various applications.
4. 1948: Official Recognition of PCB Technology: The United States officially recognized the printed circuit board as an invention and began using it for commercial purposes, driving further innovation in the field.
5. 1953: Development of Double-Sided Boards by Motorola: Motorola developed double-sided PCBs using electroplated through-hole technology, paving the way for the development of multilayer printed circuit boards (PCBs).
6. 1960: Invention of Flexible PCBs: V. Dahlgren invented the flexible printed circuit board by adhering copper foil onto flexible plastic material, expanding PCB design possibilities for more compact and versatile applications.
7. 1961: Introduction of Multilayer PCB Manufacturing: Hazeline in the USA began manufacturing multilayer PCBs using plating through-hole methods, enabling complex, multi-functional designs that integrate multiple layers of circuitry.
8. 1995: Panasonic’s Any-Layer Drill Technology: Panasonic developed the any-layer drill for multilayer DHI PCBs, introducing stacked vias to meet any-layer connection requirements, enhancing design flexibility.
9. 1996: Toshiba’s B2IT Multilayer PCB: Toshiba introduced the B2IT multilayer PCB, which quickly became widely adopted in the PCB manufacturing industry for its efficiency and reliability.
10. 2000: Advancements in Rigid-Flex and IC Substrate Technologies: New technologies, including rigid-flex boards, buried resistance and capacitance, and IC substrates, revolutionized PCB manufacturing, enabling more sophisticated and high-performance electronic systems.
At Omini, we leverage these technological advancements and the rich history of PCB manufacturing to provide state-of-the-art PCB solutions for today’s most demanding electronic applications.
Classifications of PCB Manufacturing
With nearly 100 years of development, PCBs have become an integral part of nearly every electronic device. Today, they come in various types, each suited for different applications. Here are the most commonly recognized classifications of PCBs in the industry:
By Material
• FR4 PCB
• Rogers PCB
• Ceramic PCB
• Polyimide PCB
• Semiflex PCB
• Isola PCB
• Teflon PCB
• Alumina PCB
• High Tg PCB
• Halogen-Free PCB
• Copper-Based PCB
• Taconic PCB
• Low Loss PCB
By Feature
• Heavy Copper PCB
• Blind and Buried Vias
• Microvia PCB
• VIPPO PCB
• High-Frequency PCB
• High-Speed PCB
• Quick Turn PCB
• Single-Sided PCB
• Double-Sided PCB
• 4 Layer PCB
• 6 Layer PCB
• IC Substrate PCB
• Embedded PCB
By Application
• Energy Meter PCB
• LED PCB
• Inverter PCB
• Control PCB
• Sensor PCB
• Amplifier PCB
• Radar PCB
• Medical PCB
• Automotive PCB
• Capacitive PCB
• HVAC Circuit Board
• UPS Circuit Board
• Industrial PCB
PCB Manufacturing Process at Omini
PCB manufacturing is a complex, multi-step process that requires precision and expertise. At Omini, we offer comprehensive PCB solutions, specializing in both single/double-layer and multilayer PCBs. Below is a brief overview of the key steps involved in the production of single/double-layer and multilayer PCBs, ensuring high-quality standards at every stage.
Single / Double-Layer PCB Manufacturing Process
Material Sheet Cutting: Precision cutting of base materials to the required dimensions.
Drilling: High-precision drilling of holes for component placement and vias.
PTH & Copper Plating: Plating through holes (PTH) and copper layers to form the circuit.
Dry Film and Exposure: Applying and exposing the photoresist film to define the copper pattern.
Copper Etching: Etching to remove excess copper and form the desired circuit traces.
Copper Trace AOI (Automated Optical Inspection): Inspecting copper traces for accuracy and defects.
Quality Inspection
Rigorous inspection to ensure the integrity and functionality of the PCB.
Solder Mask Printing
Applying the solder mask to prevent soldering errors and protect the PCB.
Component Mark Printing
Marking locations for components on the PCB.
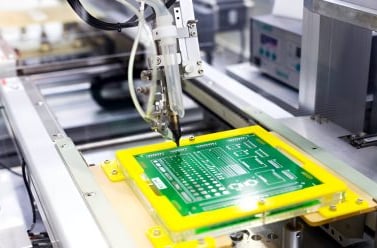
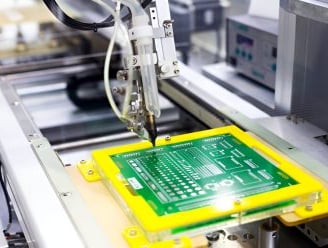
Multilayer PCB Manufacturing Process
Inner Layer Board Cutting: Precision cutting of the inner layers to the specified size.
Inner Layer Dry Film and Exposure: Applying and exposing the photoresist film for the inner layer copper traces.
Inner Layer Etching: Etching the inner layers to create the copper circuit traces.
Inner Layer AOI (Automated Optical Inspection): Ensuring the quality of the inner layer circuitry with optical inspection.
Black Oxide Treatment: Adding a protective black oxide layer to the inner layers.
Layup and Lamination: Aligning and bonding the inner layers with prepreg material through heat and pressure.
Board Cutting: Cutting the laminated multilayer PCB to the desired shape.
Drilling: Drilling additional holes for vias and component placement.
PTH and Copper Plating: Electroplating the drilled holes and applying copper layers.
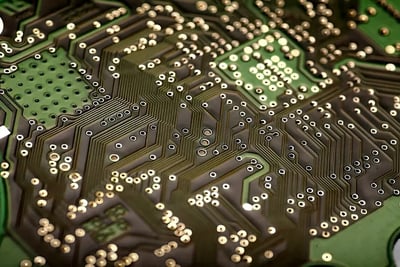
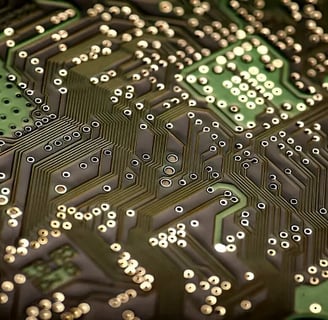
Surface Treatment: Applying a surface finish to enhance solderability and improve PCB durability.
Outline Profiling: Cutting the PCB to its final shape using CNC routing or punching.
E-testing: Electrical testing to ensure all electrical connections are intact and functional.
Final Quality Checking: Comprehensive inspection to ensure all specifications are met.
Packaging: Safe packaging for shipping to clients, ensuring product integrity.
Dry Film and Exposure: Applying and exposing the outer layer photoresist for circuit patterning.
Copper Etching: Etching the outer layers to form the final circuit traces.
Outer Layer AOI: Optical inspection of the outer layer circuits for defects.
Solder Mask Printing: Applying solder mask to protect the PCB and define solder pads.
Component Mark Printing: Printing component designators and symbols on the PCB.
Surface Treatment: Applying surface finishes like ENIG or HASL for enhanced solderability.
Outline Profiling: Cutting the PCB into its final dimensions using CNC or punching techniques.
E-testing: Conducting electrical tests to verify the functionality of the multilayer PCB.
Final Quality Checking: Ensuring that the multilayer PCB meets all specifications and quality standards.
Packaging: Secure packaging for transportation and delivery.
PCB Manufacturing Standards at Omini
In the PCB manufacturing industry, adhering to internationally recognized standards is essential for ensuring high-quality, reliable products. At Omini, we strictly follow the most widely accepted PCB manufacturing standards, particularly those set by IPC (Institute of Printed Circuits). IPC is the leading global association dedicated to advancing the research, development, and implementation of standards for the manufacturing of printed circuit boards (PCBs), wire harnesses, and electronic assemblies.

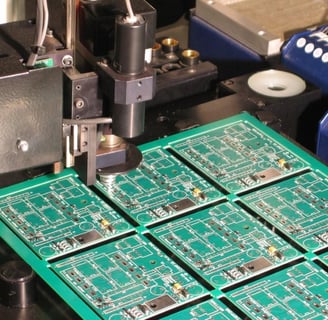
PCB Manufacturing Standards Comparison: IPC-A-600 and IPC-6012
In the world of PCB manufacturing, we often encounter the terms IPC Class 2 and IPC Class 3. These classifications are part of two of the most recognized standards in the industry: IPC-A-600 and IPC-6012, both crucial for quality control and production processes in printed circuit board manufacturing.
IPC-A-600 is the standard for the acceptability of printed boards, categorizing them into IPC Class 1, Class 2, or Class 3. This standard serves as a guide for inspecting PCBs and identifying unacceptable defects, ensuring that manufacturers and customers are aligned on quality expectations. It includes detailed visual representations highlighting the differences between Class 1, Class 2, and Class 3 boards.
On the other hand, IPC-6012 defines the performance specifications for PCB manufacturing, offering guidelines for manufacturers to adhere to IPC Class 1, Class 2, Class 3, or Class 3/A standards. While IPC-A-600 focuses on the inspection of finished boards, IPC-6012 is more concerned with the manufacturing process itself, ensuring that production meets the required standards.
Although IPC-A-600 and IPC-6012 serve different purposes, they share the same definition for Class 1, Class 2, and Class 3, so understanding the distinctions between them is not a concern for manufacturers and suppliers. Both standards are integral to ensuring the quality and reliability of PCBs across various applications.
The Main Factors Affecting PCB Manufacturing Costs
Printed Circuit Boards (PCBs) are custom-designed products, and the manufacturing costs can vary significantly depending on various factors. At Omini, we understand the importance of cost efficiency without compromising on quality. Below, we outline the main factors that influence the cost of PCB manufacturing.
Base Material Types
The type of material used for PCB production is one of the most significant cost drivers. Different PCB materials come with varying price levels, and even different manufacturers of the same material can offer different pricing. For example, FR4, the most commonly used PCB material, may cost around $30 USD per square meter. In contrast, high-frequency materials can be up to 10 times more expensive than FR4. Polyimide, commonly used in flexible PCBs, typically costs around $50 USD per square meter, but materials from premium manufacturers like Dupont can be 2-5 times more expensive. To ensure accurate pricing and avoid unexpected costs, it’s crucial to specify the material type clearly in the Gerber files and specifications when ordering from a PCB manufacturing supplier like Omini.
PCB Dimensions
Larger PCBs require more material, which directly increases manufacturing costs. At Omini, our engineers work with you to optimize your PCB panel layout, ensuring the best material utilization to help reduce costs without compromising quality.
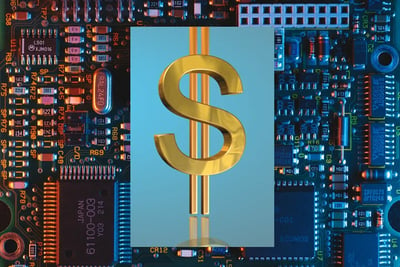
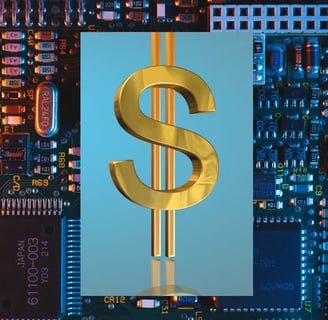
PCB Layer Counts
The number of layers in a PCB significantly impacts its cost. More layers require additional materials and processing steps, leading to a higher price. To minimize costs, we recommend using the lowest possible layer count that meets your design requirements.
Copper Thickness
Thicker copper layers increase the cost of PCB manufacturing. The standard copper thickness is usually 0.5-1 oz per square foot, but anything above 1 oz will result in higher costs. For 3 oz copper (105 µm), the cost can increase considerably. For accurate pricing, it’s essential to consult with a PCB manufacturing supplier like Omini to understand the best options for your needs.
PCB Thickness
The overall thickness of a PCB directly affects its cost. Standard PCB thickness is 1.6 mm, and anything thicker will increase the price. However, ultra-thin PCBs, such as 0.15 mm FR4, are even more expensive due to the complexity of manufacturing. To keep costs low, it’s often advisable to use standard thicknesses ranging from 0.8 to 2.0 mm.
Layup Structure
In multilayer PCB designs, using standard layup structures can help reduce costs. Custom layup structures, such as those requiring multiple prepregs or extra materials, can significantly increase manufacturing expenses. For example, using extra thick dielectrics or adding unclad FR4 material increases costs due to additional processing requirements.
Blind and Buried Vias
Using blind and buried vias increases the complexity of PCB manufacturing. These advanced features require more sophisticated equipment and additional processes, making HDI (High-Density Interconnect) PCBs more expensive than standard PCBs that only use PTH (Plated Through-Hole) vias.
Surface Finishes
Different surface finishes come with varying costs. The most affordable options include HAL (Hot Air Solder Leveling) and OSP (Organic Solderability Preservative). ENIG (Electroless Nickel Immersion Gold), along with finishes like immersion silver, immersion tin, and ENEPIG, are more expensive. Hard gold plating, which uses real gold and is applied in thicknesses ranging from 0.1-3 µm, is the most expensive finish due to the cost of the gold material.
Special Technology or Requirements
Special requirements such as countersink holes, back drilling, or impedance control can also influence the overall PCB manufacturing cost. To get an accurate estimate for these specialized features, we recommend sending your Gerber files to Omini for a detailed, free quote.
How to Choose a Reliable PCB Manufacturing Supplier?
Choosing a reliable PCB manufacturing supplier is critical to ensuring the success of your electronic products. PCBs are essential components in virtually all electronic devices, so selecting the right manufacturer is key to achieving high-quality, cost-effective solutions. With so many options available, how can you identify a reliable PCB manufacturer? Here are the most important characteristics of a trustworthy PCB supplier:
1. ISO9001 and UL Certifications
Certification standards like ISO9001 and UL are essential indicators of a reliable PCB manufacturer.
• ISO9001 is a globally recognized quality management standard that ensures a manufacturer follows best practices in areas such as staff training, equipment management, material control, supplier audits, and quality control. A manufacturer certified with ISO9001 demonstrates a commitment to maintaining a high-quality production environment.
• ISO14001 is an international standard for Environmental Management Systems (EMS). It helps organizations improve environmental performance, comply with regulations, reduce environmental impact, and promote sustainability through continuous improvement and effective resource management.
• UL (Underwriter Laboratories) certification indicates that the manufacturer complies with international safety standards. It is a must-have for many PCB types, especially in industries that require strict safety measures, such as automotive and medical devices.
At Omini, we are proud to be ISO9001:2015, ISO14001 certified and UL listed, ensuring our customers receive the highest quality and safety standards in PCB manufacturing.
2. A Good Fit for Your Business Needs
A reliable PCB supplier must be a good match for your business in terms of scale and industry focus. It’s crucial to find a supplier that understands your unique requirements and can provide competitive pricing and excellent service for your PCB needs.
At Omini, we specialize in offering one-stop PCB manufacturing services for small to medium-sized orders. Whether you need a single prototype or a batch of several thousand units, we cater to a wide range of industries including automotive, power control, medical devices, telecommunications, testing, and more. We are committed to being the right partner for businesses that need flexibility and reliability in PCB production.
3. Commitment to Quality and Longevity
Quality is the backbone of any reliable PCB manufacturer. A supplier with over a decade of experience demonstrates the stability and expertise necessary to meet your production requirements.
At Omini, we have been serving customers with high-quality PCBs since 2007. Over the past 16 years, we’ve earned the trust of clients who rely on us for small to medium-sized PCB orders. Our goal is simple: to deliver high-quality PCBs at competitive prices to customers worldwide.
“Quality Comes First” is not just a slogan at Omini; it’s a core value embedded in everything we do. From prototype to mass production, we ensure that every PCB meets the highest standards of performance and reliability.
4. Flexibility and Exceptional Customer Service
Outstanding customer service is essential for a smooth partnership. A good PCB supplier should be able to meet your needs with flexibility, quick response times, and effective solutions.
At Omini, our customer service team is dedicated to helping you every step of the way. From quick responses to RFQs and order inquiries to custom shipping arrangements and partial shipments, we strive to make your experience as seamless as possible. We also provide free DFM (Design for Manufacturing) reviews before placing orders to ensure the most efficient production process.
If you ever encounter issues or have concerns, our team, including our general manager, is committed to resolving any problems swiftly to ensure complete satisfaction. We are fully flexible and focused on delivering the best service, no matter what your PCB requirements may be.
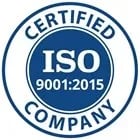

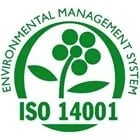

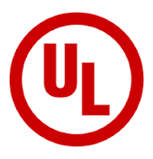

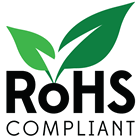
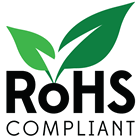
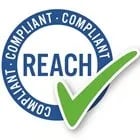

The Current Landscape of PCB Manufacturing
Over the past century, PCB manufacturing has seen remarkable technological advancements. In this section, we explore the current state of PCB manufacturing, including key regions driving production, the leading PCB manufacturers globally and in China, and the primary applications of PCBs.
Leading Countries/Regions in PCB Manufacturing
Between 2015 and 2021, the majority of the world’s top 100 PCB suppliers were based in Asia, with countries like China (Mainland and Taiwan), Japan, and South Korea leading the industry. Together, these regions accounted for approximately 93% of the global PCB market revenue.
In 2021, the market breakdown was as follows: Taiwan: 35%, Mainland China: 28%, Japan: 18%, and South Korea: 12%. The remaining 7% came from other global manufacturers, with China’s PCB industry continuing to grow steadily.
Key Applications of PCB Manufacturing
PCBs are integral to nearly all electronic products. The primary applications include:
• Communication Industry
• Computing & Data Storage
• Industrial Automation
• Medical Devices
• Automotive Electronics
• Consumer Electronics
As new technologies evolve, the demand for PCBs in emerging fields like 5G, IoT (Internet of Things), cloud computing, and robotics is expected to surge.
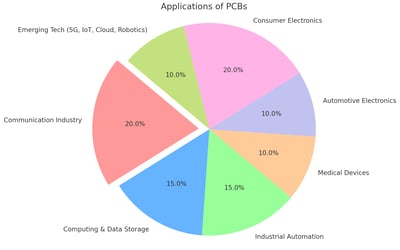
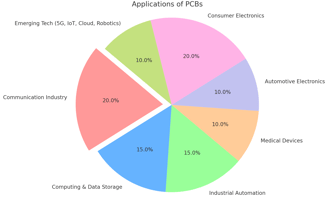
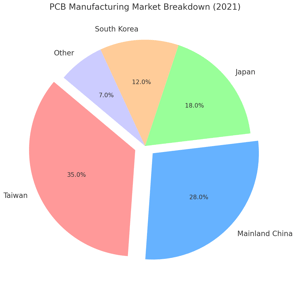
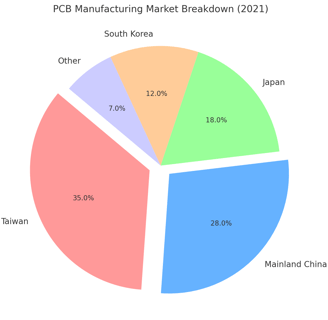
The Future of PCB Manufacturing
PCBs play a critical role in electronic devices, facilitating the integration of electronic components for various functions. With the expansion of technologies such as 5G, AI (Artificial Intelligence), wearable tech, big data, new energy vehicles, and Industry 4.0, the demand for PCB manufacturing will continue to grow significantly.In 2021, the global PCB industry experienced a 20% growth, reaching an $80 billion turnover. From 2022 to 2026, the market is expected to grow at least 5% annually, pushing the total value beyond $80 billion by 2026. China’s PCB manufacturing sector will also see significant growth, continuing to be a major player in the global market.
Additionally, as high-tech electronics advance, the demand for specialized PCBs like rigid-flex, HDI, and IC substrate PCBs will increase, requiring manufacturers to invest heavily in advanced equipment and technology.
China’s established supply chain and diverse customer base both domestically and internationally will ensure its position as the leading global PCB manufacturing hub in the coming years. China’s growth in this sector is expected to outpace the global average, contributing significantly to the global electronics industry’s development.
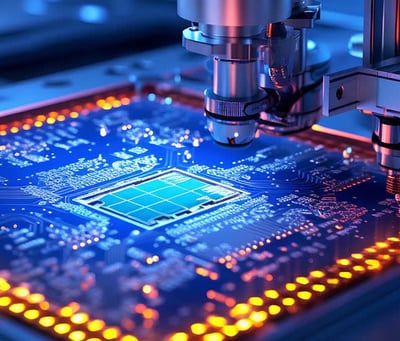
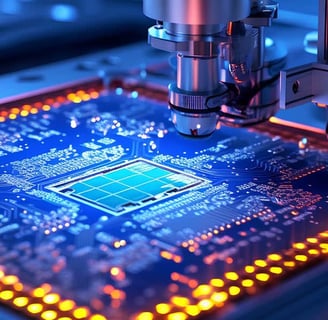
Why Choose Omini for PCB Services?
1. Premium Quality PCB Manufacturing
As a leading PCB manufacturer in China, Omini understands that product quality is the foundation of customer trust. We maintain rigorous quality control throughout every stage of production—ensuring that every board meets the highest standards. Our comprehensive quality management system covers raw material sourcing, in-process inspections, and final product testing. With a team of experienced engineers and technicians, we guarantee exceptional quality. Omini is also certified with ISO 9001, ISO 13485, and UL approvals, further ensuring our commitment to superior quality.
2. Over 16 Years of PCB Expertise
With more than 16 years in the PCB manufacturing industry, Omini has the expertise and experience to deliver reliable and innovative solutions. Our extensive experience helps us effectively handle a wide range of challenges, ensuring we meet our clients’ specific requirements. Additionally, our advanced production and testing equipment ensures the highest quality standards. Partnering with Omini means choosing a proven leader in the PCB industry.

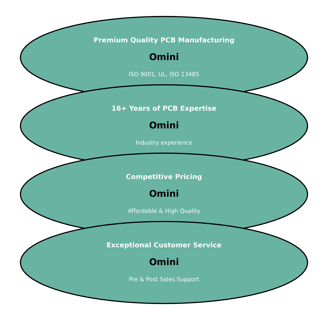
Founded in 2007, Omini is a trusted leader in PCB manufacturing, offering comprehensive, high-quality PCB solutions in China. Specializing in small to medium-volume production, Omini is committed to being your long-term strategic partner. We provide flexible, customer-focused services, which has earned us the trust of over 1,000 clients worldwide. Our goal is to become an efficient and influential PCB supplier, delivering the highest quality printed circuit boards at competitive prices.
3. Competitive Pricing for High-Quality PCBs
Leveraging our mature supply chain in China’s electronics hub, Omini provides cost-effective PCB solutions without compromising on quality. Our decades of industry experience, along with cutting-edge manufacturing technologies, allow us to offer competitive pricing for both small and medium-volume production. When it comes to affordable and high-quality PCB boards, Omini stands out as one of the top PCB manufacturers in China.
4. Exceptional & Flexible Customer Service
At Omini, we prioritize providing excellent customer service, both before and after the sale. Our pre-sales team offers detailed consultations to address any inquiries and ensure the best solution for your needs. Post-sales, we remain committed to supporting our clients, offering comprehensive assistance to resolve any issues until you’re fully satisfied. Thanks to our exceptional service and quality products, Omini has earned the trust and positive feedback from customers worldwide.
Contacts
Email: sales@ominipcba.com
Mobile: +86-185-7640-5228
Copyright © 2007-2025. Omini Electronics Limited. All rights reserved.
Head Office: +86-755-2357-1819
Products & Services
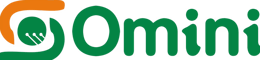
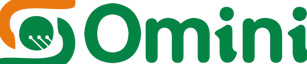
Office Address: No. 605, Tongxin Technology Building, Bao’an Avenue, Bao’an District, Shenzhen, Guangdong, China.
SMT Plant: A Building, Longwangmiao Industrial Park, Baishixia Community, Fuyong Street, Bao'an District, Shenzhen, China.
Omini Electronics Limited is an expert in trusted PCB Fabricaton and PCB Assembly in China since 2007. We have served over 1000 global customers with high-quality, low to medium-volume production. Certified by UL (E532498), ISO9001:2015, and ISO13485:2016, we offer expert electronics manufacturing services, including PCB manufacturing, assembly, and contract manufacturing, ensuring top-tier quality and precision in every project.