Phone: +86-755-2357-1819 Mobile: +86-185-7640-5228 Email: sales@ominipcba.com whatsapp: +8618576405228
Wire Bonding
Omini offers comprehensive wire bonding services for PCB and assembly, ensuring high-quality connections with precision. Explore our full range of solutions, including fabrication, testing, and electromechanical assembly, tailored for your needs.
Gold Wire Bonding & Aluminum Wire Bonding: Precision bonding solutions for reliable connections.
PCB Fabrication, Parts Sourcing & PCB Assembly: Complete services from design to assembly.
Box Build Assembly & Electromechanical Assembly: Comprehensive assembly solutions for complex products.
Small to Medium Volume Production: Flexible production capabilities to suit your needs.
ISO9001:2015, ISO 13485:2016 Certified & UL Listed: Certified to meet industry standards for quality.
100% E-test, AOI, X-RAY, ICT & FCT: Rigorous testing ensures high-quality, functional products.
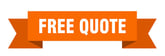
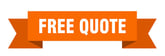
What is Wire Bonding?
Omini specializes in wire bonding, a critical process for ensuring reliable interconnection between chips and PCBs. Our advanced solutions enhance PCB assembly with precise bonding using materials like gold, aluminum, and copper.
Key Features of Wire Bonding:
1. Precise Interconnections: Wire bonding ensures the chip is securely connected to the PCB or substrate using high-quality metallic wires like gold, aluminum, or copper.
2. High-Quality Bonding Materials: The choice of bonding material depends on the application, cost, reliability, and compatibility, ensuring optimal performance in your electronics.
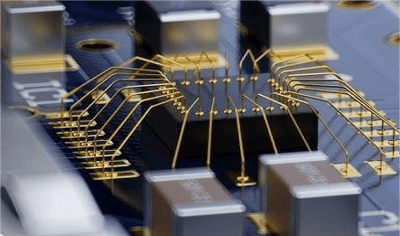
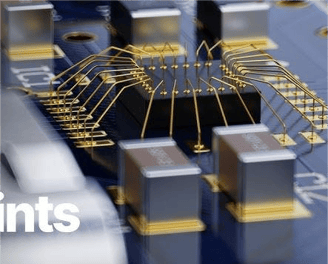
3. Automated Wire Bonding Machines: Our state-of-the-art machines are equipped with Pattern Recognition Systems (PRS) for accurate placement of bonding pads and precise wire bonding.
4. Secure Clamping & Stability: To maintain planarity and stability during the bonding process, the PCB and chip are secured in place through a vacuum system.
5. Capillary Tool Use: A capillary holds and guides the wire, ensuring a consistent and reliable bond is formed between the chip and PCB.
Omini offers top-tier wire bonding services to guarantee the highest quality in your PCB assembly projects.
Wire Bonding Types in PCB Assembly: Insights from Omini
Omini, a leader in PCB assembly and testing, offers various wire bonding techniques, each with unique benefits for different applications. Here’s an overview of the most common types of wire bonding used in PCB assembly, ensuring high-quality, efficient connections for your products.
1. Ultrasonic Bonding
Ultrasonic bonding is widely used in PCB assembly for its ability to bond wires at lower temperatures. This process utilizes ultrasonic frequency to generate mechanical vibrations that bond materials like aluminum. The process sequence includes the following steps:
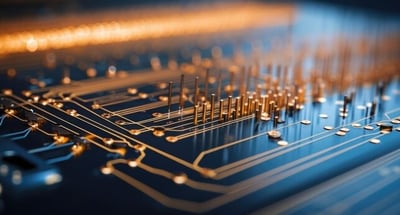
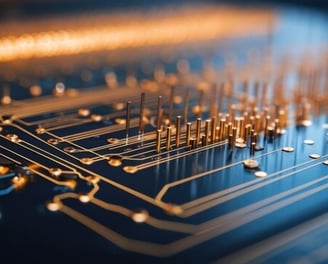
• Downward force is applied to land the wire on the bond pad.
• Ultrasonic scrub ensures a reliable wedge bond.
• A wire loop is formed, followed by opening the clamp.
• Downward force is applied again to land the wire, creating a second bond (stitch) on the PCB or substrate.
• The wire is cut at the heel of the wedge to complete the process.
2. Thermosonic Bonding
In thermosonic bonding, Omini applies ultrasonic energy combined with high temperatures to create strong, reliable bonds using materials like gold and copper. This method is particularly effective for bonding small, delicate components. The bonding process follows these simplified steps:
• The wire is held in place by the capillary tool.
• Ball formation occurs through an Electric Flame-Off (EFO) spark.
• The capillary with wire lands on the chip pad.
• Ultrasonic energy, heat, and pressure create the ball bond on the pad.
• A loop is formed as the capillary is lifted.
• The same energy combination forms the stitch bond on the PCB or substrate.
3. Thermocompression Bonding
Similar to thermosonic bonding, thermocompression bonding does not involve ultrasonic energy but relies on heat, pressure, and time to create the bond. The process uses a heated capillary or stage to apply heat to the wire, allowing it to bond with the substrate. Key steps include:
• Ball formation is achieved through an EFO spark.
• The ball is attached to the chip or substrate.
• Heat, pressure, and time are used to form the bond.
• A flatter ball dimension and higher force are applied compared to thermosonic bonding.
Each of these wire bonding techniques ensures precise, reliable connections crucial for the performance and longevity of PCB assemblies. With Omini’s extensive experience in PCB assembly and testing, we ensure that your projects meet the highest industry standards for quality and reliability.
Key Considerations in the Wire Bonding Process: A Guide by Omini
Omini, an expert in PCB assembly and testing, emphasizes the importance of several factors during the wire bonding process to ensure the highest quality and reliability for your PCB designs. Here are the critical elements to consider:
1. Wire Type and Size
Selecting the correct wire type and size is essential to achieving proper wire bonding in PCBs. The wire material, purity, and alloy composition directly affect bonding strength and reliability. For fine-pitched devices, smaller wire sizes are required to avoid issues like shorting or swaying with adjacent wires. Choosing an improper wire type or size can lead to significant reliability failures, impacting your final product quality.
2. Capillary Type
The capillary used in wire bonding plays a pivotal role in the success of the process. Key features like chamfer diameter and face angle determine the formation of the ball and wedge during bonding. Incorrect capillary geometry can result in major bonding issues such as bond smearing, oversized bonds, and broken welds or stitches. Ensuring the right capillary type helps achieve precise and reliable connections, essential for long-term performance.
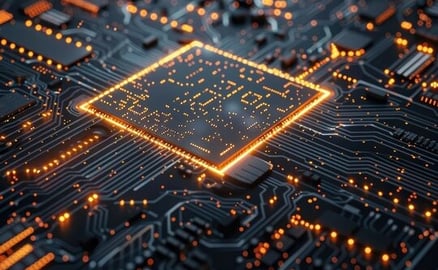
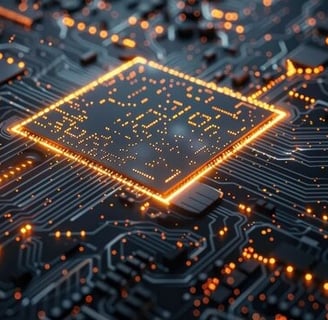
3. Clean Surfaces
For optimal wire bonding, surfaces must be free from contaminants that could interfere with the bonding process. Pre-bond surface cleaning, such as plasma cleaning, is often employed to prepare contact areas. Contaminated PCB areas can lead to poor bonding outcomes, including low wire pull and bond shear test results. In copper wire bonding, using forming gas or nitrogen is crucial to prevent oxidation, ensuring a clean and strong bond.
4. Wire Bond Machine Parameters
To achieve the best results, wire bond machine parameters—such as force, power, and time—must be carefully optimized. Excessive force or power can cause pad cratering or cracking, while insufficient settings can result in poor bonding and low pull test strength. Omini ensures that all machine parameters are precisely calibrated through design experiments, achieving the ideal settings for reliable and high-quality wire bonds in every PCB assembly.
By considering these key factors, Omini ensures the highest quality in wire bonding, contributing to durable, reliable PCB assemblies that meet industry standards.
Wire Bond Testing Methods: Ensuring Quality in PCB Assemblies with Omini
Omini, a leader in PCB assembly and testing, utilizes various wire bond testing methods to ensure the strength, reliability, and quality of every wire bond. Here’s an overview of the primary testing methods used to assess wire bond integrity during PCB assembly:
1. Wire Pull Test
The wire pull test is a widely used method to assess the strength and failure mode of wire bonds in PCB assemblies. This destructive test pulls the wire vertically using a hook to measure the pull strength and determine how the bond breaks. While the test is destructive, it is performed on a sample basis, typically during machine setup or lot monitoring, to ensure bond quality before large-scale production.
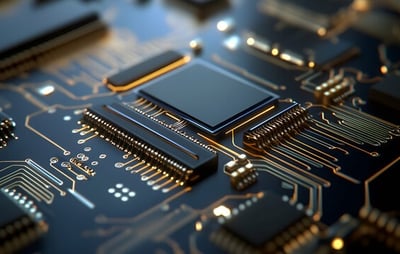
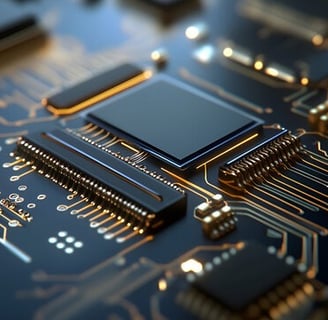
2. Ball Shear Test
The ball shear test is commonly applied for thermosonic and thermocompression bonding techniques. In this destructive test, a wedge tool is placed near the ball bond, and shear force is applied to break the bond. The strength of the bond varies significantly based on bonding parameters such as force, time, and temperature. This test is crucial for evaluating the bond strength in fine-pitched devices and ensuring the reliability of the bond under various conditions.
3. Cratering Test
The cratering test is designed to assess potential damage or cracking to the underlying pad caused by wire bonding. This test uses an etching technique to reveal cracks or damage, allowing engineers to analyze the impact of the bonding process. The specific chemical used in the test depends on the wire type. Cratering test results help verify bonding recipes and adjust parameters to prevent potential damage that could affect the long-term performance of the PCB assembly.
By utilizing these advanced testing methods, Omini ensures that every wire bond in your PCB assembly meets the highest industry standards for strength, reliability, and quality, providing a solid foundation for your electronic products.
Why Choose Omini as Your Strategic PCB Partner?
Omini, a leader in PCB assembly and testing, is committed to providing exceptional wire bonding services for your advanced PCB needs. With years of experience and a dedication to quality, Omini ensures every project is completed to the highest standards. Here’s why you should choose Omini as your trusted strategic partner in PCB assembly:
1. Commitment to Quality
At Omini, we prioritize quality in every wire bonding service. Our processes are designed to meet industry standards, with strict internal criteria implemented to ensure that each wire bond meets your exact specifications. This focus on quality ensures reliable and durable PCB assemblies, giving you peace of mind for long-term product performance.
2. Competitive Pricing
Omini offers cost-effective wire bonding services without compromising on quality. We work closely with our clients to find optimal solutions that meet your budget while maintaining high standards of service. Our flexible pricing model ensures that you receive the best value for your investment, making Omini an affordable choice for all your PCB needs.
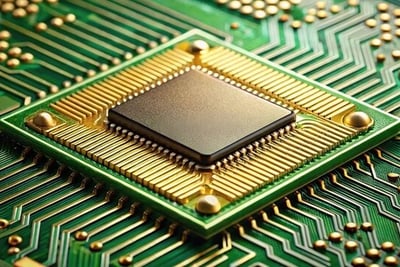
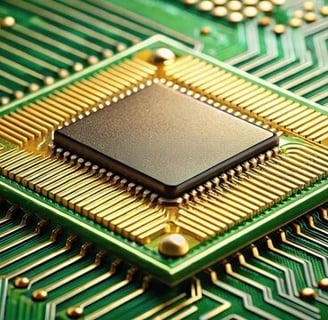
3. Engineering Expertise
With a proven track record of delivering high-yield, high-quality wire-bonded PCBs, Omini brings extensive engineering expertise to every project. Our team of experienced designers and engineers works closely with you to ensure the highest level of precision and reliability in every wire bond, optimizing the performance of your PCB assemblies.
4. Fast Delivery and Lead Time
Understanding the importance of timely delivery, Omini strives to meet even the tightest deadlines. We continuously track our delivery hit rates, machine utilization, and cycle times to ensure we can fulfill our commitments efficiently. With short lead times and reliable delivery, Omini helps you keep your projects on schedule, from start to finish.
Choose Omini for your wire bonding and PCB assembly needs and experience the perfect balance of quality, cost-efficiency, expertise, and timely delivery.
Contacts
Email: sales@ominipcba.com
Mobile: +86-185-7640-5228
Copyright © 2007-2025. Omini Electronics Limited. All rights reserved.
Head Office: +86-755-2357-1819
Products & Services
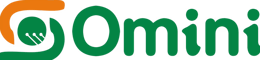
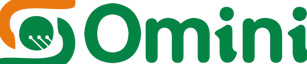
Office Address: No. 605, Tongxin Technology Building, Bao’an Avenue, Bao’an District, Shenzhen, Guangdong, China.
SMT Plant: A Building, Longwangmiao Industrial Park, Baishixia Community, Fuyong Street, Bao'an District, Shenzhen, China.
Omini Electronics Limited is an expert in trusted PCB Fabricaton and PCB Assembly in China since 2007. We have served over 1000 global customers with high-quality, low to medium-volume production. Certified by UL (E532498), ISO9001:2015, and ISO13485:2016, we offer expert electronics manufacturing services, including PCB manufacturing, assembly, and contract manufacturing, ensuring top-tier quality and precision in every project.