Phone: +86-755-2357-1819 Mobile: +86-185-7640-5228 Email: sales@ominipcba.com whatsapp: +8618576405228
Omini PCB Solutions – IPC Class 3 Compliance
For projects that require the highest level of precision and reliability, Omini offers IPC Class 3 certified PCBs, ensuring optimal performance in demanding industries like aerospace, medical, and military applications.
IPC Class 3 PCBs by Omini meet the highest industry standards, offering enhanced durability and reliability for mission-critical applications across various sectors.
Omini PCB Solutions cater to industries such as automotive, medical, military, and aeronautics, providing superior Class 3 PCBs tailored to each sector’s specific needs.
Class 3 IPC standards ensure exceptional reliability in harsh environments, such as aerospace, life support systems, and medical devices, where failure is not an option.
Omini offers IPC Class 3/A solutions for military and aeronautic applications, going beyond standard Class 3 requirements to ensure maximum performance and compliance with stringent regulations.
Choose Omini for your next high-performance PCB project, guaranteeing that each design meets the most rigorous industry standards for quality, durability, and performance.
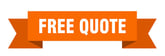
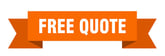
Omini PCB Solutions – IPC Class 3 Compliance
1. Copper plating thickness in PTH wall:
IPC Class 2 PCB: PTH wall thickness ≥ 20 µm.
IPC Class 3 PCB: PTH wall thickness ≥ 25 µm.
Omini ensures precise copper plating for Class 3 PCBs to meet critical standards.
2. Minimum ring of PTH:
IPC Class 2 PCB: Broken ring at ≤ 90°.
IPC Class 3 PCB: Minimum ring size 0.05 mm.
Omini produces Class 3 PCBs with optimal ring integrity for advanced applications.
3. Copper conductor width:
IPC Class 2 PCB: Gap not exceeding 30% of minimum wire spacing.
IPC Class 3 PCB: Gap not exceeding 20% of minimum wire spacing.
Omini guarantees precise conductor spacing for high-performance Class 3 PCBs.
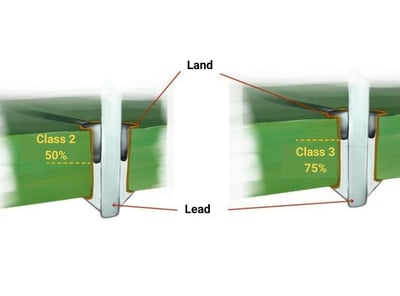
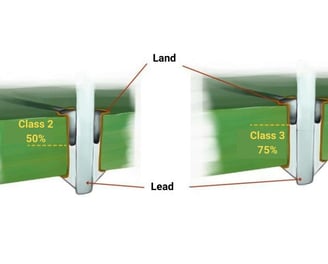
4. Hole wall copper plating voids:
IPC Class 2 PCB: Cavity inside hole wall acceptable under specific conditions.
IPC Class 3 PCB: No cavity allowed inside hole wall.
Omini ensures void-free copper plating in Class 3 PCBs for superior reliability.
5. Soda strawing in solder mask:
IPC Class 2 PCB: Straw gap acceptable under specific conditions.
IPC Class 3 PCB: No straw gap allowed.
Omini manufactures Class 3 PCBs with flawless solder mask application.
6. Maximum wicking allowed in copper plating:
IPC Class 2 PCB: Wicking not exceeding 100 µm.
IPC Class 3 PCB: Wicking not exceeding 80 µm.
Trust Omini for Class 3 PCB solutions with strict control over copper wicking.
Omini PCB Solutions – IPC-A-610 Class 3 PCB Assembly Acceptance Criteria
1. Hole wall filling by tin in PTH holes:
IPC Class 2 PCB assembly: Hole wall filling ≥ 50%.
IPC Class 3 PCB assembly: Hole wall filling ≥ 75%.
For Class 3 PCBs, Omini recommends PTH hole sizes over 15 mils to ensure proper solder paste filling and reliable connections.
2. Wetting on SMT components:
IPC Class 2 PCB assembly: Tin is evident on the vertical surface of SMD components.
IPC Class 3 PCB assembly: Minimum fillet height is 0.5 mm or 25% of solder + SMD component height.
Trust Omini for Class 3 assembly that ensures superior wetting for long-lasting component performance.
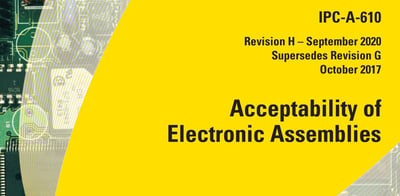
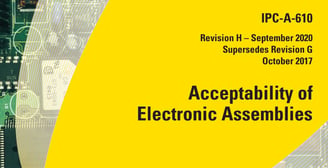
3. Side overhang on SMD components:
IPC Class 2 PCB assembly: Side overhang < 50% of component/pad area.
IPC Class 3 PCB assembly: Side overhang < 25% of component/pad area.
Omini ensures precise component placement with minimal overhang, optimizing Class 3 assembly quality.
4. End joint width on SMD pads:
IPC Class 2 standard: End joint width ≥ 50% of SMD component/pad.
IPC Class 3 standard: End joint width ≥ 75% of SMD component/pad.
Omini guarantees Class 3 assembly with enhanced joint widths for superior mechanical strength and electrical performance.
5. Side overhang on IC pins:
IPC Class 2 standard: Side overhang < 50% of pin width or ≥ 0.5 mm (whichever is less).
IPC Class 3 standard: Side overhang < 25% of pin width or ≥ 0.5 mm (whichever is less).
Omini ensures minimal overhang for Class 3 IC pin connections, enhancing overall reliability and performance.
Contacts
Email: sales@ominipcba.com
Mobile: +86-185-7640-5228
Copyright © 2007-2025. Omini Electronics Limited. All rights reserved.
Head Office: +86-755-2357-1819
Products & Services
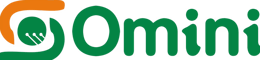
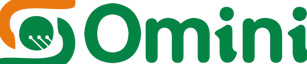
Office Address: No. 605, Tongxin Technology Building, Bao’an Avenue, Bao’an District, Shenzhen, Guangdong, China.
SMT Plant: A Building, Longwangmiao Industrial Park, Baishixia Community, Fuyong Street, Bao'an District, Shenzhen, China.
Omini Electronics Limited is an expert in trusted PCB Fabricaton and PCB Assembly in China since 2007. We have served over 1000 global customers with high-quality, low to medium-volume production. Certified by UL (E532498), ISO9001:2015, and ISO13485:2016, we offer expert electronics manufacturing services, including PCB manufacturing, assembly, and contract manufacturing, ensuring top-tier quality and precision in every project.