Phone: +86-755-2357-1819 Mobile: +86-185-7640-5228 Email: sales@ominipcba.com whatsapp: +8618576405228
PCB Surface Finishes
Omini offers a comprehensive range of PCB surface finishes, essential for ensuring high-quality, reliable performance in various electronic applications. With a focus on precision and customer satisfaction, Omini provides the following PCB surface finishing options
HASL (Hot Air Solder Leveling): A widely used, cost-effective surface treatment, providing excellent solderability for most PCB designs and applications, especially in standard consumer electronics.
ENIG (Electroless Nickel/Immersion Gold): This surface finish offers superior reliability with excellent solderability, ensuring high-quality connections for critical applications, particularly in high-frequency and high-performance PCBs.
OSP (Organic Solderability Preservative): An eco-friendly and cost-effective solution, ideal for lead-free applications, ensuring good solderability while providing a stable and long-lasting surface finish for your PCBs.
Immersion Silver: This finish provides excellent solderability and resistance to oxidation, making it an ideal choice for high-performance, fine-pitch components and long-term reliability in demanding environments.
Immersion Tin: A versatile surface finish, commonly used for fine-pitch components, ensuring reliable performance and enhanced durability, particularly in applications requiring superior flatness and solderability.
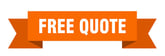
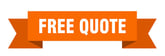
What are PCB Surface Finishes?
PCB surface finishes, also known as PCB surface treatments, refer to the technology used to apply a layer of metal or compound onto the copper pads of printed circuit boards (PCBs) through chemical or physical methods. These surface finishes serve two primary functions:
1. Prevents Oxidation of Copper Pads/Conductors: The surface finish protects the copper pads from oxidation, ensuring the long-term integrity and reliability of the PCB in various electronic applications.
2. Improves Solderability for Electronic Components: Surface finishes enable smooth and reliable soldering of electronic components onto the PCB, ensuring ease of assembly and superior performance in the final product.
Omini offers a variety of high-quality PCB surface finishes that cater to different needs, providing enhanced protection and improved solderability for your PCB designs.
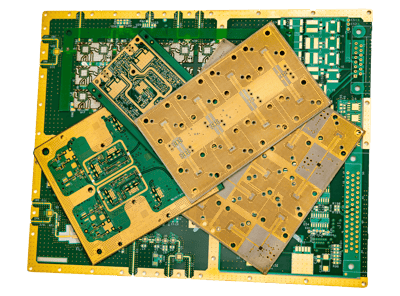
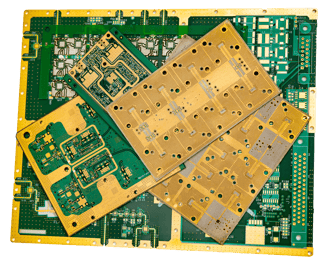
What Kinds of Surface Finishes Does Omini Offer?
At Omini, we provide a wide range of high-quality PCB surface finishes to meet diverse customer needs. Below are the surface finishes we specialize in:
1. Immersion Gold (Au): Ideal for high-frequency and high-reliability applications, offering excellent solderability and oxidation resistance.
2. Immersion Silver (Ag): A cost-effective option providing excellent solderability with minimal oxidation, perfect for a wide range of applications.
3. Immersion Tin: Commonly used for fine-pitch components, offering excellent flatness and solderability while ensuring long-lasting performance.
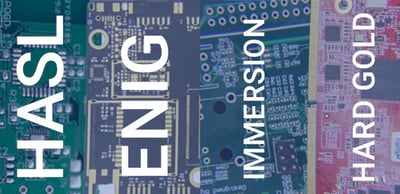
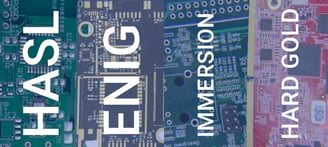
4. ENEPIG (Electroless Nickel/Immersion Gold with Palladium): A premium finish for advanced PCB designs, offering high reliability and superior solderability, particularly for high-density interconnects.
5. Pb-Free HASL (Hot Air Solder Leveling): A lead-free surface finish widely used for cost-effective, reliable, and environmentally friendly PCBs.
6. OSP (Organic Solderability Preservative): A cost-effective, eco-friendly finish ideal for lead-free applications, ensuring excellent solderability and protecting the PCB surface from oxidation.
7. Hard Gold Plating: Offers durable, wear-resistant finishes, perfect for applications that require gold plating for connectors, edge contacts, or high-precision applications.
8. Soft Gold Plating: Provides a smooth, reliable surface finish for applications that require high-performance soldering and a low-resistance surface.
9. Selective Finishes: Tailored surface finishes applied only to specific areas of the PCB, ideal for reducing costs while meeting performance requirements.
10. Carbon Ink / Peelable Blue Mask: Provides additional protection during the PCB manufacturing process and can be easily removed after assembly, ensuring clean and reliable circuit designs.
Choose Omini for expert PCB surface finishes that enhance performance, durability, and ease of manufacturing for your electronic applications.
Detailed Introduction of Different Kinds of PCB Surface Finishes by Omini
At Omini, we offer a wide range of PCB surface finishes to suit various applications, ensuring durability, reliability, and high performance. Below is a detailed breakdown of the different types of PCB surface finishes:
1. Immersion Gold (ENIG)
Immersion gold, also known as ENIG (Electroless Nickel Immersion Gold), involves covering the copper surface with a thick layer of nickel and gold. This process protects the PCB from oxidation in normal atmospheric conditions. With a shelf life of up to 12 months and excellent electrical performance due to gold’s excellent conductivity, immersion gold is widely used in high-density and high-standard PCBs, especially in advanced electronics.
2. Immersion Silver
Immersion silver involves a chemical displacement reaction to deposit a silver layer onto the copper pads. Silver provides excellent electrical conductivity, ensuring good performance, and is easy to solder with tin during the PCB assembly process. While the cost is lower than immersion gold, silver can yellow over time when exposed to environmental conditions, which can affect its appearance.
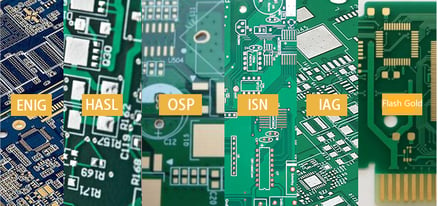
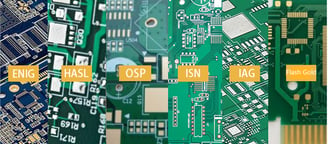
3. Immersion Tin
In the immersion tin process, a tin layer is deposited onto the copper pads through a chemical displacement reaction. The tin layer protects the copper from oxidation and provides excellent solderability. Immersion tin offers a smooth surface, which is ideal for fine-pitch components. Though it is more expensive than HAL (Hot Air Leveling), it ensures superior soldering performance.
4. ENEPIG (Electroless Nickel Electroless Palladium Immersion Gold)
ENEPIG is an enhanced version of ENIG. It involves the addition of a palladium layer between the nickel and gold layers, preventing the migration of nickel into the gold layer, which can cause defects. This process ensures better wiring performance, improved aging resistance, and eliminates the risk of black pad defects found in traditional ENIG finishes.
5. HAL (Hot Air Leveling)
HAL, or Hot Air Leveling, involves melting tin and leveling it over the PCB surface using hot air. This process creates a thick layer of solder that protects the copper pads, which are not covered by a solder mask. HAL is one of the most commonly used surface finishes due to its excellent performance and cost-effectiveness.
6. OSP (Organic Solderability Preservative)
OSP is a thin organic layer applied to the copper traces using a chemical method. This finish protects the copper from oxidation in normal environments and provides excellent solderability. During the soldering process, the organic film vaporizes at high temperatures, leaving a clean surface ideal for assembly.
7. Hard Gold Plating
In hard gold plating, a layer of nickel is first plated on the copper traces, followed by a 2-5 micron gold layer. The nickel prevents diffusion between gold and copper, while the gold plating protects against oxidation and ensures good solderability. Hard gold plating, containing cobalt and other elements, is used for non-welded areas such as edge connectors, offering a durable, wear-resistant surface.
8. Soft Gold Plating
Soft gold plating also involves a nickel layer followed by a 5-30 micron gold layer. Unlike hard gold, soft gold uses pure gold (no additives), resulting in a less shiny surface. Soft gold plating is ideal for soldering electronic components to the PCB and is commonly used for components requiring high solderability and precision.
9. Selective Finishes
Selective finishes involve applying two or more surface treatment methods on the same PCB to optimize performance. Common combinations include ENIG + OSP, ENIG + hard gold plating for edge connectors, HAL + hard gold plating, and OSP + hard gold plating. This approach maximizes the benefits of different finishes based on specific design requirements.
Choose Omini for reliable, high-quality PCB surface finishes that ensure enhanced performance, durability, and ease of assembly for your electronic products.
The Advantages and Disadvantages of Different Kinds of PCB Surface Finishes by Omini
At Omini, we provide a range of PCB surface finishes tailored to meet different performance and cost needs. Below is a comparison of the advantages and disadvantages of each surface finish:
1. HAL with Lead
• Cost: Normal
• Shelf Life: 12 months
• Solderability: High
• Advantages: Cost-effective and efficient in production with excellent solderability.
• Disadvantages: Not RoHS/Reach compliant. Not suitable for fine-pitch soldering (<0.5mm pin distance) or BGA due to rough surface.
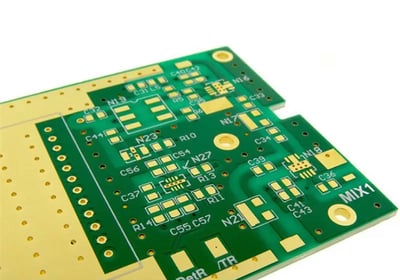
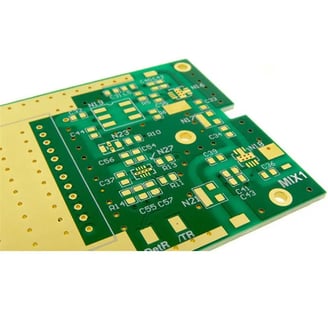
2. Pb-Free HAL
• Cost: Normal
• Shelf Life: 12 months
• Solderability: High
• Advantages: Cost-effective and highly efficient with excellent solderability.
• Disadvantages: Not suitable for fine-pitch components (<0.5mm pin distance) or BGA due to surface roughness.
3. OSP (Organic Solderability Preservative)
• Cost: Low
• Shelf Life: 3 months
• Solderability: Normal
• Advantages: Cost-effective and efficient.
• Disadvantages: Not suitable for PTH and SMT mixed assembly. Poor thermal stability; should be soldered within 14 hours after first reflow. Not ideal for EMI grounding areas, mounting holes, or press-fit holes.
4. Gold Plating
• Cost: High
• Shelf Life: 12 months
• Solderability: High
• Advantages: Excellent solderability, conductivity, and durability with a smooth surface ideal for fine-pitch components.
• Disadvantages: High cost, with potential risk of embrittlement in solder joints.
5. Immersion Gold (ENIG)
• Cost: High
• Shelf Life: 12 months
• Solderability: High
• Advantages: Excellent solderability, conductivity, and long shelf life. Smooth surface ideal for fine-pitch applications.
• Disadvantages: Risk of “black pad” issues over time.
6. Immersion Silver
• Cost: Normal
• Shelf Life: 12 months
• Solderability: High
• Advantages: Excellent solderability at a cost-effective price. Smooth surface ideal for small ICs.
• Disadvantages: Sensitive to sulfur and can discolor at high temperatures.
7. Immersion Tin
• Cost: Normal
• Shelf Life: 12 months
• Solderability: High
• Advantages: Cost-effective with excellent solderability and smooth surface for small ICs.
• Disadvantages: Requires strict control of immersion tin chemicals and may be less durable than other finishes.
8. ENEPIG (Electroless Nickel Electroless Palladium Immersion Gold)
• Cost: High
• Shelf Life: 12 months
• Solderability: High
• Advantages: Prevents “black pad” issues and offers excellent durability and stability. A perfect alternative to OSP or ENIG.
• Disadvantages: Higher cost.
Omini provides a wide range of PCB surface finishes to meet your design and manufacturing needs, offering both cost-effective and high-performance options for your projects.
Shelf Life and Workshop Life for PCBs with Different Surface Finishes by Omini
At Omini, we understand that proper storage and handling of PCBs are essential to maintaining their quality. Below is a guide to the shelf life and workshop life of PCBs with different surface finishes.
1. Immersion Silver
• Storage Condition: Temperature ≤ 27°C, humidity ≤ 60%, no exposure to acid, alkali, or organic solutions
• Shelf Life: 6 months
• Workshop Life after Unpacking: ≤48 hours
2. (OSP) Organic Solderability Preservative
• Storage Condition: Temperature ≤ 27°C, humidity ≤ 60%, no exposure to acid, alkali, or organic solutions
• Shelf Life: 6 months
• Workshop Life after Unpacking: ≤24 hours
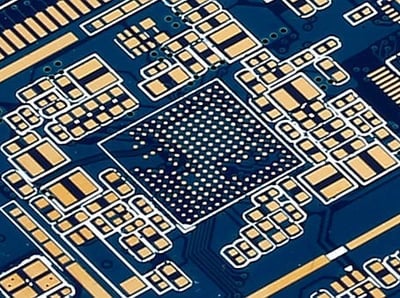
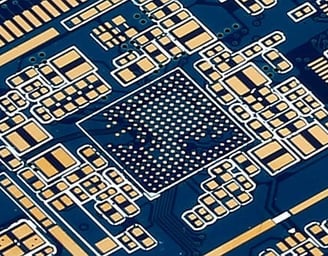
3. ENIG, ENEPIG, Plating Gold
• Storage Condition: Temperature ≤ 27°C, humidity ≤ 60%, no exposure to acid, alkali, or organic solutions
• Shelf Life: 6 months
• Workshop Life after Unpacking: ≤24 hours
4. Immersion Tin
• Storage Condition: Temperature ≤ 27°C, humidity ≤ 60%, no exposure to acid, alkali, or organic solutions
• Shelf Life: 6 months
• Workshop Life after Unpacking: ≤24 hours
5. (HASL) Hot Air Solder Level
• Storage Condition: Temperature ≤ 27°C, humidity ≤ 60%, no exposure to acid, alkali, or organic solutions
• Shelf Life: 6 months
• Workshop Life after Unpacking: ≤24 hours
Important Notes for HDI Boards:
• If storage time exceeds three months but is less than six months, PCBs need to be baked before production and assembled within 8 hours.
• Silver-Immersion PCB Baking: 120 ± 5°C for 2 hours, stacking height ≤ 2.5cm
• Whole Nickel Gold PCB Baking: 120 ± 5°C for 2-4 hours, stacking height ≤ 2.5cm
• OSP and Selective OSP PCB Baking: 120 ± 5°C for 2 hours, stacking height ≤ 2.5cm
• Ensure that the oven is clean and free of volatile gases from corrosive chemicals such as acids, alkalis, and organic solvents.
Omini ensures that the right conditions are met to maintain the integrity and performance of your PCBs throughout their lifecycle.
Contacts
Email: sales@ominipcba.com
Mobile: +86-185-7640-5228
Copyright © 2007-2025. Omini Electronics Limited. All rights reserved.
Head Office: +86-755-2357-1819
Products & Services
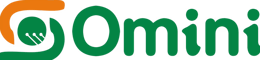
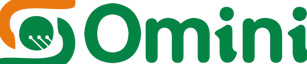
Office Address: No. 605, Tongxin Technology Building, Bao’an Avenue, Bao’an District, Shenzhen, Guangdong, China.
SMT Plant: A Building, Longwangmiao Industrial Park, Baishixia Community, Fuyong Street, Bao'an District, Shenzhen, China.
Omini Electronics Limited is an expert in trusted PCB Fabricaton and PCB Assembly in China since 2007. We have served over 1000 global customers with high-quality, low to medium-volume production. Certified by UL (E532498), ISO9001:2015, and ISO13485:2016, we offer expert electronics manufacturing services, including PCB manufacturing, assembly, and contract manufacturing, ensuring top-tier quality and precision in every project.