Phone: +86-755-2357-1819 Mobile: +86-185-7640-5228 Email: sales@ominipcba.com whatsapp: +8618576405228
PCB Assembly Tests & Inspections by Omini
At Omini, we prioritize delivering top-quality PCB solutions. Our comprehensive testing and inspection processes ensure reliability at every stage of production and post-assembly. Here’s how we guarantee excellence:
AOI (Automated Optical Inspection): Accurately detects assembly defects, misalignments, soldering issues, and missing components with precision.
ICT (In-Circuit Testing): Thoroughly verifies component integrity, circuit continuity, electrical performance, and proper connections.
Functional Testing: Ensures product functionality, durability, and performance under realistic operating conditions.
X-ray Inspection: Examines hidden solder joints, internal layers, and voids to maintain product reliability.
Visual Inspection: Conducted manually to identify visible defects, assembly errors, and overall component placement.
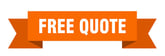
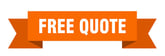
IQC (Incoming Quality Inspection) in PCB Assembly Process
IQC (Incoming Quality Inspection) is a vital step in the PCB assembly process. At Omini, we emphasize the importance of a rigorous IQC procedure to ensure that all components meet the highest standards of quality and reliability.
1. Component Inspection
IQC involves the thorough examination of each component, focusing on:
• Physical Characteristics: Size, shape, color, texture, and silkscreen.
• Electrical Properties: Resistance, capacitance, power, brightness, and other essential metrics.
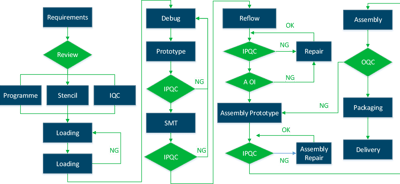
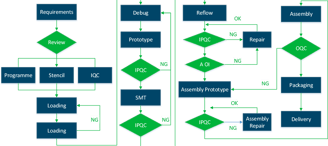
2. Minimizing Defects and Ensuring Consistency
This inspection guarantees that all parts used in the assembly process are defect-free and adhere to the required specifications, minimizing potential issues in production. By checking for defects, we ensure that faulty components don’t disrupt the assembly process, enhancing the overall quality of the finished product.
3. Counterfeit Prevention and Supply Chain Security
IQC also plays a crucial role in identifying counterfeit or substandard components before they enter the production line, safeguarding the quality and integrity of the final PCB assembly.
At Omini, we implement a strict IQC process to ensure that all components meet high-quality standards. This commitment allows us to deliver reliable and safe PCB assemblies that meet or exceed customer expectations.
Manual Visual Inspection in PCB Assembly
At Omini, we use a comprehensive range of testing methods to ensure the highest quality in our PCB assemblies. While we perform 100% electronic testing on our PCB bare boards, Automated Optical Inspection (AOI) for component accuracy, X-ray inspection for BGA soldering, In-Circuit Testing (ICT) for electrical connections, and Functional Testing (FCT) based on customer requirements, manual visual inspection remains a crucial part of the process.
1. Component and Soldering Inspection
Manual visual inspection focuses on:
• Inspecting components for correct placement and orientation.
• Evaluating solder joints for proper connection and quality.
• Checking overall PCB assembly integrity and surface finish.
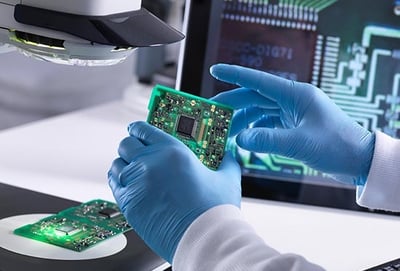
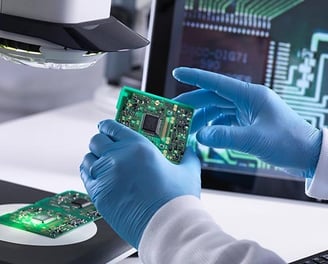
2. Identification of Potential Issues
This inspection method is essential for detecting minor visual defects that may not be caught by automated equipment, such as:
• Shorts, opens, or missing components.
• Misplaced components or incorrect orientations.
• General appearance inconsistencies that could affect the functionality of the PCB.
3. Economical Solution for Low-Volume Production
Manual visual inspection offers a cost-effective solution for verifying PCB assembly quality, particularly in quick-turn, low-volume production environments. Trained and experienced personnel use specialized visual inspection techniques to ensure the highest standards are met.
4. Minimizing Defects and Reducing Costs
By incorporating manual visual inspection, Omini can identify potential issues early, minimizing costly defects and reducing warranty claims. This inspection also helps streamline production processes, lowering costs associated with rework, scrap materials, and delays.
Manual visual inspection is a critical final step to ensure that all PCB assemblies meet customer expectations and industry standards before shipping. At Omini, we combine advanced automated testing and manual inspection to deliver reliable, high-quality products that ensure long-term customer satisfaction.
AOI (Automated Optical Inspection) in PCB Assembly
Automated Optical Inspection (AOI) is an advanced technology that plays a crucial role in ensuring the quality and accuracy of PCB assemblies. At Omini, we leverage cutting-edge AOI systems equipped with high-resolution cameras and specialized software to quickly detect and address defects in the manufacturing process.
1. Defect Detection and Component Placement Verification
AOI is used to inspect both surface mount and through-hole PCBs, making it versatile for a wide range of PCB designs. It performs:
• 2D and 3D inspections of component placements.
• Detection of subtle anomalies like solder joint defects, misalignments, and missing components.
2. Improved Quality Control
With AOI, Omini ensures consistent, high-quality output for every PCB assembly. This technology minimizes human error by automating the detection of defects that may be missed through manual inspection.
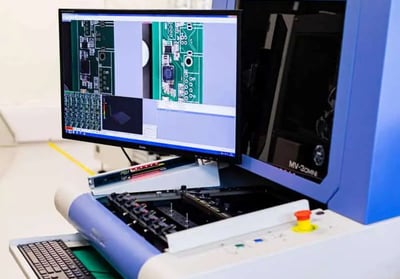
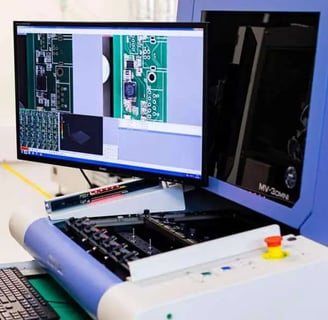
3. Cost Reduction and Efficiency
By identifying issues early in the process, AOI reduces the need for costly rework operations. This improves the overall production efficiency and helps lower costs related to faulty component placements or soldering issues.
4. High-Yield Manufacturing
AOI is crucial in achieving high yields in PCB assembly manufacturing. At Omini, we implement 100% Automated Optical Inspection (AOI) across all our PCB assemblies, ensuring that every product meets the required Bill of Materials (BOM) specifications before shipping.
With its speed and precision, AOI has become an indispensable tool for PCB assembly manufacturers worldwide, and Omini utilizes this advanced technology to deliver high-quality, reliable PCBs to our customers.
X-ray Inspection in PCB Assembly
X-ray Inspection is a highly specialized, non-intrusive testing method used to examine the internal connections of PCB assemblies, especially for complex components like BGA and flip-chip devices. At Omini, we integrate X-ray inspection to ensure the integrity of hidden solder joints and internal vias.
1. Non-Contact, High-Resolution Imaging
X-ray inspection allows for detailed imaging of internal connections without physically touching the PCB or its components. This enables us to:
• Inspect inner solder joints and vias.
• Detect potential defects in hidden connections that cannot be viewed with the naked eye.
2. Advanced Detection for Complex Components
Unlike traditional inspection methods, X-ray inspection is essential for detecting defects in components such as BGA and flip-chip, where solder joints are concealed beneath the components. Omini uses X-ray technology to accurately inspect these challenging areas, ensuring optimal solder joint quality.
3. Ensuring High-Quality Inner Connections
X-ray inspection is indispensable for verifying the quality of internal connections in complex PCBs. By using this advanced tool, Omini ensures that every PCB assembly meets the highest standards of quality before reaching the customer.
Whether it’s electronic testing for open/short circuits, Automated Optical Inspection (AOI) for component accuracy, In-Circuit Testing (ICT) for electrical connections, or Functional Testing (FCT), Omini ensures that all steps are taken to verify the quality and reliability of every PCB. For BGA, flip-chip, and other complex components, X-ray inspection provides the critical visibility needed for thorough evaluation.
ICT (In-Circuit Test) in PCB Assembly
In-Circuit Testing (ICT) is a critical part of the PCB assembly process at Omini. It ensures that every component on the PCB functions correctly and meets all necessary quality standards. ICT is vital for thoroughly testing individual components, including resistors, capacitors, transistors, and integrated circuits, while detecting any issues such as short circuits or open connections.
1. Comprehensive Component Evaluation
ICT allows for a detailed inspection of each component on the PCB, helping to ensure that:
• All components are correctly placed and functional.
• There are no short circuits or open connections between components.
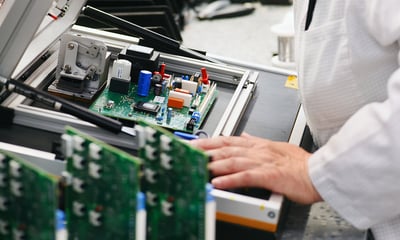
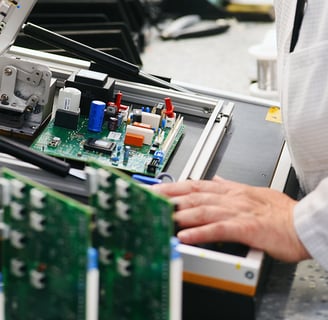
2. Quality Control and Error Prevention
Omini uses ICT as a reliable method to verify the correctness of PCB assemblies, helping eliminate costly errors and reducing the risk of failure during operation. This testing process helps maintain the highest levels of quality control throughout the manufacturing cycle.
3. Ensuring Operational Performance
By identifying any issues early in the process, ICT allows manufacturers to ensure that PCBs are fully operational and perform as expected. This process is essential in preventing potential defects and ensuring the functionality of the final product.
Omini employs ICT testing to guarantee that every PCB assembly is correctly assembled, high-quality, and ready for operational use.
FCT (Functional Test) in PCB Assembly
Functional Testing (FCT) is another essential process in the PCB assembly journey at Omini, designed to simulate the actual working conditions of a PCB to ensure it functions according to its intended design and specifications.
1. Simulating Real-World Conditions
FCT tests PCB assemblies by simulating real-world scenarios, ensuring that they perform under conditions similar to those they will face in end-use. This testing is crucial for:
• Verifying that each PCB assembly meets the required performance specifications.
• Identifying potential issues before the product enters production or reaches the customer.
2. Improving Product Quality and Reducing Delays
With FCT, Omini ensures that PCB assemblies meet customer expectations, helping to reduce production delays and the risk of returns due to malfunctioning boards. Proper implementation of FCT helps maintain the highest quality standards for the final product.
3. Limitations of FCT
While FCT is an invaluable tool, there are a few limitations:
• For smaller quantities or simpler PCBs, FCT may not always be necessary.
• FCT cannot simulate every possible function of a PCB or every component within it, limiting its scope for complex designs.
Despite these limitations, FCT is still an essential step to ensure that each PCB assembly meets the specified design and performance requirements before delivery to customers.
At Omini, we invest in a thorough FCT process to provide customers with high-quality, fully functional PCBs that meet all specifications.
FAI (First Article Inspection) in PCB Assembly
First Article Inspection (FAI) is a critical step in the PCB assembly process at Omini. It involves examining the initial PCB assemblies and comparing them to customer specifications to ensure that all components meet the required Bill of Materials (BOM) and design parameters. This thorough inspection process helps verify that the assembly is correct and functional before mass production begins.
1. Comprehensive Component Evaluation
During the FAI process, every component of a PCB assembly is meticulously inspected for:
• Accuracy, ensuring that all components are in the correct locations as per the BOM.
• Completeness, checking for missing parts or incorrect components.
• Compatibility and Fitment, ensuring that all parts are properly assembled and compatible.
• Functionality, including electrical performance tests such as continuity testing and resistance measurement.
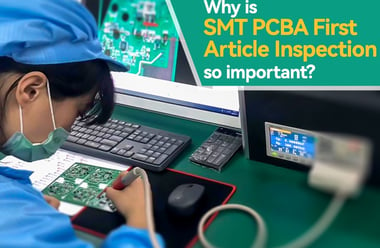
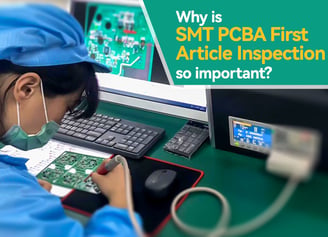
2. Ensuring Design Compliance and Reducing Defects
Omini utilizes FAI to verify that the PCB assemblies meet all customer design requirements. By identifying and addressing any discrepancies early, FAI helps to minimize the risk of product defects and ensures that the final product aligns with customer expectations. This process significantly reduces the likelihood of failures during mass production and enhances the overall quality of the final product.
3. Cost Savings and Risk Reduction
Conducting an FAI at the early stages of PCB assembly not only saves time and money but also helps to eliminate potential defects that could lead to costly production delays or failures. By ensuring that PCBs meet the necessary specifications, Omini helps reduce production risks and costs for our customers, ensuring a smoother path to full-scale manufacturing.
4. Compliance with Industry Standards
At Omini, FAI also ensures that our PCB assemblies adhere to industry standards such as IPC-A-610 and J-STD-001. By following these guidelines, we guarantee that every PCB meets the highest levels of quality and reliability before advancing to full production.
FAI is an essential quality assurance step in the PCB assembly process, and Omini is committed to delivering precision and accuracy at every stage to ensure the highest standards for our customers’ products.
Reliability Test in PCB Assembly
Reliability testing is a crucial step in the PCB assembly process at Omini. It ensures the stability, durability, and overall performance of PCB assemblies under various conditions. These tests are designed to evaluate how well different components interact and whether the PCB assembly can withstand harsh or fluctuating environments.
1. Testing Stability and Durability
Reliability tests at Omini involve simulating real-world conditions to assess the long-term performance of PCBs. These tests include:
• Vibration tests to simulate real-world movement and shock.
• Mechanical shock to measure resilience against sudden impacts.
• Drop tests to evaluate impact resistance.
• Pull and shear tests to assess the strength of solder joints and component attachment.
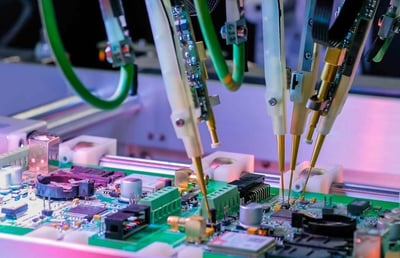
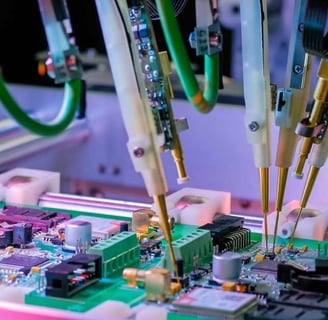
2. Environmental Stress Testing
To ensure that PCB assemblies perform in diverse environments, Omini conducts various environmental reliability tests, such as:
• High and low temperature cycling to simulate extreme temperature variations.
• Humidity exposure to test moisture resistance.
• Salt spray tests to assess corrosion resistance in saline conditions.
3. Comprehensive Performance Evaluation
In addition to physical testing, Omini also conducts solder fatigue analysis and thermal tests to identify potential weaknesses in PCB assemblies. These tests help to predict long-term reliability by exposing PCBs to conditions that simulate real-life stressors.
4. Ensuring Safety and Functionality
By regularly performing these reliability tests, Omini ensures that all PCB assemblies are safe to use, perform as expected, and can endure their intended environments. This process significantly reduces the risk of PCB failure during operation, offering peace of mind to our customers.
Common Reliability Tests Performed at Omini:
• Vibration Test
• Mechanical Shock
• Drop Test
• Pull & Shear Test
• Bending Test
• Thermal Test
• Salt Spray Test
• Burn-In Test
At Omini, we implement reliability testing to ensure that every PCB assembly is of the highest quality and can withstand the demands of real-world usage. These tests are essential for ensuring that our products meet safety standards and perform consistently over time.
Contacts
Email: sales@ominipcba.com
Mobile: +86-185-7640-5228
Copyright © 2007-2025. Omini Electronics Limited. All rights reserved.
Head Office: +86-755-2357-1819
Products & Services
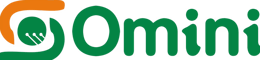
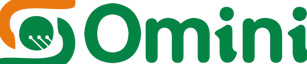
Office Address: No. 605, Tongxin Technology Building, Bao’an Avenue, Bao’an District, Shenzhen, Guangdong, China.
SMT Plant: A Building, Longwangmiao Industrial Park, Baishixia Community, Fuyong Street, Bao'an District, Shenzhen, China.
Omini Electronics Limited is an expert in trusted PCB Fabricaton and PCB Assembly in China since 2007. We have served over 1000 global customers with high-quality, low to medium-volume production. Certified by UL (E532498), ISO9001:2015, and ISO13485:2016, we offer expert electronics manufacturing services, including PCB manufacturing, assembly, and contract manufacturing, ensuring top-tier quality and precision in every project.