Phone: +86-755-2357-1819 Mobile: +86-185-7640-5228 Email: sales@ominipcba.com whatsapp: +8618576405228
Omini Conformal Coating Solutions
Omini provides a comprehensive, high-quality conformal coating service designed to meet the unique demands of the PCB industry. Our expertise spans across multiple techniques, ensuring reliable protection for your PCB assemblies. Our solutions are ideal for a variety of industries and applications.
Conformal Coating Techniques: Brushing, Spray, and Dipping for optimal protection.
PCB Parts Sourcing & Fabrication: High-quality PCB sourcing and fabrication for efficient production.
PCB Assembly & Box Build: Full turnkey assembly services, including box build and functional testing.
Certifications: ISO9001:2015, ISO 13485:2016 Certified & UL Listed for industry compliance.
Comprehensive Testing: 100% E-test, AOI, X-RAY, ICT & FCT to ensure the highest quality standards.
No Minimum Order Quantity (MOQ): Flexible production with competitive pricing tailored to your needs.
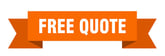
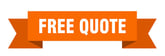
What is Conformal Coating?
Conformal coating is a thin protective layer applied to Omini’s printed circuit boards (PCBs), designed to shield electronic components or PCB bare boards from environmental threats such as heat, moisture, dust, chemicals, and vibrations. This protective coating plays a crucial role in enhancing the performance and longevity of PCBs in challenging conditions.
1. Electrical Insulation: Conformal coatings help improve the electrical insulation of PCBs, preventing electrical shorts and failures in complex circuit designs.
2. Corrosion Protection: These coatings act as a barrier against moisture and chemicals, offering essential protection to prevent corrosion and oxidation on sensitive components.
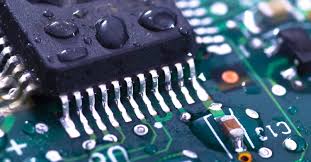
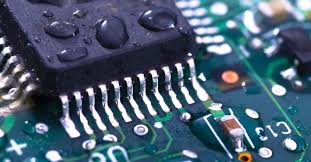
3. Reliability in Harsh Environments: Conformal coatings increase the reliability of PCBs, allowing them to perform effectively in demanding environments, including aerospace, automotive, and medical applications.
At Omini, we specialize in providing high-quality PCB solutions, ensuring your electronics remain durable and high-performing in extreme conditions.
Types of Materials Used in Conformal Coatings
At Omini, we provide advanced conformal coating solutions for PCBs, offering protection against environmental threats while enhancing reliability. Different materials are used for conformal coatings based on the specific needs of various industries. Here are the main types:
1. Acrylic: Acrylic coatings are commonly used for consumer electronics, offering excellent protection against environmental pollutants and moisture. They are easy to apply and remove, making them ideal for mass production of PCBs in consumer-grade devices.
2. Silicone: Known for their flexibility and high-temperature resistance, silicone-based coatings are widely used in automotive and aerospace industries. These coatings provide excellent protection against thermal stress, which is a critical factor in these sectors.
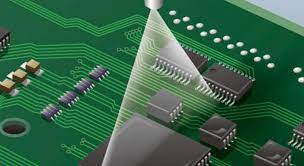
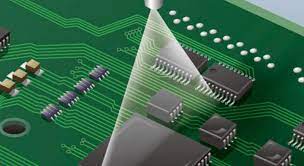
3. Urethane: Urethane coatings are highly resistant to chemicals and offer strong mechanical properties. These coatings are perfect for industrial electronics that need protection from harsh chemical environments, ensuring long-term durability and reliability.
4. Epoxy: Epoxy conformal coatings are renowned for their abrasion and solvent resistance, making them ideal for PCBs exposed to physically demanding conditions. This type of coating provides a strong barrier, ensuring the PCB performs optimally even in challenging environments.
5. Parylene: Parylene coatings offer superior protection against moisture and chemicals and are applied using vapor deposition. This material is often used in the medical device and military electronics industries due to its uniform coating and high-performance characteristics.
Incorporating these materials into conformal coating for PCBs allows Omini to deliver robust, high-performing PCB solutions that can withstand harsh operational environments while maintaining excellent functionality and reliability.
Application Methods for Conformal Coating on PCBs
At Omini, we offer advanced conformal coating services for PCBs, ensuring enhanced protection and reliability in various industrial applications. Different application methods are used to apply the conformal coating, depending on the specific requirements of the PCB and the volume of production. Here are the main techniques:
1. Compatibility Issues
Choosing the right conformal coating material is crucial for the success of your PCB assembly. Incompatible coatings can lead to failures, such as poor adhesion or chemical reactions with PCB components. At Omini, we ensure the coating is selected based on the PCB’s operating environment and the potential for chemical exposure, preventing any adverse effects on functionality.
2. Application Potential Problems
The application of conformal coating can face several challenges, such as de-wetting and cracking. If the coating is applied too thickly or cures too quickly, it may crack, compromising the integrity of the protection. Uneven coverage, caused by de-wetting, can leave areas of the PCB exposed, and the “orange peel” effect can negatively impact both aesthetics and performance. At Omini, we monitor the coating application process closely to ensure consistent and effective results.
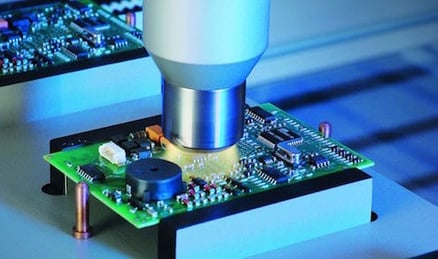
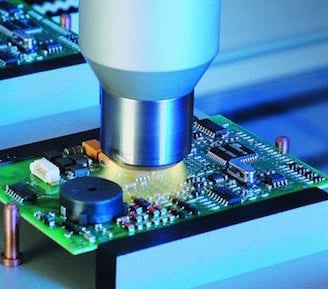
3. The Importance of Thickness and Uniformity
Proper thickness and uniformity of the conformal coating are vital to ensuring the PCB’s protection against environmental factors. An uneven coating can lead to insulation issues and gaps in the moisture barrier, weakening the PCB’s protective capabilities. Omini strictly controls the coating process to ensure uniform application and optimal protection for your PCBs.
4. Inspection of Conformal Coating for PCB
To ensure the effectiveness of the conformal coating, Omini uses advanced tools like UV light and microscopes for thorough inspection. UV light helps identify coverage inconsistencies, while microscopes are used to detect micro-level faults such as bubbles or thin spots that could affect the functionality of densely packed assemblies.
5. Lifespan and Durability Considerations
The durability of a conformal-coated PCB depends on both the quality of the coating application and the operational environment. At Omini, we provide ongoing maintenance and repair services to ensure that your PCBs continue to perform reliably. Our coating solutions are designed to withstand environmental stresses, ensuring sustained performance over time.
6. Conformal Coating Repair Considerations
If damage occurs to the conformal coating, Omini offers expert repair services. This involves the careful removal of the damaged coating, either through solvent or mechanical means, followed by a thorough cleaning process. The new coating is then re-applied precisely to restore the protective integrity of the PCB without compromising its functionality.
Why Choose Omini for Your PCB Conformal Coating Services?
At Omini, we provide high-quality PCB conformal coating services that enhance the reliability and lifespan of your printed circuit boards (PCBs). Our services are designed to withstand tough environmental conditions, including electrical and mechanical stresses, ensuring the durability and performance of your products in challenging environments.
1. Meet Industry Standards with Precision
Conformal coating for PCBs is a critical process that ensures your PCBs meet industry standards for quality and reliability. At Omini, we follow the widely accepted IPC-CC-830 standard for conformal coatings, which outlines the acceptable types of coatings, application methods, and inspection criteria. Our strict adherence to these standards ensures consistent results and high-quality coatings that enhance your PCB’s longevity and performance.
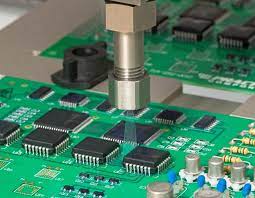
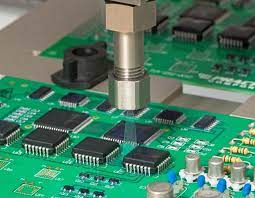
2. Experience Across Various Industries
Omini brings years of expertise in PCB conformal coating, with tailored solutions for diverse industries. Whether it’s the automotive, aerospace, or consumer electronics sectors, we ensure our coatings meet the unique durability and resistance standards of each industry. For the automotive and aerospace industries, we provide coatings that offer superior protection under extreme conditions. In consumer electronics, our coatings safeguard devices while maintaining their functionality, offering long-term protection without compromising performance.
3. No Minimum Order Quantity
At Omini, we understand that the conformal coating process can be complex, and any errors during mass production can lead to significant losses. That’s why we offer pre-production samples for customer inspection to ensure that everything meets your specifications before full-scale production begins. Whether you require small or medium-volume PCB conformal coating services, we’re equipped to handle your needs with precision. There’s no need to worry about large order quantities—Omini specializes in flexible, small-batch production, making it easier for you to get the coatings you need, no matter the size of your order.
With Omini, you can confidently rely on our high-quality, efficient, and industry-compliant PCB conformal coating services for all your project requirements.
Contacts
Email: sales@ominipcba.com
Mobile: +86-185-7640-5228
Copyright © 2007-2025. Omini Electronics Limited. All rights reserved.
Head Office: +86-755-2357-1819
Products & Services
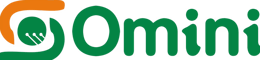
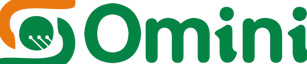
Office Address: No. 605, Tongxin Technology Building, Bao’an Avenue, Bao’an District, Shenzhen, Guangdong, China.
SMT Plant: A Building, Longwangmiao Industrial Park, Baishixia Community, Fuyong Street, Bao'an District, Shenzhen, China.
Omini Electronics Limited is an expert in trusted PCB Fabricaton and PCB Assembly in China since 2007. We have served over 1000 global customers with high-quality, low to medium-volume production. Certified by UL (E532498), ISO9001:2015, and ISO13485:2016, we offer expert electronics manufacturing services, including PCB manufacturing, assembly, and contract manufacturing, ensuring top-tier quality and precision in every project.