Phone: +86-755-2357-1819 Mobile: +86-185-7640-5228 Email: sales@ominipcba.com whatsapp: +8618576405228
Multilayer PCB Solutions by Omini
Omini offers high-quality multilayer PCB solutions with competitive pricing, ensuring top-notch performance across various applications. Our advanced PCB manufacturing services include:
PCB Types Offered: Rigid, Flex, Rigid-Flex, HDI, High TG, High Speed, High Frequency, Backplane, Embedded PCBs, IC Substrates
Layer Options: 4-40 Layers for mass production and up to 100 Layers for prototypes
Advanced Via Technologies: Blind & Buried Vias, Staged & Staggered Vias, Back Drill
Via Plugging Solutions: Conductive & Non-conductive Via Plugging, VIAPPO
Quality Certifications: ISO9001:2015 Certified & UL Listed
Comprehensive Testing: 100% E-test, AOI Test, and Visual Inspection for quality assurance
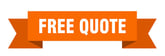
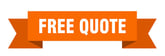
What Is A Multilayer PCB?
A multilayer PCB is a printed circuit board with more than two copper layers. In contrast to single-sided PCBs and double-sided PCBs, which only feature one or two copper layers, a multilayer PCB typically ranges from 4 to 18 layers, and can even extend to 100 layers in specialized applications.
Key Features of Multilayer PCBs:
1. Outer Layers: The top and bottom layers of the PCB, where SMD (Surface Mount Devices) and DIP (Dual Inline Package) components are typically placed.
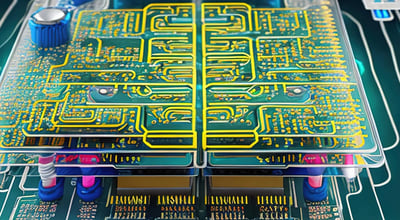
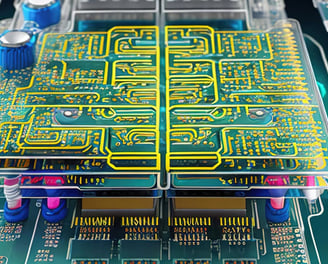
2. Inner Layers: The signal layer, power ground layer, and plane layer are essential components of the PCB’s inner structure.
3. Layer Bonding: These layers are bonded together using dielectric cores and prepregs, creating a “sandwich” structure.
4. Via Types: The layers are interconnected using through-hole drills, blind vias, and buried vias, enabling complex electronic connections.
Omini specializes in providing high-quality multilayer PCB solutions, offering exceptional design and manufacturing capabilities to meet the unique needs of your electronic applications. We ensure precision and performance across all layers, ensuring that your product is reliable, durable, and optimized for your application.
Main Components of Multilayer PCB
Omini, a leading provider of high-quality PCB solutions, ensures that every multilayer PCB meets the highest standards. Below are the key components that make up a typical multilayer PCB:
• Core: The core of a multilayer circuit board is composed of conductive copper layers, which are responsible for conducting electrical signals and distributing power across the board.
• Prepreg: Prepreg is the insulating material used to bond the cores together. It connects the layers in the PCB stack-up and ensures structural integrity.
• Copper Foil: Copper foil is applied as the initial copper thickness on both the inner and outer layers of a multilayer PCB, forming the conductive pathways for electrical signals.
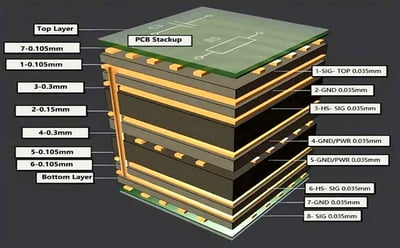
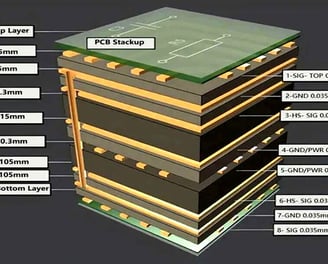
• Solder Mask: The solder mask is a protective layer that shields the components on the multilayer circuit board from external environmental factors like oxidation, corrosion, and staining.
• Surface Treatment: Surface treatment is a process used during PCB fabrication to treat exposed copper surfaces, preventing issues like short circuits, oxidation, and open circuits.
• Vias: Vias are the holes that allow electrical connections between different layers in a multilayer circuit board. These include through holes, blind vias, buried vias, and back-drilled vias, each providing different methods of connecting layers in complex PCB designs.
Different Types of Vias in Multilayer PCB
When it comes to designing and manufacturing multilayer PCBs, vias play a crucial role in connecting different layers of the circuit board. Omini, as a leader in PCB design and manufacturing, offers various types of vias to meet different application needs.
1. Through Hole Drills (Including Vias)
Through-hole drills or vias connect all layers of the PCB from the top to the bottom. These vias are commonly used in traditional PCB designs and are the most basic type for electrical connections across layers.
2. Blind Vias
Blind vias are electrical connections between the outer layer (either top or bottom) and one or more of the inner layers. They do not extend all the way through the PCB, making them ideal for applications that require more complex routing but without affecting the overall structure.
3. Buried Vias
Buried vias are connected only to inner layers of the PCB and are not visible from the outer layers. This type of via is used to create compact designs without compromising space on the outer layers, which is crucial for high-density applications.
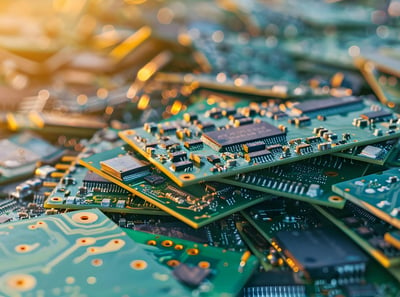

4. Stacked Vias
Stacked vias are aligned vertically, allowing multiple layers to be connected in a straight line. This type of via is commonly used for high-performance applications where minimal routing space and effective electrical connection are essential.
5. Staggered Vias
Staggered vias are designed with a slight offset between adjacent layers, providing a more efficient layout for routing in compact designs. This via configuration ensures that the electrical connection between layers is optimized without compromising the overall functionality.
6. Micro Vias
Microvias are extremely small vias, typically less than 0.15mm in diameter, and are commonly used in HDI (High-Density Interconnect) multilayer PCBs. These vias are ideal for miniaturized designs and are often found in advanced applications such as mobile devices and wearable electronics.
Advantages of Multilayer PCB
Multilayer PCB boards offer numerous advantages, making them a crucial component in modern electronic design. The primary benefit of a multilayer PCB is that it enables more components and functionalities in a smaller area. As electronic components continue to shrink, it becomes possible to reduce the PCB size while retaining exceptional features. Omini, a leader in PCB design and manufacturing, maximizes these benefits for clients with advanced multilayer solutions. Below are some of the key advantages of multilayer PCBs:
1. Minimized PCB Size: Omini ensures that multilayer PCBs can be designed to a smaller size by utilizing inner layers, adhering to PCB design rules, without sacrificing functionality.
2. High Component Density: Multilayer PCBs allow for higher component density, making them ideal for compact and complex designs.
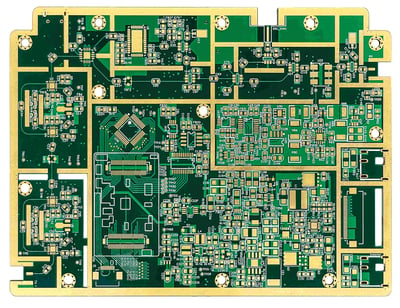
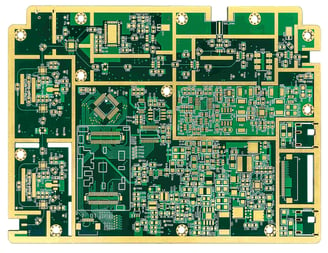
3. Enhanced Functionality: By incorporating more wires and drills, multilayer PCBs facilitate numerous electronic connections, offering greater versatility and functionality compared to simpler boards.
4. Powerful Performance: Multilayer PCBs are perfect for placing high-power components, optimizing performance for demanding applications.
5. High Thermal Conductivity: These PCBs provide excellent heat dissipation, which is essential for high-performance applications where thermal management is critical.
6. Superior Mechanical Strength: Omini’s multilayer PCBs offer high mechanical strength, making them suitable for handling heavy components and ensuring durability in various environments.
Disadvantages of Multilayer PCB
While multilayer PCBs offer numerous advantages, there are also certain disadvantages to consider. Omini, as an expert in PCB design and manufacturing, ensures that these challenges are addressed with precision, but it’s important to understand the potential drawbacks:
1. More Complex Manufacturing Process: The production of multilayer PCBs requires more intricate procedures compared to simpler boards. Due to the multiple layers and specialized processes involved, Omini ensures high-quality control but it is a more time-intensive procedure.
2. Higher Cost: Manufacturing multilayer PCBs is generally more expensive due to the specialized techniques required. The additional processes and materials increase the overall cost. Any issues during production may require extensive rework, which can further increase expenses. Omini works to optimize costs while maintaining quality standards.
3. Longer Manufacturing Time: The process of producing multilayer PCBs typically takes longer, as more steps are involved in creating and testing the layers. While Omini has advanced machinery that helps reduce production times, it remains a more time-consuming process than simpler PCB types.
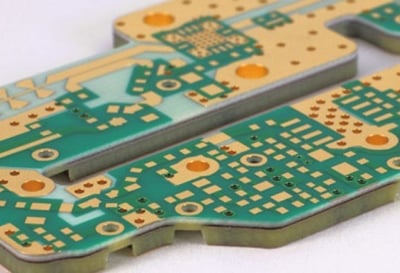
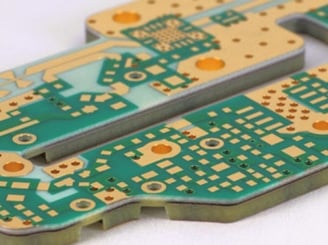
Manufacturing Process of Multilayer PCB
The production of multilayer PCBs involves several specialized processes, depending on specific requirements such as edge plating, hole castellation, via-fill and plugging, blind-buried vias, and more. Below is an overview of the typical multilayer PCB manufacturing process, as provided by Omini, a leader in PCB design and manufacturing services.
1. DFM Check
The Design for Manufacturability (DFM) check ensures all layers of the multilayer PCB are reviewed for errors before production. Omini’s DFM engineers verify design flaws, enabling a smooth production process without errors or delays.
2. Material Selection and Cutting
For every multilayer PCB, materials are selected based on order requirements, and then precisely cut to size. Omini offers a wide range of high-quality materials to meet the specific needs of each PCB design.
3. Inner Layers Process
During this phase, the inner layer images are transferred to the multilayer PCB using UV films and dry films. The unwanted copper is then etched away, leaving the desired circuitry pattern. This step ensures the precision and reliability of the board.
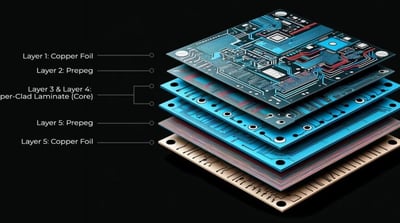
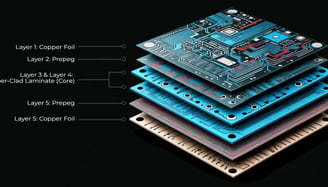
4. AOI (Automated Optical Inspection)
AOI inspects the board by converting the circuitry image to a digital form, allowing for defect detection. Any issues identified at this stage are manually verified by the inspection team, ensuring only defect-free multilayer PCBs proceed to the next stages.
5. Lamination
Lamination bonds the inner copper foil, core, and prepregs together under heat and pressure. Omini ensures this process is meticulously controlled to form strong, reliable layers within the multilayer PCB.
6. Drilling
The drilling process is crucial for creating holes that connect different layers of the multilayer PCB. Whether for through-holes, blind vias, or buried vias, Omini’s advanced drilling machines follow precise data to ensure accuracy and performance.
7. Copper Plating
In this step, the PCB is submerged in a copper plating bath to enhance its thickness and durability. This step strengthens the multilayer PCB, ensuring it can handle higher electrical loads and stress.
8. Outer Layer Process
The outer layers are processed similarly to the inner layers, with image transfer and etching techniques used for precise design. Omini ensures that the top and bottom layers meet all the necessary standards for reliable performance.
9. Masking and Legend Printing
After copper layers are completed, Omini applies a solder mask to protect the components from external factors like oxidation. The silkscreen legend is also printed to indicate component orientation, part numbers, and company logos.
10. Surface Finish
To enhance performance and protect the PCB, Omini applies a surface finish as per customer requirements. This process improves the solderability and testing ability of the multilayer PCB.
11. Electrical Testing
At this stage, all electrical connections on the multilayer PCB are tested using advanced equipment to ensure there are no shorts or broken tracks. Omini employs flying probe testing to verify the integrity of every board.
12. Routing and Scoring
For multilayer PCBs with non-standard shapes, routing and scoring processes are performed. This is essential for depanelizing the PCB, ensuring it meets both customer specifications and industry standards.
13. Final Inspection and Packing
After production, each multilayer PCB undergoes a final inspection to ensure quality. Omini ensures that every board is thoroughly checked for defects before being securely packed and shipped to the client.
Why Choose Multilayer PCB from Omini?
When compared to single-layer boards and double-layer boards, the multilayer PCB manufacturing process is more complex and precise. This makes it a significant challenge for PCB manufacturers. When selecting a reliable multilayer PCB manufacturer, factors such as reputation, technology, equipment, experience, and industry scale are crucial. If you have specific requirements, consider Omini—a trusted multilayer PCB supplier in China. We offer flexible solutions tailored to your needs and prioritize customer satisfaction. Choosing Omini brings the following benefits:
1. 100% High-Quality Guarantee: We ensure all multilayer PCBs meet the highest quality standards, delivering reliable and durable products.
2. Over 98% On-Time Delivery Rate: With Omini, you can trust that your orders will arrive on time, every time.
3. Low-Volume Orders Accepted: We accept small batch orders, starting from just 1 piece, offering flexibility for prototyping and low-volume production.
4. Full Process Contracting Service: From design to delivery, Omini provides end-to-end PCB manufacturing solutions, ensuring seamless production at every stage.
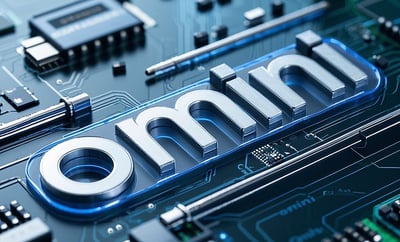
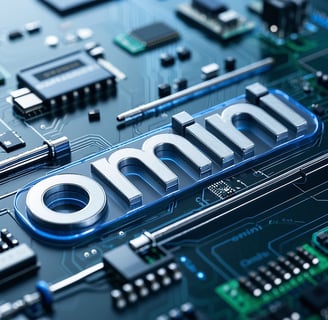
5. Customer-Oriented, Flexible Customized Solutions: At Omini, we offer customized PCB solutions that are designed to meet your specific needs, with a focus on optimizing functionality and cost.
If you have further questions about multilayer circuit boards, feel free to consult Omini. We look forward to working with you and providing the best PCB solutions for your needs!
Contacts
Email: sales@ominipcba.com
Mobile: +86-185-7640-5228
Copyright © 2007-2025. Omini Electronics Limited. All rights reserved.
Head Office: +86-755-2357-1819
Products & Services
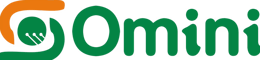
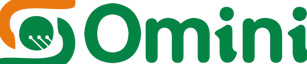
Office Address: No. 605, Tongxin Technology Building, Bao’an Avenue, Bao’an District, Shenzhen, Guangdong, China.
SMT Plant: A Building, Longwangmiao Industrial Park, Baishixia Community, Fuyong Street, Bao'an District, Shenzhen, China.
Omini Electronics Limited is an expert in trusted PCB Fabricaton and PCB Assembly in China since 2007. We have served over 1000 global customers with high-quality, low to medium-volume production. Certified by UL (E532498), ISO9001:2015, and ISO13485:2016, we offer expert electronics manufacturing services, including PCB manufacturing, assembly, and contract manufacturing, ensuring top-tier quality and precision in every project.