Phone: +86-755-2357-1819 Mobile: +86-185-7640-5228 Email: sales@ominipcba.com whatsapp: +8618576405228
Free DFM & DFA Services by Omini
Looking to optimize your PCB designs? Omini offers free DFM and DFA services to ensure your designs are cost-effective, manufacturable, and assembly-friendly, helping you accelerate production and reduce potential issues.
Omini offers free Design for Manufacturing (DFM) and Design for Assembly (DFA) services, ensuring your PCB designs are optimized for efficient production and cost-effective assembly.
Our expert team at Omini reviews your designs to identify potential issues early, minimizing delays and ensuring seamless production throughout the PCB lifecycle.
Omini’s DFM & DFA services help improve PCB performance, reduce costs, and enhance manufacturability, providing you with a competitive edge in your industry.
By incorporating DFM & DFA during the design phase, Omini helps streamline your assembly process and reduce the risk of errors, leading to faster time-to-market.
Get in touch with Omini today to take advantage of our free DFM & DFA analysis and optimize your PCB designs for both quality and efficiency.
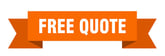
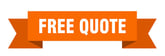
What is PCB DFM/DFA?
DFM (Design for Manufacturing) and DFA (Design for Assembly) are essential concepts in PCB design that directly impact the efficiency, quality, and cost-effectiveness of the manufacturing and assembly processes.
• DFM refers to designing PCBs in a way that ensures high functional performance, while also simplifying the manufacturing process. It aims to enhance manufacturing efficiency, reduce defect rates, minimize production costs, and ensure high-quality outputs.
• DFA focuses on the assembly phase, ensuring that the PCB design supports a simple and efficient assembly process. The goal is to achieve high assembly efficiency, reduce defects, lower costs, and improve overall product quality.
At Omini, we prioritize DFM and DFA principles to offer our customers the best in PCB design, manufacturing, and assembly services.
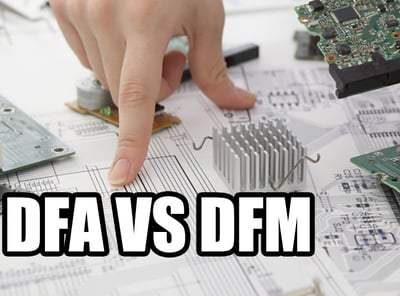
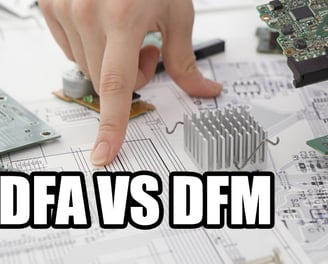
Why Do We Need DFM/DFA?
Implementing DFM/DFA strategies is crucial for optimizing PCB production and ensuring the best possible outcomes. Here are the key benefits:
1. Prevent Design Errors: Avoid costly mistakes and design flaws that could affect product functionality or manufacturing.
2. Provide Cost-Saving Advice: Omini helps customers identify cost-saving opportunities and reduce production time.
3. Reduce Communication Costs: Minimize disputes and improve collaboration by streamlining the design and manufacturing process.
4. Minimize Design Iterations: Reduce the number of design revisions needed during product development, accelerating time to market.
5. Accelerate Time to Market: Speed up the overall process, helping you get your product to market faster.
6. Enhance Manufacturing and Assembly Quality: Reduce defects in both PCB manufacturing and assembly, resulting in higher output.
7. Enable Concurrent Engineering: Support intelligent manufacturing with design processes that align with production, making both design and manufacturing smoother.
8. Improve Equipment Reliability: Ensure longer equipment lifespan and greater reliability by optimizing design and assembly processes.
9. Reduce Product Release Costs: Save money in the release phase by optimizing your design for efficient production and assembly.
At Omini, our DFM and DFA expertise ensures your PCB designs are ready for high-quality, efficient manufacturing and assembly, helping you achieve superior results at reduced costs.
What Free DFM Services Do We Offer at Omini?
At Omini, we provide a comprehensive range of DFM (Design for Manufacturing) services aimed at optimizing your PCB designs for efficient production and high-quality outcomes. Below are the key areas of our free DFM support:
1. Material Suggestions and Alternatives
With a wide range of materials available globally, Omini cannot always stock every specific material requested. However, if we don’t have your specified material in stock, we’ll suggest suitable alternatives to meet your design needs. If you prefer a particular material or brand, we can procure it based on your exact requirements.
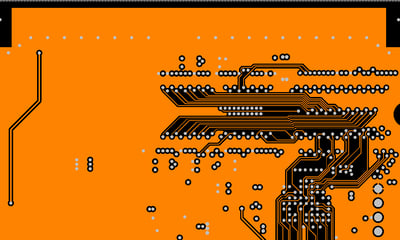
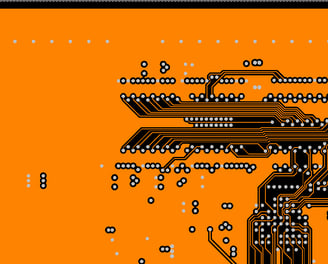
2. Stack-up Design Recommendations
• While we typically manufacture PCBs according to your provided stack-up, there are cases where we may suggest modifications. Common reasons include:
• Unavailability of the specified core/prepreg or copper thickness.
• Inability to meet controlled impedance requirements.
• Potential failure risks associated with the specified stack-up.
• Any proposed changes will be communicated for customer approval before production begins, ensuring your final design meets all specifications.
3. Panel Design Advice
In cases where customers do not provide panel drawings or specifications, Omini will step in to provide panel design recommendations. This is crucial for ensuring efficient assembly. For instance, we advise against using panels with edge connectors inside the panel, as this can hinder proper chamfering on gold connectors and affect assembly quality.
4. Tolerances and Compliance
Tolerances are critical in PCB manufacturing. At Omini, we ensure that all critical tolerances—such as overall thickness, outline dimensions, copper trace width/space, impedance values, copper plating, and surface finish—are meticulously adhered to. Our CAM engineers review all drawings and will consult with you if tolerances cannot be met. If no specific tolerances are provided, we will produce your PCB according to IPC-A-600 Class 2 standards to guarantee high-quality manufacturing.
CAM Design Services at Omini
At Omini, our CAM (Computer-Aided Manufacturing) design services are essential for ensuring that your PCB designs are optimized for high-quality production and assembly. Below are some key areas of focus in our CAM design process:
1. Copper Trace Design and Integrity
Ensuring that copper traces are correctly routed and free from defects is crucial for proper PCB functionality. Omini carefully checks for any broken traces that could compromise the integrity of the circuit.
2. Etching Quality and Layer Reversal
Etching issues can occur when characters are reversed between layers (e.g., the bottom layer is positive and the top layer is negative). At Omini, we carefully analyze the etching process to avoid these issues, which can affect wiring levels and overall design performance.
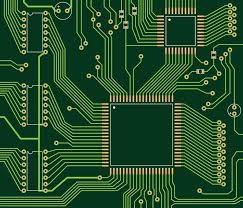
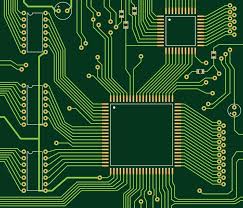
3. Pad-to-Edge Clearance
Omini ensures that the pad-to-board edge distance meets the required specifications to prevent damage during the profiling process. Insufficient clearance can lead to pad damage during production.
4. Thermal Pad and Isolation Pad Overlap
When thermal pads overlap with isolation pads, continuity cannot be determined. Omini addresses this issue to ensure that the PCB’s thermal management is optimized for performance.
5. Power and Ground Layer Isolation
Omini verifies that the isolation area between power and ground layers is sufficient to prevent unwanted connections. Insufficient isolation can lead to signal interference or circuit failure.
6. Circuit Spacing and Safety
Proper spacing between circuits is critical for ensuring the reliability of the PCB. Omini ensures that distances between traces meet industry standards, preventing electrical shorts or signal interference.
7. Inner Layer Isolation Pad Clearance
We check that the distance between inner layer isolation pads is sufficient to avoid shorts or design faults. Proper clearance is essential for maintaining the integrity of multi-layer PCBs.
8. Dummy Copper Pads for Large Free Areas
Omini recommends adding dummy copper pads in large areas that are free from copper to prevent issues like board bowing and twisting. This is particularly important for high-density designs.
9. Drill Integrity in Separate Areas
Ensuring that drill holes are properly located and do not interfere with other pads or traces is crucial for high-quality manufacturing. Omini verifies the placement of drill holes in separate areas to maintain PCB integrity.
At Omini, we ensure that your PCB designs undergo rigorous CAM design checks, optimizing them for reliable, high-performance manufacturing and assembly. Our CAM experts work to identify and resolve issues early in the design process, helping you avoid costly errors and delays.
Solder Mask Considerations at Omini
At Omini, we ensure that your PCB design meets the highest quality standards, particularly in the application of solder mask. Here are some common issues we check during the solder mask phase:
1. Fiducial Marks Free from Solder Mask
It’s essential to keep fiducial marks free from solder mask to ensure proper alignment during assembly. Omini carefully checks for this in every design to avoid errors.
2. Solder Mask Opening on Fiducial
If the solder mask opening on fiducials is too large, it can cause alignment issues during the assembly process. Our engineers will identify and resolve such issues to ensure accuracy.
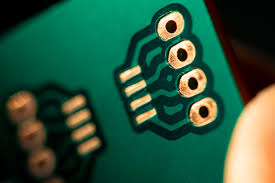
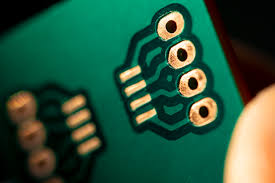
3. Excessive Solder Mask Opening on Pads/Traces
Omini ensures that there is no unnecessary solder mask opening on pads and traces. This can lead to poor electrical performance and affect soldering quality.
4. Edge Connectors Not Fully Free from Solder Mask
Edge connectors should be completely free from solder mask to ensure proper connection. Omini ensures that edge connectors are correctly defined in your PCB design.
Silkscreen Quality Control at Omini
Omini also prioritizes the quality and clarity of the silkscreen layer, as it plays a key role in the PCB assembly process. Poor silkscreen can lead to assembly errors and affect the overall appearance of your board. Here are common silkscreen issues we address:
1. Silkscreen on Pads
Silkscreen should not overlap pads, as this can obstruct the placement of components. Omini checks for this error to ensure proper assembly.
2. Crowded Silkscreen
Overcrowded or illegible silkscreen can make it difficult to read labels and affect assembly accuracy. We ensure that the text and graphics are clear and well-spaced.
3. Silkscreen Outside Board Edge
Silkscreen that extends beyond the edge of the PCB can cause production and inspection issues. Omini ensures that silkscreen stays within the board’s defined area.
4. Small or Overlapped Silkscreen
Silkscreen that is too small or overlapped can result in illegible markings. Our engineers ensure that all markings are correctly sized and positioned.
5. Negative Words on Top Layer
Words or symbols should not be in negative form on the top layer, as this can confuse assembly technicians. Omini carefully checks for this issue during the design review.
Drill and Hole Quality at Omini
Proper hole placement and size are critical for the functionality and assembly of PCBs. Omini rigorously checks the drilling process for common issues:
1. Vias and PTH Holes Overlap
When vias and PTH holes overlap, it can cause structural integrity issues. We ensure that vias and pads are correctly positioned to avoid interference.
2. Missing Notes for Special Holes
Special holes (e.g., slots or non-plated holes) should be clearly marked in the drill drawing. Omini checks for missing or incorrect hole attributes to ensure accurate manufacturing.
3. Drill Size Matching PTH Pin Size
Drill holes must be slightly larger than the pin size of PTH components to ensure proper fit. Omini ensures that the drill sizes are correctly specified to accommodate component pins.
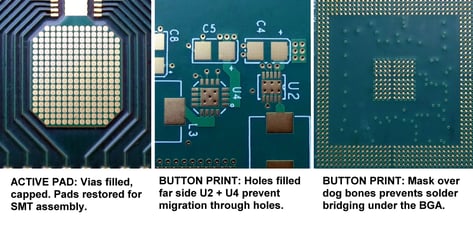
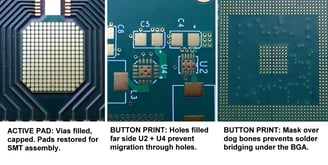
Blind and Buried Vias at Omini
Omini is experienced in producing HDI (High-Density Interconnect) PCBs with blind and buried vias. These via types are commonly used to save space and improve functionality. Here’s what we recommend:
1. Symmetrical Structure for Easy Production
We advise a symmetrical structure for blind and buried vias to simplify production. This design reduces the risk of bow and twist, ensuring that your PCB remains flat and reliable during manufacturing.
2. Design for Functionality and Reliability
While blind and buried vias are essential for high-density designs, we always ensure that these vias are properly designed to enhance the PCB’s function while maintaining manufacturing ease.
At Omini, we ensure that your PCB designs are optimized for production by addressing critical factors like solder mask application, silkscreen quality, drill hole placement, and via design. Our CAM engineers carefully review every aspect to ensure that your PCBs are produced with the highest level of quality and precision.
What Free DFA Services Do We Offer at Omini?
At Omini, we provide comprehensive DFA (Design for Assembly) services to ensure that your PCB designs are optimized for efficient and high-quality assembly. Our free DFA services include thorough checks and suggestions in key areas to streamline production and minimize issues during the assembly phase. Here are the primary aspects of our DFA services:
1. PCB DFM (Design for Manufacturing) Check
Before starting production, Omini conducts an in-depth DFM (Design for Manufacturing) review to ensure your PCB design is ready for efficient manufacturing. This includes a file check across the following areas:
• Material Selection: Ensuring the materials are suitable for your design and manufacturing needs.
• Stack-up Design: Verifying that the stack-up configuration is optimized for performance and manufacturability.
• PCB Panel Design: Reviewing panelization for effective production and assembly.
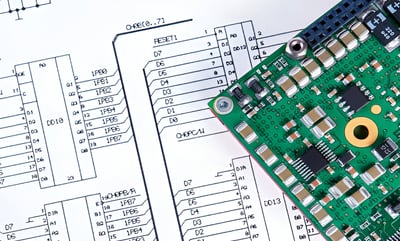
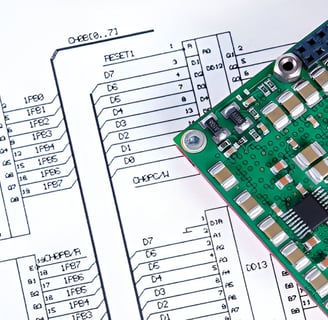
• Holes (PTH, NPTH): Ensuring proper placement and size for PTH (Plated Through-Hole) and NPTH (Non-Plated Through-Hole).
• Tooling Holes & Mounting Holes: Checking the placement of tooling and mounting holes to ensure they don’t interfere with other components.
• Fiducial Marks: Ensuring that fiducial marks are correctly placed and free from solder mask for accurate alignment.
• Solder Side Clearance: Verifying sufficient clearance on the solder side for reliable soldering.
• Component Clearance: Ensuring adequate space for component placement to avoid mechanical interference.
• Copper Connections: Checking copper traces and connections for proper design and manufacturing compatibility.
• Solder Mask Color: Confirming that the solder mask color meets your specifications.
• Silkscreen Quality: Verifying that silkscreen markings are clear, readable, and correctly placed.
• UL Logo/PCB Vendor Information: Ensuring proper certification marks (e.g., UL logo) and vendor details are included.
• Surface Finishes: Advising on appropriate surface finishes based on your design requirements.
2. BOM (Bill of Materials) Check
At Omini, we also conduct a BOM (Bill of Materials) check to ensure that all components are compatible with your PCB design and meet the necessary quality standards. We look for common issues, such as:
• Mismatch Between Parts and Pads: If parts listed on the BOM do not fit the pad or drill design on the PCB, we will consult with the customer and suggest the correct part number if necessary.
• Unclear or Incomplete Part Numbers: If the part numbers on the BOM are unclear or incomplete, we will work with the customer to clarify and ensure the correct parts are used.
3. Alternative Parts Advice
Sometimes, parts may be obsolete or have very long lead times, which can delay production. Omini will suggest suitable alternatives to ensure your project stays on track. We only use these alternatives in production with the customer’s approval to ensure you’re satisfied with the solution.
At Omini, our free DFA services are designed to ensure that your PCB designs are optimized for efficient manufacturing and assembly. By addressing potential issues early in the process, we help reduce the risk of delays, errors, and increased costs, ultimately ensuring a smoother production process.
Contacts
Email: sales@ominipcba.com
Mobile: +86-185-7640-5228
Copyright © 2007-2025. Omini Electronics Limited. All rights reserved.
Head Office: +86-755-2357-1819
Products & Services
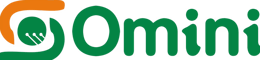
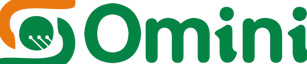
Office Address: No. 605, Tongxin Technology Building, Bao’an Avenue, Bao’an District, Shenzhen, Guangdong, China.
SMT Plant: A Building, Longwangmiao Industrial Park, Baishixia Community, Fuyong Street, Bao'an District, Shenzhen, China.
Omini Electronics Limited is an expert in trusted PCB Fabricaton and PCB Assembly in China since 2007. We have served over 1000 global customers with high-quality, low to medium-volume production. Certified by UL (E532498), ISO9001:2015, and ISO13485:2016, we offer expert electronics manufacturing services, including PCB manufacturing, assembly, and contract manufacturing, ensuring top-tier quality and precision in every project.