Phone: +86-755-2357-1819 Mobile: +86-185-7640-5228 Email: sales@ominipcba.com whatsapp: +8618576405228
Omini BGA Assembly
Miniaturization drives the electronics industry, with devices shrinking while functionality grows. Omini supports this trend with advanced solutions like BGA and Micro-BGA assemblies, offering higher I/O counts and performance in compact designs. This shift enhances component density, exemplified by the evolution of smartphones from bulky to sleek, powerful, and multifunctional.
BGA and Micro-BGA Assembly
SMT + PTH + Manual Assembly
PCB Manufacturing & Electronic Component Sourcing
ISO9001:2015, ISO 13485:2016, Certified & UL Listed
IPC-A-610 Class 2 & 3 Standards
100% E-Test, AOI, In-Circuit Test, and Functional Test
High-Density Interconnect (HDI) Technology
Advanced Package Testing & Inspection
Custom PCB Design & Engineering Support
Flexible Volume Production (Prototype to Full-Scale)
Lead-Free Soldering & RoHS Compliance
Quick Turnaround & On-Time Delivery
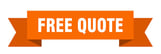
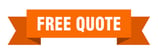
What is BGA Assembly?
Omini specializes in high-quality BGA assembly for printed circuit boards (PCBs). BGA assembly is a specialized process within Surface Mount Technology (SMT), where Ball Grid Array (BGA) chips are mounted onto PCBs. The process involves accurately soldering the chip’s small solder balls to the corresponding pads on the PCB, requiring precise pick-and-place machines and skilled technicians to ensure the highest quality.
Before understanding BGA assembly, it’s important to know what BGA is. BGA stands for “Ball Grid Array,” a type of semiconductor packaging where connection points are solder balls arranged in a grid pattern, rather than traditional leads. The chip is attached to a substrate, usually wire-bonded to the contact pads. The BGA package is then mounted onto the PCB using the SMT (Surface Mount Technology) process.
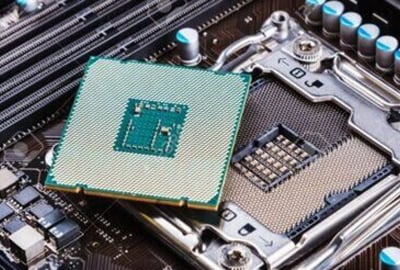
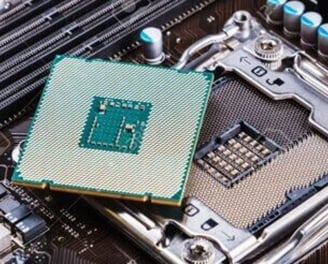
Types of BGA Assembly
• Plastic Ball Grid Array (PBGA): Featuring a glass-reinforced epoxy carrier, PBGA has the die mounted on the epoxy laminate. This type of BGA is known as “plastic” due to its epoxy substrate, with wire bonding used for the first-level connection. Copper tracks connect the chip to the PCB pads using the ball grid array for the second-level connection.
• Ceramic Ball Grid Array (CBGA): CBGA uses a ceramic substrate instead of epoxy, offering better hermetic sealing, making it ideal for more demanding environments.
• Tape Ball Grid Array (TBGA): TBGA features a flexible polyimide substrate with high-temperature-resistant solder balls. Copper stiffeners are often bonded to the substrate for added structural integrity.
Main Advantages of BGA PCB Assembly
Omini offers high-performance BGA PCB assembly with several key advantages, making it an ideal choice for advanced electronic applications:
1. Superior Thermal Dissipation
BGA packages provide excellent thermal management by efficiently conducting heat away from the chip and distributing it across the PCB. This helps prevent overheating and ensures the longevity and reliability of the components.
2. Higher Package Density
By replacing traditional lead frames with solder balls, BGA assembly increases I/O connectivity and reduces the overall package size. This optimization allows for more efficient use of board space, which is crucial for compact, high-density designs.
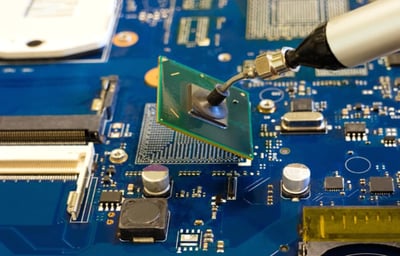
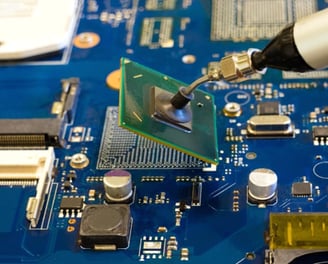
3. Low Inductance
The use of solder balls instead of leads minimizes signal distortion, especially in high-frequency applications. This offers significant electrical advantages over traditional leaded packages, ensuring more stable and reliable signal transmission.
Key Processes in BGA Assembly
Omini provides high-precision BGA PCB assembly services, ensuring top-tier performance for all your electronic needs. The BGA assembly process is intricate and demands advanced equipment along with skilled professionals. Below are the essential steps in BGA PCB assembly:
1. Solder Paste Application
The first step in BGA assembly is applying solder paste to the PCB. This involves printing a precise amount of paste onto the board, controlled through optimized stencil apertures and solder printing parameters. Due to strict environmental regulations, lead-free solder, such as SAC305, is now commonly used for improved transfer efficiency. The PCB should be coated with Organic Solderability Preservative (OSP) and have the appropriate surface finishes for robust assembly. BGA components use two types of pad designs:
• Solder Mask Defined (SMD): In this design, the copper pad is larger than the solder mask opening, offering excellent adhesion and better resistance to bending and temperature changes, although the pad is smaller for the BGA solder ball.
• Non-Solder Mask Defined (NSMD): The solder mask opening is larger than the copper pad, creating a gap or trench in the cross-section, exposing the entire copper pad.
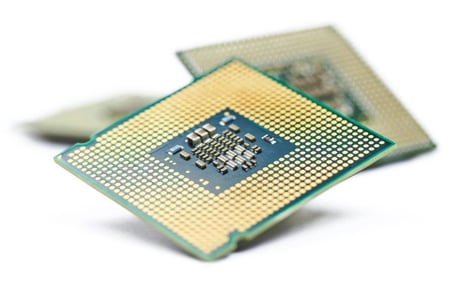
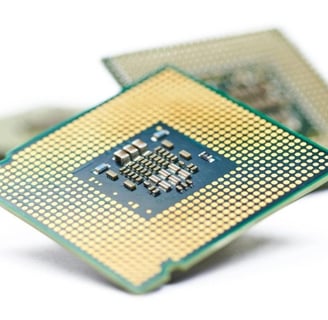
2. BGA Placement
Omini uses automated pick-and-place technology to precisely position BGA components. The BGA is picked up by a nozzle and placed onto the PCB using a vision system that ensures accurate alignment. This self-alignment feature during reflow soldering helps compensate for minor placement errors, ensuring precise positioning of even the smallest BGA components.
3. Reflow Soldering
Reflow soldering is a critical process in BGA assembly, where a carefully controlled thermal profile is used to melt solder paste and create strong, reliable connections. The process involves ramping up the temperature, activating flux, reaching a peak temperature, and cooling. Common issues like solder bridging, voiding, and poor wetting are closely monitored during reflow to ensure high-quality joints. Understanding the thermal properties of the copper pad, PCB, solder material, and BGA component is crucial to avoiding defects.
4. Underfill Dispensing
For fine-pitched BGA devices, underfill dispensing enhances reliability by filling the space between the BGA component and the PCB. This layer improves board-level reliability, especially under thermal and mechanical stress. The underfill material used must have the right viscosity, a low coefficient of thermal expansion, and a high glass transition temperature.
5. Quality Inspection
Omini employs Automated Optical Inspection (AOI) to detect faults in BGA assembly. AOI ensures accurate BGA positioning with optimized lighting and resolution. Additionally, X-ray inspection is conducted to verify solder coverage and detect any voids in the solder joints. This inspection method scans X-ray images to measure void percentages and assess the quality of the BGA solder joints.
Applications of BGA Assembly
Omini specializes in BGA PCB assembly, which is widely used across various industries due to its superior performance and reliability. Below are some key applications of BGA assembly:
• Automotive: BGA assembly offers higher package density, enabling the integration of more functions into a single board. In the automotive sector, this is essential for devices like navigation systems, instrument clusters, and other in-car electronics that require compact designs and enhanced performance.
• Aerospace: BGA PCBs are ideal for aerospace applications due to their excellent heat dissipation properties. Aerospace equipment must endure rigorous thermal cycles, and BGA’s efficient heat management ensures reliable operation in dynamic environments.
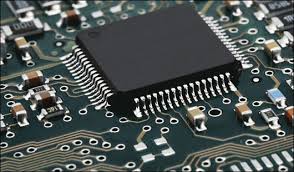

• Industrial Equipment: In industrial settings, where high thermal stability is crucial, BGA assembly is used in control systems, motor drives, and instruments. Its ability to withstand thermal and mechanical stress makes it an ideal choice for demanding industrial applications.
• Consumer Electronics: Everyday devices such as computers, smartphones, and other mobile gadgets benefit from BGA assembly. The compact design and superior heat dissipation properties of BGA packages contribute to the slim profile, lightweight design, and enhanced performance of modern electronics.
Why Choose Omini as Your BGA Assembly Supplier?
Omini stands out as a trusted BGA PCB assembly supplier, offering efficient and cost-effective solutions for your manufacturing needs. With extensive experience in the PCB industry, Omini delivers exceptional service and quality that sets us apart from other suppliers.
1. Quality Assurance
As BGA components continue to shrink and become more fine-pitched, quality becomes even more critical. Omini adheres to strict assembly procedures, ensuring compliance with international standards such as IPC, ISO, and UL. Unlike other suppliers who focus solely on high-volume orders, Omini has no minimum order requirements and guarantees that every order meets our high-quality standards.
2. Competitive Pricing
Pricing is always a key factor when choosing a supplier. Omini offers flexible and competitive quotes tailored to your needs, ensuring that you receive the most cost-effective solution for your project. We provide transparent pricing with no hidden costs, allowing you to make informed decisions.
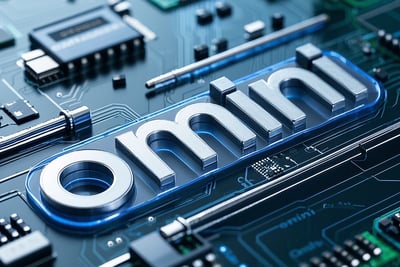
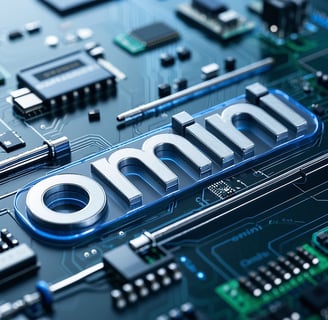
3. Fast Lead Times & On-Time Delivery
Timely delivery is crucial in BGA assembly. Omini boasts an impressive on-time delivery rate of over 98%, ensuring that your orders are delivered promptly and reliably, every time. We understand the importance of meeting deadlines and strive to exceed your expectations.
4. Advanced Technical Capability
Successful BGA assembly requires advanced equipment and a skilled team. Omini stays at the forefront of industry developments by introducing cutting-edge technology and continuously improving our capabilities. Whether you need complex PCB manufacturing or precision BGA assembly, Omini has the expertise to handle all your requirements.
Contacts
Email: sales@ominipcba.com
Mobile: +86-185-7640-5228
Copyright © 2007-2025. Omini Electronics Limited. All rights reserved.
Head Office: +86-755-2357-1819
Products & Services
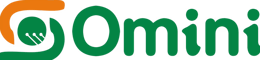
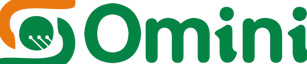
Office Address: No. 605, Tongxin Technology Building, Bao’an Avenue, Bao’an District, Shenzhen, Guangdong, China.
SMT Plant: A Building, Longwangmiao Industrial Park, Baishixia Community, Fuyong Street, Bao'an District, Shenzhen, China.
Omini Electronics Limited is an expert in trusted PCB Fabricaton and PCB Assembly in China since 2007. We have served over 1000 global customers with high-quality, low to medium-volume production. Certified by UL (E532498), ISO9001:2015, and ISO13485:2016, we offer expert electronics manufacturing services, including PCB manufacturing, assembly, and contract manufacturing, ensuring top-tier quality and precision in every project.