Phone: +86-755-2357-1819 Mobile: +86-185-7640-5228 Email: sales@ominipcba.com whatsapp: +8618576405228
Rigid PCB Solutions by Omini
At Omini, we specialize in providing high-quality rigid PCBs with competitive pricing, ideal for a wide range of electronic applications. Our rigid PCB solutions are designed to meet the demands of modern, high-performance electronics.
1-40 Layers for Mass Production & 100 Layers for Prototypes: We provide rigid PCBs with 1-40 layers for mass production and up to 100 layers for prototypes.
Materials: FR4, High-Speed, Microwave & RF, Metcal Core, Ceramic, PTFE: Our PCBs are made from FR4, high-speed materials, microwave & RF, Metcal core, ceramic, and PTFE.
Blind & Buried Vias, Stacked & Staggered Vias, Any-Layer HDI: We offer blind/buried vias, stacked/staggered vias, and any-layer HDI for high-density interconnects.
Conductive & Non-Conductive Via Plugging: Omini provides both conductive and non-conductive via plugging for enhanced PCB reliability.
Back Drill, Backplane, Embedded Devices, IC Substrate: We specialize in back drilling, backplane design, embedded devices, and IC substrates.
ISO9001:2015 Certified & UL Listed: Omini is ISO9001:2015 certified and UL listed, ensuring top-quality standards.
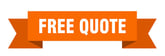
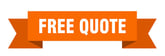
What is Rigid PCB?
A rigid PCB is a printed circuit board made from a solid substrate material that cannot bend or deform after manufacturing. It is a traditional PCB widely used across industries, including automotive, commercial, and industrial fields.
1. Material Composition of Rigid PCBs
The most common substrate for rigid PCBs is FR4, a flame-retardant epoxy woven fiberglass, known for its hardness, good dielectric properties, and excellent thermal stability. The choice of laminate material depends on the specific requirements of the application, such as thermal expansion or dielectric constant.
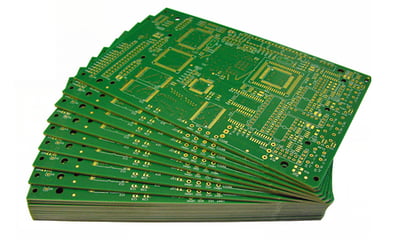
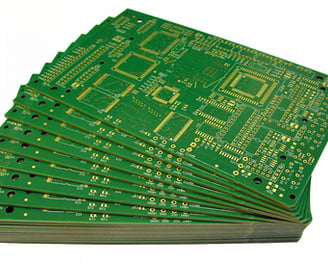
2. Structure of Rigid PCB
Rigid PCBs typically consist of three main layers:
• Insulating Substrate: The base material, often FR4.
• Copper Layer: The conductive portion that is etched to create the circuitry.
• Photoresist Layer: A protective layer over the copper, ensuring durability and preventing damage during manufacturing.
3. Rigid PCB Layer Types
Rigid PCBs can be classified into three main types based on the number of layers:
• Single-Sided PCBs
• Double-Sided PCBs
• Multi-Layer PCBs
The number of layers directly affects the functionality and complexity of the PCB.
At Omini, we provide high-quality rigid PCBs tailored to meet the demands of modern electronics, ensuring optimal performance for various applications. Whether for automotive, industrial, or commercial use, our rigid PCBs are designed for durability and reliability.
What are the Benefits of Rigid PCBs?
Rigid PCBs offer distinct advantages over flexible PCBs, making them the preferred choice for many applications. Omini manufactures high-quality rigid PCBs, providing the ideal solution for projects that require durability, mechanical strength, and high functionality.
1. Higher Functionality
Rigid PCBs support multi-layer construction and dense connections, which increases the functionality and design flexibility of your PCB. This makes them ideal for complex and high-performance applications.
2. Manufacturing Efficiency
As the earliest PCB technology, rigid PCBs benefit from mature, automated, and standardized manufacturing processes. This ensures fast production times and cost efficiency for large-scale manufacturing.
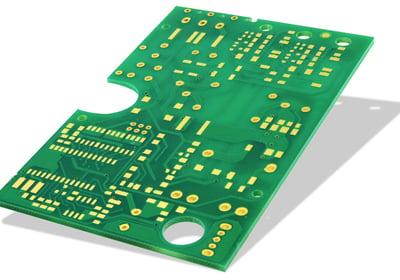
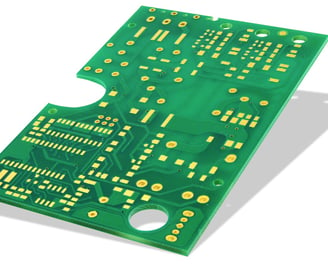
3. High Reliability
Rigid PCBs are known for their durability and resistance to deformation. Due to their structural rigidity, they provide superior reliability in demanding environments, making them the preferred choice for most industrial applications.
At Omini, we specialize in providing reliable, high-performance rigid PCBs designed to meet the diverse needs of modern electronics.
What are the Applications of Rigid PCBs?
Rigid PCBs are widely used across multiple industries due to their durability, reliability, and high-performance capabilities. Omini offers high-quality rigid PCBs that serve a broad range of applications, including consumer electronics, automotive, medical devices, and more.
1. Consumer Electronics
Rigid PCBs are commonly used in consumer electronics, such as computer motherboards and storage devices, where reliability and performance are critical.
2. Automotive Electronics
In the automotive industry, rigid PCBs play a crucial role in vehicles’ infotainment systems, enhancing the performance of in-car electronics.
3. Communication Technologies
Rigid PCBs are essential in communication technologies, including satellite systems, radio, and antennas, ensuring high-quality signal transmission.
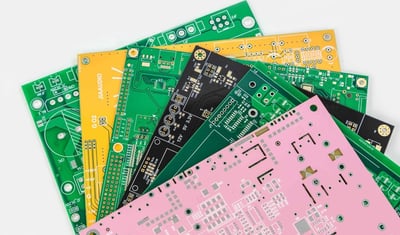
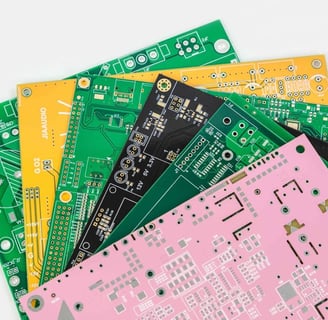
4. Mobile Phones
Rigid PCBs are widely used in mobile phones, supporting the complex circuits required for modern smartphones.
5. Medical Equipment
The medical field relies on rigid PCBs for various equipment, providing stability and precision in devices like diagnostic machines and monitoring systems.
6. Industrial Electronics
Omini manufactures rigid PCBs for industrial electronics, including control systems and instrumentation, ensuring reliable operation in harsh environments.
At Omini, we specialize in providing rigid PCBs for a wide range of applications, ensuring the highest quality and performance for each project.
How to Fabricate Rigid PCBs?
Fabricating a rigid PCB involves several precise and carefully controlled steps. Omini specializes in delivering high-quality rigid PCBs, ensuring excellent performance and durability across various industries. Here’s an overview of the fabrication process:
1. Schematic Diagram and PCB Layout
The process begins with creating a schematic design in CAD software, which maps out the components and connections of the PCB. The PCB layout then defines the physical arrangement of the circuit board, ensuring an efficient and functional design.
2. Lamination
In the lamination process, prepreg sheets are layered with copper foil under heat and pressure. The resin in the prepreg sheets cures under the applied heat, bonding the copper layers. This step is crucial for forming the rigid structure of the PCB.
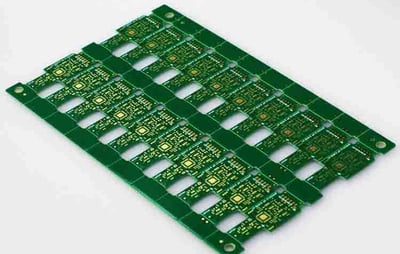
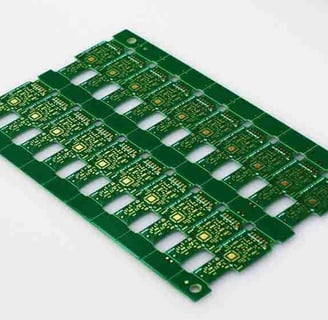
3. Photoresist Application
A photoresist layer is applied to protect the copper from oxidation. A positive resist is commonly used, where the exposed areas become soluble in the developer, allowing the unexposed copper to be etched away in later stages.
4. Etching Process
During etching, unwanted copper is removed using etchants like iron chloride or ammonium chloride. The process must be tightly controlled to ensure precise copper patterns for the circuitry, followed by a rinsing step to remove the photoresist.
5. Drilling
Using computer-controlled drilling machines, holes and vias are precisely created. For miniaturized components, smaller drills are required. Drilling methods may include laser, micro-drilling, and micromachining, with fibreglass PCBs often drilled using diamond or tungsten carbide tips.
6. Solder Masking
A solder mask, or “solder resist,” is applied to the board to isolate the conductive and insulative areas. This protective coating prevents solder from bridging between traces. The solder mask is applied using photolithography or silk-screening techniques, depending on the complexity.
7. Surface Finish
To prevent oxidation, the exposed copper pads undergo a surface finish. This ensures reliable soldering of components. Popular surface finishes include HASL (Hot Air Solder Leveling) and ENIG (Electroless Nickel Immersion Gold), both providing excellent electrical connectivity.
8. Silkscreen
Silkscreen printing is used to apply identification marks, logos, component codes, and other important labels to the PCB. This can be done using traditional stencil printing or more advanced methods like Liquid Photo Imaging (LPI) for high-density designs.
At Omini, we ensure that each step in the rigid PCB fabrication process is meticulously executed to deliver high-quality, reliable boards suitable for demanding applications.
Why Choose Omini as Your Rigid PCB Partner?
When it comes to selecting the right partner for your rigid PCB needs, Omini offers unmatched expertise and capability in delivering high-quality PCBs. Here’s why we are the ideal choice for your next project:
1. Diversified Capabilities
Omini specializes in a wide range of rigid PCB solutions, from simple single-layer boards to complex 100-layer HDI PCBs. Whether you need standard designs or advanced technologies with complex vias and fine lines, we can meet all your requirements.
2. Competitive Pricing
We offer competitive pricing with flexible options tailored to your needs. Once you share your technical specifications, Omini can provide an immediate and accurate quotation, ensuring that you get the best value for your investment.
3. High Quality
At Omini, quality is at the core of everything we do. We produce high-quality rigid PCBs that meet all specifications, with a focus on zero defects and continuous improvement. Our production adheres to strict quality management systems such as ISO9001, ISO13485, and TS16949.
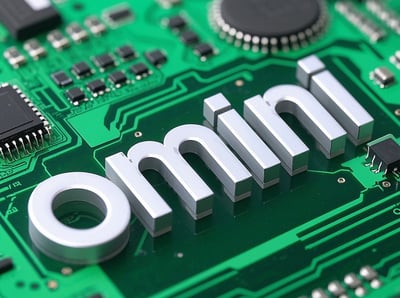
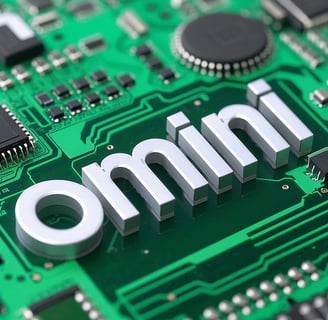
4. Perfect Customer Service
We believe open communication and collaboration are key to successful partnerships. Omini treats our customers as partners, aligning our goals with yours to ensure we deliver on our commitments, with a strong focus on your needs and requests.
5. Fast Delivery
Omini is known for meeting tight delivery schedules. We offer fast turnaround times and expedited options, ensuring that your rigid PCBs are delivered on time, every time.
Choose Omini for your rigid PCB needs and experience the difference in quality, reliability, and customer service.
Contacts
Email: sales@ominipcba.com
Mobile: +86-185-7640-5228
Copyright © 2007-2025. Omini Electronics Limited. All rights reserved.
Head Office: +86-755-2357-1819
Products & Services
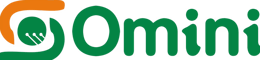
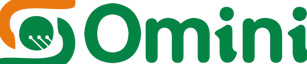
Office Address: No. 605, Tongxin Technology Building, Bao’an Avenue, Bao’an District, Shenzhen, Guangdong, China.
SMT Plant: A Building, Longwangmiao Industrial Park, Baishixia Community, Fuyong Street, Bao'an District, Shenzhen, China.
Omini Electronics Limited is an expert in trusted PCB Fabricaton and PCB Assembly in China since 2007. We have served over 1000 global customers with high-quality, low to medium-volume production. Certified by UL (E532498), ISO9001:2015, and ISO13485:2016, we offer expert electronics manufacturing services, including PCB manufacturing, assembly, and contract manufacturing, ensuring top-tier quality and precision in every project.