Phone: +86-755-2357-1819 Mobile: +86-185-7640-5228 Email: sales@ominipcba.com whatsapp: +8618576405228
PCBA Testing
When it comes to high-quality PCB assembly, Omini offers a full range of services to meet all your testing needs, ensuring top performance and reliability.
PCB Fabrication, Component Sourcing & PCB Assembly: We provide end-to-end solutions for efficient PCB production, from design to assembly.
Box Build Assembly & System Integration: Omini specializes in complete box build assembly and system integration for your electronic products.
E-Test, ICT Test, Functional Test & Burn-in Test: We offer a wide range of tests, including E-Test, ICT, functional testing, and burn-in tests to ensure your PCB’s performance.
Reliability Test & Environmental Test: Our extensive reliability and environmental testing ensure that your PCB assembly meets industry standards.
Small to Medium Volume Production: Whether you need small or medium volume runs, Omini guarantees quick turnarounds and competitive pricing.
ISO9001:2015, ISO 13485:2016 Certified & UL Listed: We maintain strict quality control through our ISO certifications and UL listing, ensuring top-quality products.
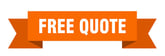
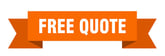
What is PCBA Testing?
PCBA (Printed Circuit Board Assembly) testing is a critical step in ensuring the quality and reliability of PCBs. Omini, a leader in PCB assembly solutions, provides comprehensive testing to ensure that every PCB meets industry standards and customer expectations. Below is an overview of PCBA testing processes:
1. Understanding PCBA Testing
PCBA testing refers to the process of verifying the electrical and physical functionality of a printed circuit board assembly. This includes testing the mounted electronic components and ensuring that the input and output values align with specifications. At Omini, we integrate advanced testing tools to ensure high-quality production.
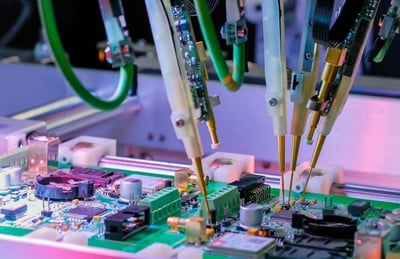
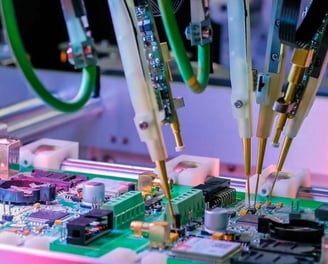
2. Importance of Functional Testing
Functional testing evaluates both individual components and the entire PCB operation. This test simulates real-world conditions, ensuring that the assembly functions correctly before shipment. Omini guarantees that 100% of PCBs undergo functional testing to meet stringent quality standards.
3. Online Testing for Enhanced Quality Control
Online testing checks whether the PCB meets design requirements during the SMT and DIP processes. This ensures that the final product is in line with electrical and mechanical standards. Omini leverages this testing method to prevent defects and ensure process compliance.
4. Ensuring Brand Reputation with Quality Testing
To protect your brand and reputation, PCBA testing is essential. Poor quality products can harm your brand’s credibility. Omini emphasizes functional testing to ensure that each PCB meets the highest standards before being shipped to Original Equipment Manufacturers (OEMs) or Electronics Contract Manufacturers (ECMs).
5. The Role of PCBA Testing in Production
PCBA testing is not just a post-production step but a continuous process integrated into production. It’s a key part of Omini’s commitment to delivering high-quality, reliable PCBs that meet global industry standards, including RoHS and ISO certifications.
By using Omini’s PCB assembly services, you can be confident that your products undergo thorough testing, ensuring both functionality and durability for a range of applications.
Types of PCBA Testing
The PCB assembly process is highly intricate, involving various critical steps such as part procurement, SMT (Surface Mount Technology) assembly, DIP (Dual In-line Package) plug-ins, and extensive testing. Among these, PCBA testing is one of the most vital aspects, as it ensures the final product’s functionality, quality, and compliance with required standards. Omini is committed to maintaining high standards of quality through rigorous testing of every PCB assembly, helping clients achieve reliable and efficient products. Below are the key types of PCBA testing that are essential for ensuring superior quality:
1. ICT (In-Circuit Testing)
This test checks the individual circuits on the PCB for open or short circuits and verifies voltage, current, and other electrical properties. ICT ensures that each component functions correctly before moving on to the next phase of assembly.
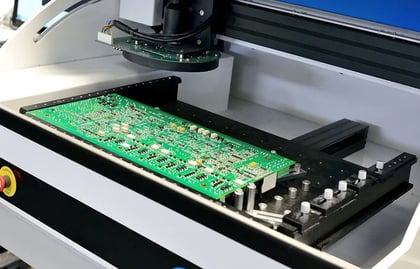
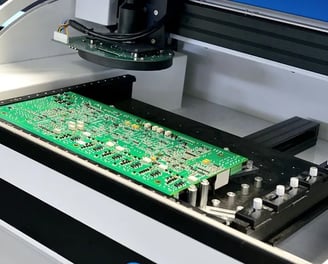
2. FCT (Functional Testing):
The FCT tests the overall functionality of the PCB by simulating real-world conditions. This test examines the interaction between hardware and software systems and ensures that the entire PCB operates as intended. It also involves burn-in testing, where the PCB undergoes prolonged use to detect potential failures.
3. Aging Test:
This test involves running the PCBA board and its electronic components for extended periods to identify any failures over time. The aging test ensures that the product can withstand continuous operation, and once it passes, it is considered ready for batch production.
4. Fatigue Test:
The fatigue test simulates long-term usage by subjecting the PCB assembly to high-frequency operations. This test evaluates the likelihood of component failure under stress and provides valuable data on the longevity and reliability of the product.
5. Harsh Environment Testing:
This test exposes the PCBA to extreme environmental conditions such as high and low temperatures, humidity, drops, splashes, and vibrations. It ensures that the PCB performs reliably under adverse conditions, providing insights into the overall durability of the product.
6. Reliability and Performance Testing:
Omini places significant emphasis on continuous reliability and performance testing throughout the production process. This includes various real-time assessments to ensure that the PCBA meets both functional and durability standards over time.
Why is PCBA Testing Necessary for Your Business?
At Omini, we understand that PCBA testing is essential for ensuring the reliability and quality of your products. The testing process not only guarantees the performance of your printed circuit boards (PCBs) but also directly impacts the overall success of your business. Below are key reasons why PCBA testing is critical:
1. Improves Assembly Capability
A higher pass rate in electronic PCB assembly testing leads to a higher pass rate for the final products. This directly improves the overall quality of your products, enhances manufacturing efficiency, and boosts the assembly capabilities of your company.
2. Enhances Economic Advantages
Only products that pass rigorous PCBA tests will satisfy customer expectations and perform well in the market. During the testing phase, any errors or issues can be identified and corrected, ensuring that your product meets industry standards. This proactive approach helps products gain customer trust and favor, ultimately driving the economic growth of your business.
By implementing thorough PCBA testing processes, Omini helps businesses ensure that every product leaving the assembly line meets the highest quality standards, thereby promoting growth, profitability, and long-term success.
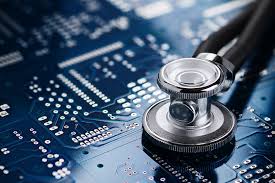
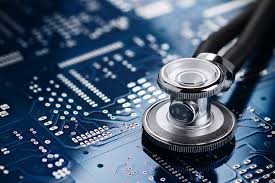
Benefits of PCBA Testing for Your Business
Omini recognizes that PCBA testing is a crucial step in ensuring the quality and performance of your products. Proper testing helps to identify potential issues early, leading to improved product quality, customer satisfaction, and sales growth. Below are the key benefits of circuit card assembly testing:
1. Enhances Product Quality
Printed circuit board testing plays a vital role in improving the qualification rate of your products. By thoroughly testing each PCB assembly, you ensure that only high-quality products reach the market, enhancing overall product performance and reliability.
2. Increases Customer Satisfaction
PCB board testing is instrumental in enhancing customer satisfaction. Through rigorous testing, Omini helps identify and eliminate defective products before they reach consumers, preventing quality issues and ensuring that only the best products are delivered to the market.


3. Boosts Sales Performance
Electronics assembly testing directly contributes to better sales performance. High-quality, reliable products build a strong reputation, helping to expand market share and increase sales. As customers experience superior product quality, brand loyalty and sales figures grow.
By investing in comprehensive PCBA testing, Omini ensures that your products meet industry standards and exceed customer expectations, driving growth and success in the competitive PCB market.
The Methods to Test PCBA
Omini recognizes the importance of precise PCBA testing methods to ensure the reliability and quality of printed circuit board assemblies. Below are some common methods used in PCBA testing:
1. Manual Testing
Manual testing relies on direct visual inspection and is widely used, but it has significant limitations. As the complexity of the boards increases, this method becomes less effective at detecting hidden defects. Moreover, classifying various types of defects manually is time-consuming and prone to human error. While this method is inexpensive, it is becoming less suitable for modern, high-volume production.
2. Automatic Optical Inspection (AOI)
Omini employs Automatic Optical Inspection (AOI), which provides more accurate and efficient testing by using high-resolution cameras to inspect solder joints, components, and overall board quality. AOI excels in identifying polarity issues, component misalignment, and other visual defects. However, it struggles with detecting certain types of hidden defects, such as those in multi-layer PCBs or intricate component connections.
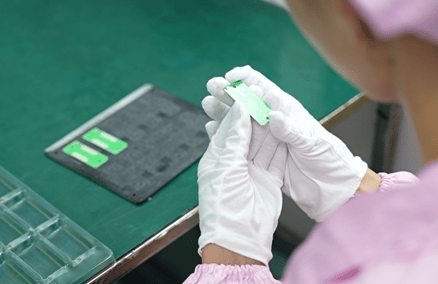
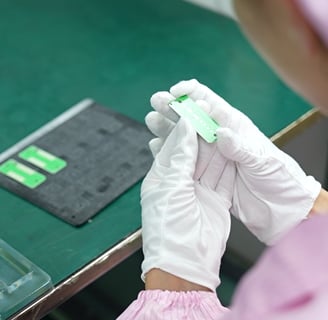
3. Flying Probe Testing
Flying probe testing is an advanced method that has gained popularity in recent years due to its speed, accuracy, and versatility. This method allows for testing without the need for fixtures, making it ideal for low-volume production and prototypes. Omini utilizes flying probe testing to ensure precise electrical testing of PCBs, as it can detect open circuits, shorts, and other faults with high accuracy. The ability to quickly switch between different test setups is a key advantage.
4. Functional Testing
Functional testing is essential for verifying the performance of a PCB after assembly. Omini applies functional testing to simulate real-world operating conditions and assess the PCB’s functionality. This method ensures that the assembled board meets all electrical and mechanical specifications. It requires specialized instrumentation and involves comprehensive end-product testing, including thermal simulations to check for potential failures under load.
5. Production Defect Analyzer (MDA)
The Production Defect Analyzer (MDA) is a cost-effective testing solution that is useful for high-throughput testing of basic circuit integrity. MDA helps identify issues such as open or short circuits and verifies the presence of all components. However, it does not test the functionality of the board or its components, limiting its use for more complex testing needs. Omini uses MDA as part of a comprehensive testing strategy to identify manufacturing defects early in the production process.
By utilizing a combination of these PCBA testing methods, Omini ensures the highest quality standards are met and that all printed circuit board assemblies are reliable, durable, and fully functional.
The Equipment for PCBA Testing
When it comes to testing soldered circuit boards, several common test instruments are essential for ensuring the quality and reliability of printed circuit boards. The equipment used in Omini’s PCB assembly testing process includes ICT online testers, FCT function tests, and aging tests, all of which play a crucial role in achieving the highest standards.
1. ICT Online Tester
The ICT (In-Circuit Testing) offers significant advantages such as broad application, ease of operation, and high efficiency. This test is essential for detecting open circuits, short circuits, and component damage. It can accurately locate faults, making repairs easier and more cost-effective. Omini utilizes ICT to ensure that each board meets the stringent quality standards.
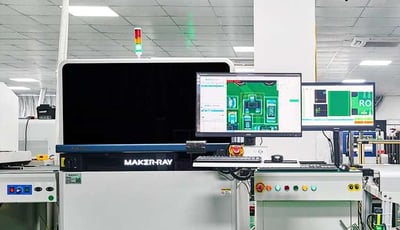

2. FCT Function Test
Once a PCB passes ICT, it moves to the FCT (Functional Testing) phase. This test evaluates the product’s functionality by simulating the actual operating environment. During this phase, Omini ensures that the printed circuit board operates within its design parameters. The function test is crucial for verifying that each component works properly and that the overall system performs as expected.
3. Aging Test
The Aging Test simulates real-world conditions by subjecting the circuit board to high and low temperatures, temperature cycling, and electrical stress. This helps identify any defects in the assembly process, such as poor soldering or mismatched component parameters. Omini uses this method to ensure that PCBs can withstand extended periods of use and meet consumer demand in terms of durability and performance.
These three essential tests—ICT, FCT, and aging—are key to the Omini PCB assembly process. By integrating these methods into our workflow, Omini ensures that all circuit boards meet rigorous quality standards, resulting in low maintenance rates and satisfied customers.
PCBA Test Fixture Classification
Omini understands the critical role that PCBA test fixtures play in ensuring the quality and reliability of your printed circuit board assemblies. Below are the common types of PCBA testing methods and the key aspects involved in their fixture design:
1. ICT Test (In-Circuit Testing)
The ICT test primarily focuses on evaluating the circuit’s on-off functionality, voltage and current values, fluctuation curves, amplitude, and noise levels. This test ensures that all components are properly connected and functioning as expected.
2. FCT Test (Functional Circuit Testing)
The FCT test simulates the full-function environment of a completed product. Its purpose is to detect any assembly defects before the circuit board is integrated into the final machine. By catching issues early, this test prevents waste and time loss associated with disassembly and reorganization.
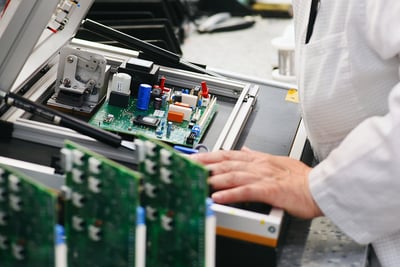
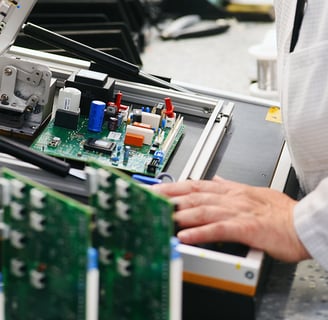
3. Fatigue Test
The fatigue test subjects PCB assemblies to high-frequency and long-term operational conditions to observe any potential faults or failures. This test provides valuable feedback on the operational characteristics of circuit assembly boards in electronic products, allowing Omini to make necessary adjustments before mass production.
4. Harsh Environment Test
The harsh environment test exposes the PCBA board to extreme conditions such as temperature variations, humidity, drops, splashes, and vibrations. The results of these tests on random samples help assess the overall reliability of the entire batch of PCB products.
5. Aging Test
The aging test powers the circuit board assembly and electronic products for extended periods to simulate real-world usage. This test helps identify potential failures over time, ensuring that products meet long-term reliability standards before being sold in batches.
Key Points in PCBA Test Fixture Creation
At Omini, we emphasize the importance of designing efficient and effective PCBA test fixtures to ensure accurate and reliable results. Key points in creating a test fixture include:
1. Fixture Design Based on Test Needs
The design of the test fixture should align with the specific testing requirements and the type of PCB being tested. It includes the design of the load plate, pressure plate, and instrumentation module.
2. Accurate Fixture Positioning
The fixture should be correctly positioned, and the connection of the instrumentation should be smooth for efficient testing.
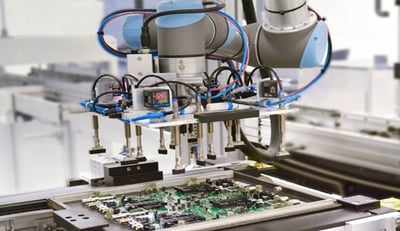
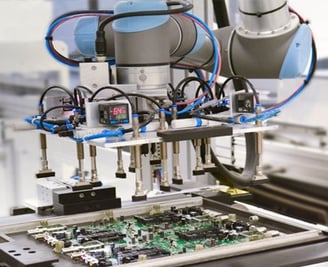
3. Efficient Fixture Box Layout
The test fixture box should be designed with ample space to accommodate the test product, ensuring a compact and organized layout for easy installation and access.
4. Reserved Interface Position
The test fixture must have correctly positioned and sufficient reserved interfaces, allowing for flexibility and easy adjustments.
5. Ease of Maintenance
The fixture box should include features such as a case buckle or pressing buckle, enabling easy replacement and maintenance of components.
6. Zero Calibration
Correct zero calibration is crucial as the test fixture’s zero drift can change with varying test conditions. Omini ensures that FCT test fixtures are equipped with electrical and tangency correction settings for precise measurements.
7. Fixture Durability and Maintenance
If the test fixture becomes damaged or the needle needs replacement, maintenance and repair are essential to ensure continued accuracy and reliability.
PCBA Test Fixture Production Process
The production process for PCBA test fixtures at Omini involves:
1. Design Selection
Based on the test needs and customer requirements, the final fixture design is chosen, with specific attention to pressure plates, load plates, and other essential components.
2. Correct Clamping Plate Position
The clamping or load plates must be positioned accurately to prevent damage during testing, ensuring smooth operation.
3. Fixture Layout
The test fixture should be designed with ample internal space, and the layout should facilitate easy installation and maintenance.
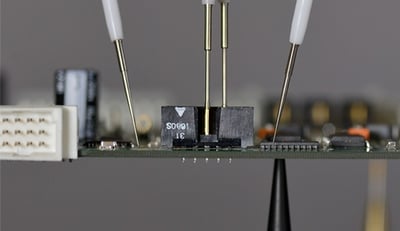
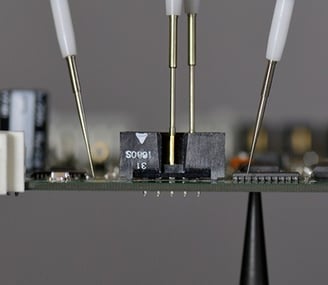
4. Accurate Reserved Interface Positioning
The test fixture should have sufficient and well-placed reserved interfaces to ensure compatibility and ease of use.
By focusing on these key aspects, Omini ensures that every PCBA test fixture is tailored for optimal performance, enhancing testing accuracy, and improving overall product quality.
What Will the PCBA Testing Consist of?
1. ICT Test (In-Circuit Testing)
The ICT test mainly involves checking circuit switching, current values, voltage, amplitude, noise, and other parameters to ensure that the PCB manufacturing and assembly process is functioning as expected. This test is crucial for verifying the integrity and performance of individual components in the PCB assembly.
2. FCT Test (Functional Testing)
The FCT test is designed to assess the entire functionality of the PCBA once the IC program has been integrated. This test verifies both the code and hardware, ensuring there are no issues. It includes the use of specific fixtures and test racks to simulate real-world conditions and confirm the functionality of the assembled PCB.
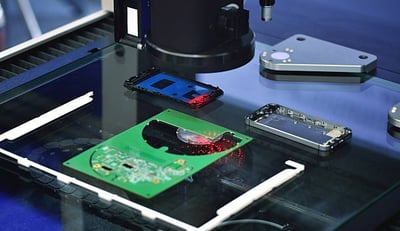
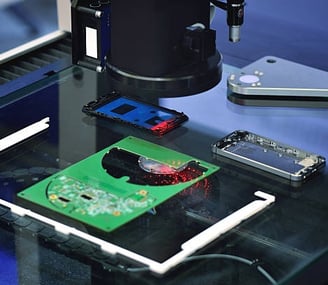
3. Fatigue Test
The fatigue test simulates the long-term operation of the PCB assembly by subjecting it to repeated cycles. For example, testing components like buttons or LEDs for thousands of cycles helps determine the likelihood of failure over time. This test ensures the durability and reliability of the PCBA under continuous use.
4. Harsh Environments Test
In this test, the PCBA is exposed to extreme conditions such as temperature variations, humidity, drops, splashes, and shocks. By testing under these harsh environments, random samples are assessed, and the overall reliability of the printed wiring assembly (PWA) is predicted for mass production.
5. Aging Test
The aging test involves powering the PCB assembly and electronic products for extended periods while maintaining operational states. This test identifies any potential faults and is crucial before products are released into the market. Only after passing this test can the product be deemed ready for mass production and sale.
Electronic PCB assembly test methods are sophisticated and integral to the production process. Without these tests, products may experience high failure rates and frequent repairs, which would harm the growth of enterprises. With Omini’s comprehensive testing services, businesses can quickly identify quality and performance issues, enabling timely adjustments to ensure product reliability and foster brand development.
What is the PCBA Test Rack?
The principle of the PCBA test rack is straightforward. It works by connecting metal probes to the solder pads or test points on the PCB. Once the PCB is powered, the test circuit’s standard values—such as voltage and current—are measured to check if the test circuit is functioning correctly.
PCBA test racks are typically custom-made according to the size of the PCB, the test purpose, and the required test values. Materials like acrylic, plastic, and metal probes are commonly used, and the racks are equipped with monitors and wires to facilitate the testing process.
The Usage of the PCBA Test Rack
1. PCB Assembly Testing in Custom Circuit Board Production
The PCBA test rack is essential throughout the entire custom circuit board assembly process. It is primarily used to test assembled circuit boards after the completion of the SMT (Surface-Mount Technology) and DIP (Dual In-line Package) components.
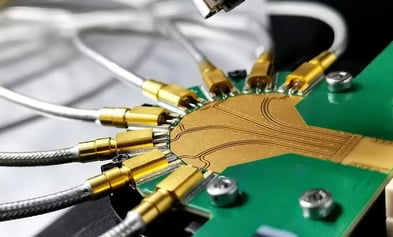
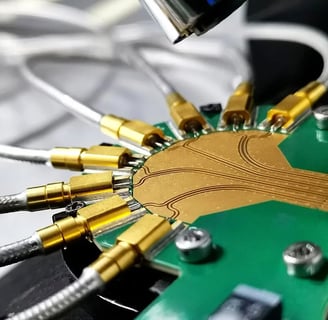
2. ICT Test for Conductivity
The ICT test is used to assess the conductivity of the circuit board by testing specific points. This ensures that the entire PCB is successfully soldered and free from defects.
3. Completion of Circuit Board Assembly Testing
The PCBA test rack plays a crucial role in completing the testing of circuit board assemblies, ensuring that the products meet the necessary quality standards.
4. Impact on Testing Efficiency and Pass Rates
The quality of the PCBA test rack directly influences the efficiency and pass-through rate of the ICT test. Due to the frequent operation of these racks, manufacturers, including Omini, prioritize the production quality to ensure reliability and durability.
Further Understanding of PCBA Testing
1. PCBA Functional Test
FCT (Functional Test) refers to a method that simulates the operating environment (excitation and load) of a test target board (UUT: Unit Under Test). It ensures that the PCB works in various design states, obtaining the parameters to verify its functionality. Simply put, it loads the UUT with suitable excitation and measures whether the output response meets the required specifications.
Key Components of the PCBA Functional Test
• Power Supply Test: Tests the proper operation of the power supply and measures the voltage at each point to ensure proper power distribution across the board.
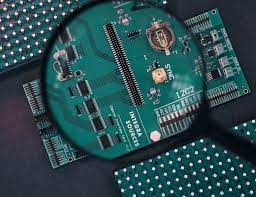
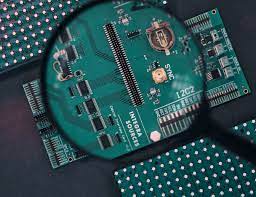
• Port (Interface) Test: Checks for short circuits or open circuits that could lead to dysfunction, ensuring that all connections are intact and working as expected.
• Special Function Testing: This varies depending on the specific board’s requirements. Each PCB design may have unique functions that need to be tested for proper operation.
Composition of the Functional Test System
• System Control Center: The control center is typically composed of a PC, MCU, ARM, or other processors. Its primary role is to control the test process, judge and record each step, and ultimately provide the final test results. It acts as the “brain” of the functional test system.
• Control and Execution: This part includes I/O components that act as the execution mechanism, creating various test environments and enabling test functions throughout the process.
• Parameter Measurement: This component, including measurement boards and instruments, collects various analog or digital quantities during the test. It is crucial for accurate data acquisition and monitoring throughout the testing process.
• Data Processing and Output: The processing and output of test results are essential for tracking and controlling the quality of PCBA products. The system stores and outputs these results, ensuring easy access for future quality control and performance assessment.
2. PCBA Electrical Characteristic Test
PCBA electrical characteristic tests are vital to ensure the functionality and reliability of circuit boards. Key aspects include:
• Current Test: Detects whether the circuit board experiences current exposure issues. The test passes if the current is within the acceptable range defined by the design specifications.
• Voltage Test: Tests the board’s voltage withstand capability by gradually increasing the voltage. If the circuit does not fail, the test passes.
• Impedance Test: Impedance testing is crucial to measure the resistance of components or circuits to current. Using an ohmmeter, the impedance is checked, and the test passes if the value is within the specified range.
3. Reliability Test
Tests such as ICT, FCT, aging, fatigue, and harsh environment tests fall under the umbrella of reliability testing. These tests ensure that PCBs, like those offered by Omini, perform reliably under various conditions, reducing failure rates and enhancing product durability.
PCBA Mechanical Characteristic Test by Omini
Omini specializes in delivering comprehensive PCBA mechanical characteristic tests to ensure the reliability and durability of your circuit boards. Below are the key tests offered by Omini to guarantee that your products meet the highest industry standards:
1. Pressure-Withstanding Test
The pressure-withstanding test is crucial to assess the board’s ability to endure pressure. This test is essential for ensuring that the board can perform under various stress conditions. The equipment required for this test is a pressure-withstanding tester.
2. Salt Mist Test
The salt mist test evaluates the circuit board’s corrosion resistance, simulating environmental factors that can impact product longevity. This test is performed using a salt spray tester, which exposes the board to saline conditions to measure its resistance to corrosion.
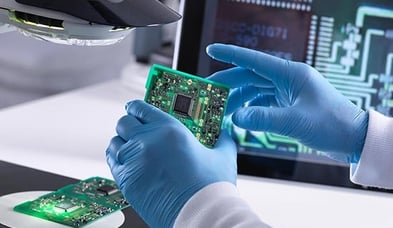
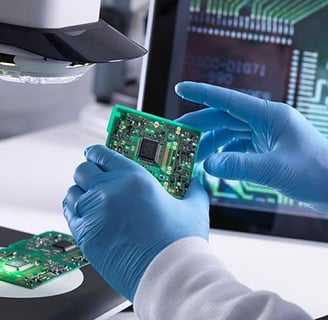
3. Vibration Test
The vibration test checks whether the circuit board can withstand different levels of random vibration, ensuring the board’s stability during transportation or operational environments. The equipment required for this test is a vibration meter.
4. High Temperature and Humidity Test
The high temperature and humidity test is designed to examine the board’s performance in extreme conditions. This test ensures the board can function effectively in high-temperature and high-humidity environments. It requires a constant temperature and humidity test chamber.
5. Solder Strength Thrust Test
The solder strength thrust test is performed to determine whether the solder strength of components meets the necessary requirements. This test uses a thrust meter to check the robustness of the solder joints on the PCB.
These mechanical tests are essential to validate the durability and reliability of PCBs in various operational environments. At Omini, we conduct these tests to help ensure your products are ready for real-world applications.
Choose Omini for PCBA Testing
As a trusted PCB manufacturing and assembly provider, Omini has always believed that PCBA testing is crucial to ensure product quality. It plays a key role in determining product performance, controlling quality, reducing after-sales issues and repair rates, boosting customer confidence, and fostering long-term, win-win partnerships between enterprises and customers. With a comprehensive procurement, production, and quality management system, Omini can quickly deliver cost-effective PCB assembly solutions. Additionally, Omini conducts a full range of testing for PCB assembly and soldering. We are the perfect choice for businesses seeking high-quality PCB assembly services, as demonstrated by the following advantages:
1. A Well-Experienced PCB Assembly Manufacturer
Omini has specialized in circuit board contract manufacturing for over 16 years. Equipped with advanced production equipment and a meticulous management system, we ensure superior PCB assembly services that meet the highest standards of quality and reliability.
2. A Well-Qualified PCBA Manufacturer
With the rapid growth of the internet and electronic component trading platforms, Omini stands out as a qualified and reliable electronic circuit assembly manufacturer. We hold certifications such as UL, ISO9001, RoHS/REACH, and more, which enhances customer trust and ensures that we deliver high-quality products. Our streamlined process allows dealers to quickly receive accurate quotations based on requirement documents, saving time and effort in sourcing components.
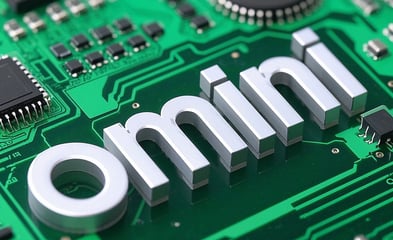
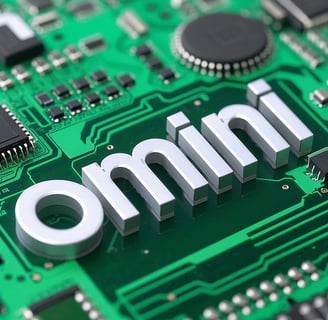
3. A Considerate Printed Circuit Board Assembly Service Provider
Omini focuses on improving the customer service experience by offering extensive expertise in pre-sales, sales, and after-sales support. We are always ready to assist with any questions and address customer concerns promptly. During prototyping and testing, we help identify design issues and suggest modifications. We are dedicated to solving technical challenges for our customers, ensuring they receive the best PCB assembly and soldering services.
Contacts
Email: sales@ominipcba.com
Mobile: +86-185-7640-5228
Copyright © 2007-2025. Omini Electronics Limited. All rights reserved.
Head Office: +86-755-2357-1819
Products & Services
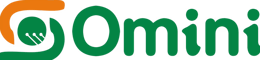
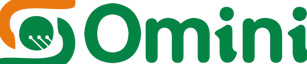
Office Address: No. 605, Tongxin Technology Building, Bao’an Avenue, Bao’an District, Shenzhen, Guangdong, China.
SMT Plant: A Building, Longwangmiao Industrial Park, Baishixia Community, Fuyong Street, Bao'an District, Shenzhen, China.
Omini Electronics Limited is an expert in trusted PCB Fabricaton and PCB Assembly in China since 2007. We have served over 1000 global customers with high-quality, low to medium-volume production. Certified by UL (E532498), ISO9001:2015, and ISO13485:2016, we offer expert electronics manufacturing services, including PCB manufacturing, assembly, and contract manufacturing, ensuring top-tier quality and precision in every project.