Phone: +86-755-2357-1819 Mobile: +86-185-7640-5228 Email: sales@ominipcba.com whatsapp: +8618576405228
PCB Manufacturing Tolerances
Omini offers high-precision PCB manufacturing services, ensuring that each Printed Circuit Board meets stringent tolerances for performance and reliability.
PCB tolerances define the allowable deviations in size, thickness, angle, and other parameters between the actual board and the customer’s design specifications.
Tighter tolerances can improve functionality but make the manufacturing process more difficult and reduce the yield rate, increasing production costs.
Application-specific tolerances: For critical industries like aerospace, Omini delivers ultra-precise PCBs that meet the strictest tolerance standards to ensure maximum reliability.
Industry-standard IPC-A-600 governs PCB tolerance requirements, and Omini adheres to these norms to guarantee that all products meet or exceed customer expectations.
By focusing on quality and precision, Omini ensures that every PCB meets the necessary tolerances for optimal performance in a variety of industries, from consumer electronics to advanced applications.
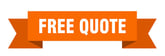
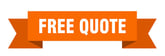
PCB Drilling Tolerances and Specifications by Omini
Omini provides precision drilling services for PCB manufacturing, ensuring each board adheres to industry standards and customer specifications. Below are the key drilling tolerances for Plated and Non-Plated Holes and Slots:
1. Plated Hole Size (PTH):
• ≤4.00mm tolerance: ±0.75mm (Best: ±0.05mm)
• 4.00mm tolerance: ±0.10mm
2. Non-Plated Hole Size (NPTH):
• ≤4.00mm tolerance: ±0.05mm
• 4.00mm tolerance: ±0.10mm
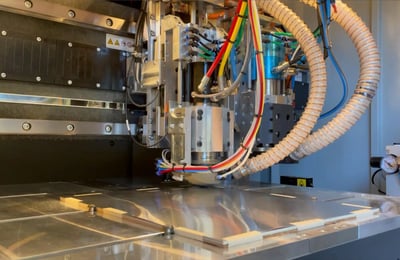
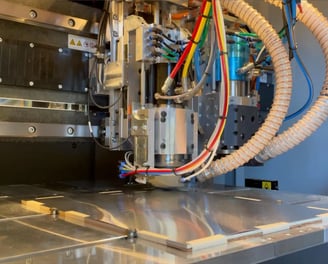
3. Plated Slot Size by Drill (PTH Slot):
• Tolerance: ±0.1mm (Best: ±0.75mm)
4. Non-Plated Slot Size by Drill (NPTH Slot):
• Tolerance: ±0.075mm (Best: ±0.05mm)
5. Hole Position and Other Drilling Specifications:
• Hole Position Tolerance: ±0.075mm
• Back Drill Depth: ±0.1mm
• Countersink Hole Angle: ±10°
• Countersink Hole Size: ±0.15mm
• Aspect Ratio: 1:18 (Drill size: PCB thickness)
Omini follows strict quality control measures to ensure precision in all drilling processes for both plated and non-plated holes, guaranteeing excellent performance across all applications.
Hole Wall Copper Tolerances at Omini
Omini ensures the highest standards of copper wall thickness for hole integrity, as defined by IPC-A-600.
1. Minimum Copper Thickness:
• 20μm for IPC-A-600 Class 2
• 25μm for IPC-A-600 Class 3
These precise tolerances help to ensure reliable electrical performance and longevity of your PCBs, making Omini your trusted partner in PCB manufacturing.
PCB Surface Finish Thickness Specifications by Omini
Omini offers a wide range of surface finishes for high-quality PCB manufacturing, ensuring reliable and durable performance for every application. Below are the surface finish thickness tolerances for various finishes:
1. HAL Lead-Free:
• Thickness: 2 – 40μm
• Ideal for environmentally friendly and cost-effective solutions.
2. Immersion Gold (ENIG):
• Nickel: 3 – 8μm
• Gold: 0.05 – 0.10μm
• Offers excellent solderability and high-performance characteristics.
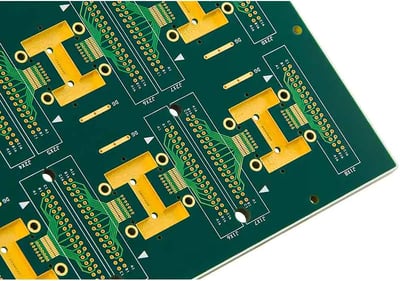
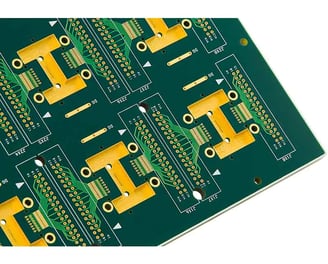
3. Immersion Silver:
• Thickness: 0.2 – 0.4μm
• Ideal for long-lasting and reliable electrical connections.
4. Immersion Tin:
• Thickness: ≥1.0μm
• Provides superior solderability and minimal oxidation.
5. OSP (Organic Solderability Preservative):
• Thickness: 0.1 – 0.3μm
• Best for cost-effective and eco-friendly PCB assembly.
6. ENEPIG:
• Nickel: 3 – 8μm
• Palladium: 0.05 – 0.15μm
• Gold: 0.05 – 0.1μm
• Offers enhanced reliability and durability for high-frequency applications.
7. Plating Gold:
• Nickel: 3 – 6μm
• Gold: 0.1 – 4μm
• Ideal for premium-grade PCBs requiring long-term reliability.
8. Carbon Ink:
• Thickness: 0.10 – 0.35mm
• Used for creating conductive patterns on PCBs.
9. Peelable Mask:
• Thickness: 0.20 – 0.80mm
• Protects the PCB surface during assembly and ensures easier removal.
These precise surface finishes by Omini ensure superior performance, durability, and reliability for all your PCB needs.
Soldermask Specifications by Omini
Omini provides high-quality soldermask applications to ensure optimal protection and performance of your PCBs. Below are the key soldermask specifications:
1. Minimum Soldermask to Trace Clearance:
• Tolerance: 0.05mm
• Ensures proper insulation between traces and soldermask for enhanced durability.
2. Minimum Soldermask Track Cover:
• Tolerance: 0.05mm
• Guarantees effective protection for all copper traces on the PCB.
3. Minimum Soldermask Web:
• Tolerance: 0.075mm
• Ensures sufficient spacing between tracks for safe PCB functionality.
4. Thickness on Copper Trace:
• Range: 10 – 18μm
• Provides optimal insulation without compromising performance.
5. Thickness on Edge of Copper Trace:
• Minimum: >10μm
• Ensures reliable protection of copper edges for better performance and longevity.
With Omini’s advanced soldermask application techniques, you can trust that your PCBs will meet the highest standards of quality and reliability.
PCB Legend/Silkscreen Specifications by Omini
Omini ensures precision in every aspect of PCB manufacturing, including legend and silkscreen printing. Below are the key tolerances for legend and silkscreen applications:
1. Minimum Width:
• Tolerance: 0.10mm
• Ensures accurate and readable markings for PCB identification.
2. Minimum Height:
• Tolerance: 1.00mm
• Guarantees clear and legible silkscreen for all PCB components and labels.
Omini uses state-of-the-art printing technology to meet these specifications for the highest quality and reliability.
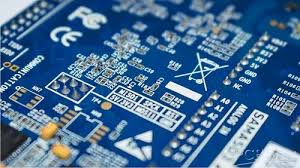
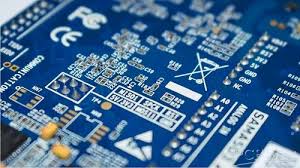
PCB Routing/Profiling Tolerances by Omini
For precise routing and profiling, Omini follows strict tolerances to ensure optimal board functionality. Below are the key tolerances for PCB routing/profiling:
1. Min. Trace/Pad to Outline – Outer Layers:
• Tolerance: 0.15mm
• Ensures proper separation for routing without damaging traces or pads.
2. Min. Trace/Pad to Outline – Inner Layers:
• Tolerance: 0.20mm
• Provides safe clearance for inner-layer routing.
3. Profile Dimensional Tolerance:
• Tolerance: ±0.13mm (Best: ±0.13mm)
• Guarantees precise dimensional accuracy for the final PCB profile.
Omini’s routing processes are designed to meet these critical tolerances, ensuring the integrity and functionality of your PCB.
PCB Scoring/V-Cut Tolerances by Omini
Omini ensures accurate scoring and V-cut processes for reliable PCB separation. Below are the key tolerances for scoring/V-cut applications:
1. Maximum PCB Thickness:
• Tolerance: 3.20mm
• Suitable for a wide range of PCB thicknesses.
2. Minimum PCB Thickness:
• Tolerance: 0.60mm
• Ensures durability and precision for thinner boards.
3. Min. V-Cut Copper Distance:
• Tolerance: 0.3mm
• Prevents damage to copper traces during V-cut operations.
4. Difference After Separation:
• Tolerance: ±0.20mm
• Ensures consistent quality after the separation process.
5. Normal Rest Material:
• Tolerance: 0.50mm ±0.10mm
• Provides optimal material support for clean V-cut separation.
6. V-Cut Positional Tolerance Top to Bottom:
• Tolerance: ±0.1mm
• Guarantees accurate alignment during the V-cut process.
7. Minimum Score Depth:
• Tolerance: 0.1mm
• Ensures that the scoring depth is sufficient for easy separation without compromising board integrity.
At Omini, we ensure that every PCB is routed and scored to perfection, meeting the most demanding specifications for both functionality and ease of handling.
PCB Edge Beveling Specifications by Omini
Omini offers precision edge beveling services to ensure your PCBs meet the required structural and functional standards. Below are the key tolerances for edge beveling:
1. Bevel Angle Tolerance:
• Tolerance: ±5°
• Available bevel angles: 15°, 30°, 45°, 60°
• Ensures precise angle cuts for smooth and clean PCB edges.
2. Remain Material Thickness Tolerance:
• Tolerance: ±0.1mm
• Ensures optimal material thickness for durability and performance.
Omini’s edge beveling process ensures high precision and consistency across all PCB designs.
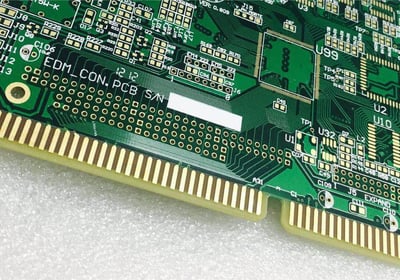
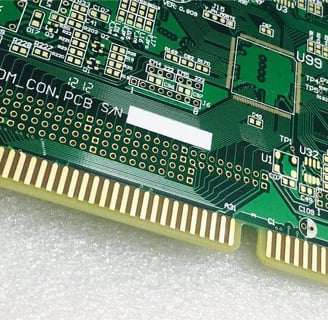
PCB Impedance Tolerance by Omini
Omini delivers high-precision impedance control for PCB manufacturing, ensuring reliable signal transmission and electrical performance. Below are the key impedance tolerances:
1. Impedance Tolerance:
• Tolerance: ±10% (Best: ±5%)
• Ensures reliable impedance control for high-speed, high-frequency applications.
At Omini, we adhere to strict impedance control measures to guarantee that your PCBs meet the highest standards of electrical performance.
PCB Electrical Test Tolerances by Omini
Omini performs thorough electrical testing to ensure your PCBs meet quality and performance standards. Below are the key tolerances for electrical testing:
1. Minimum Test Pitch:
• Tolerance: 0.10mm
• Ensures that all electrical tests are accurately performed with minimal risk of error.
2. Smallest Testable Pad:
• Tolerance: 0.05mm
• Guarantees reliable testing even on small and fine-pitch pads.
3. Test Voltage:
• Tolerance: 500V
• Ensures thorough electrical testing under standard conditions.
4. Test Current:
• Tolerance: 200mA (Adjustable)
• Allows for customized current settings based on specific testing requirements.
5. Continuity Test:
• Minimum Resistance: 5Ω
• Ensures reliable electrical connectivity for all tested paths.
6. Isolation Test:
• Maximum Resistance: 500MΩ
• Ensures that the PCB meets isolation requirements to prevent short circuits or electrical leakage.
Omini provides comprehensive electrical testing to ensure the reliability and functionality of your PCBs in real-world applications.
Contacts
Email: sales@ominipcba.com
Mobile: +86-185-7640-5228
Copyright © 2007-2025. Omini Electronics Limited. All rights reserved.
Head Office: +86-755-2357-1819
Products & Services
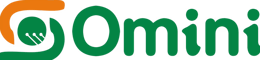
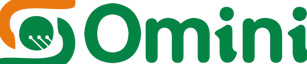
Office Address: No. 605, Tongxin Technology Building, Bao’an Avenue, Bao’an District, Shenzhen, Guangdong, China.
SMT Plant: A Building, Longwangmiao Industrial Park, Baishixia Community, Fuyong Street, Bao'an District, Shenzhen, China.
Omini Electronics Limited is an expert in trusted PCB Fabricaton and PCB Assembly in China since 2007. We have served over 1000 global customers with high-quality, low to medium-volume production. Certified by UL (E532498), ISO9001:2015, and ISO13485:2016, we offer expert electronics manufacturing services, including PCB manufacturing, assembly, and contract manufacturing, ensuring top-tier quality and precision in every project.