Phone: +86-755-2357-1819 Mobile: +86-185-7640-5228 Email: sales@ominipcba.com whatsapp: +8618576405228
SMT Assembly
At Omini, we specialize in high-quality PCB assembly, offering reliable and cost-effective solutions to meet the diverse needs of the electronics industry. With over 15 years of expertise, we are your trusted partner for all your PCB assembly requirements.
Single-Sided & Double-Sided SMT Assembly: Professional assembly for both single and double-sided surface-mount technology (SMT).
Flexible Assembly Options: Choose from consigned PCB assembly, partial turnkey, and full turnkey assembly solutions to suit your project needs.
No Minimum Order Quantity: We offer flexible solutions with no minimum order requirements and highly competitive pricing, making us the ideal choice for both small and large volume orders.
Comprehensive Testing Services: Our advanced testing methods include E-test, AOI (Automated Optical Inspection), X-ray, ICT (In-Circuit Test), FCT (Functional Test), and Burn-in Testing to ensure the highest quality and performance.
Certified Quality: We are ISO 9001:2015, ISO 13485:2016 Certified & UL Listed, ensuring that all our products meet the highest industry standards.
Expertise in Complex Components: We handle a wide range of component types, including Min. 01005, BGA, micro-BGA, QFN, DFN, CSP, and more.
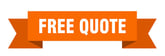

What is SMT Assembly?
Surface Mount Technology (SMT) Assembly is a cutting-edge assembly process that uses conductive solder paste to mount electronic components directly onto the surface of Printed Circuit Boards (PCBs). As the electronics industry has advanced, SMT assembly has replaced traditional Through-Hole Technology (THT) for many applications, enabling the production of smaller, higher-density, and faster electronic devices. Unlike THT, which relies on wave soldering, SMT assembly utilizes reflow soldering to cure the adhesive material, providing a more efficient and precise method for component placement.
The Evolution of Electronics and PCB Assembly
In the past, electronic devices were bulky and heavy, much like the cathode-ray tube (CRT) televisions with tall antennas used to capture signals. Today, flat-screen televisions are standard, equipped with multiple functionalities such as web browsing, speech recognition, connectivity, and even data storage. This dramatic shift towards miniaturization in electronic devices has not only reduced their size but also improved performance. The driving force behind these advancements lies in innovations in electronics manufacturing, particularly in the use of Printed Circuit Boards (PCBs) to house and connect internal components.
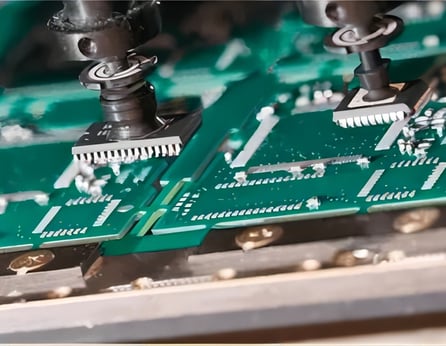
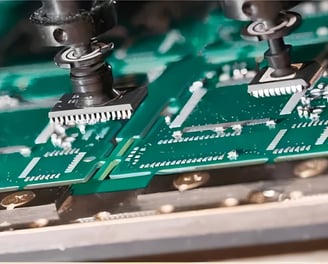
Historically, the conventional method for attaching components to PCBs was Through-Hole Technology (THT). In THT, the component leads are inserted into holes on the PCB and soldered into place. However, as the demand for smaller, more compact devices increased, a more efficient and space-saving solution was required. This led to the development of Surface Mount Technology (SMT), a technique that allows components to be mounted directly onto the surface of the PCB, reducing the need for large, bulky packaging.
In this article, we will explore the fundamentals of SMT assembly, its benefits, and the challenges it presents in modern electronics manufacturing.
The Benefits of SMT PCB Assembly
PCB Miniaturization
Surface Mount Technology (SMT) offers significant advantages over traditional Through-Hole Technology (THT) when it comes to PCB miniaturization. Unlike THT, which requires more space for component placement, SMT assembly enables the design of more compact and lightweight printed circuit boards. This is particularly beneficial for applications in the rapidly growing wearable and portable device sectors, where space-saving is essential for optimal performance.
Enhanced Electrical Performance
SMT assembly provides superior electrical performance, especially for high-frequency applications. One key advantage is signal noise reduction, thanks to the lower lead inductance and capacitance offered by SMT components. This ensures better signal integrity and higher reliability in demanding electronic devices. The versatility of SMT also allows for a wide range of component types and packages, making it an ideal solution for various PCB designs and applications.
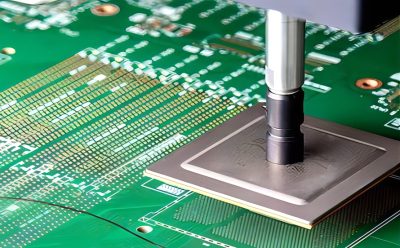
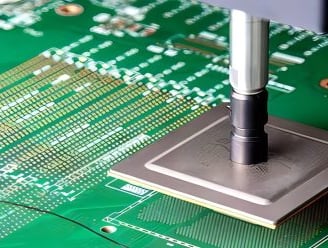
Automation for Faster Production
The adoption of automation in SMT PCB assembly enables much faster production times. Advanced high-speed machines streamline the entire process, from component placement to soldering, significantly reducing manufacturing time. Additionally, the process is simplified because there is no need for drilling holes to insert leaded components, which is common in THT assembly. This efficiency allows for high-volume production, cost savings, and faster turnaround times for clients.
With omini’s state-of-the-art SMT PCB assembly services, you can benefit from cutting-edge technology and expertise to create high-performance, compact, and reliable electronic products.
Common Defects in SMT Assembly: Insights from Omini
Achieving zero defects in SMT PCB assembly is the ultimate goal. As the demand for miniaturized devices increases, PCBs become more susceptible to various defects that can compromise quality and performance. At omini, we understand the importance of identifying and addressing these potential issues to ensure high-quality manufacturing. Below are some of the most common defects encountered during the SMT assembly process.
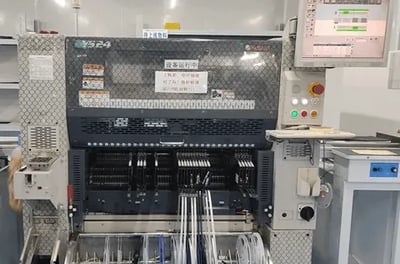
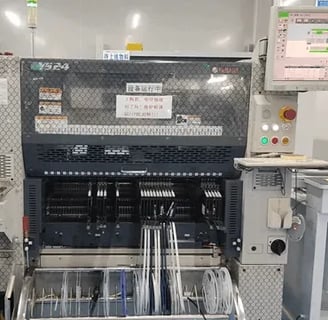
2. Tombstoning
Tombstoning refers to a soldering defect where a component becomes soldered on only one side, causing it to appear as though it is standing vertically—hence the term “tombstone.” This issue typically arises from incorrect pad design or improper solder mask application, which can cause instability in the component’s placement and lead to poor electrical connections.
3. Solder Bridging
Solder bridging occurs when excess solder paste creates an unintended connection between two adjacent pads, leading to a short circuit. This defect is often caused by excessive solder paste application, an unoptimized thermal profile during reflow, or poor stencil design. Solder bridging can cause serious electrical issues, potentially damaging the circuit and leading to product failure.
4. Solder Balls
Solder balls are small spherical clumps of solder that detach from the joint during the SMT assembly process. These balls pose a significant risk because they are conductive and can cause short circuits during electrical testing. Common causes of solder balling include moisture in the solder paste, misaligned stencil printing, and ineffective solder flux. At omini, we focus on preventing solder ball formation to ensure optimal electrical performance and reliability.
At omini, we are committed to achieving the highest standards in SMT assembly by addressing these common defects through precise process control, advanced equipment, and expert knowledge. We continuously optimize our techniques to reduce errors and deliver high-quality PCBs that meet the most stringent industry standards.
1. Insufficient Solder Coverage
Insufficient solder coverage is a common issue in SMT PCB assembly that can lead to weak and unreliable connections between components and PCB pads. This defect is often caused by poor wetting, improper stencil aperture dimensions, insufficient solder paste volume, or misalignment during stencil printing. Additionally, an inadequate reflow peak temperature can also contribute to insufficient solder coverage, resulting in potential circuit failure.
Key Processes in SMT PCB Assembly by omini
At omini, we optimize these processes to deliver precise, high-performance SMT PCB assemblies, meeting the strictest industry standards.
1. Solder Paste Printing
Solder paste is applied to the PCB using a stencil and squeegee. The stencil’s apertures define the paste pattern, which is then spread evenly across the PCB pads. Controlling the amount of paste is crucial for creating reliable solder joints.
2. Pick and Place
A fully automated Pick and Place machine uses robotic arms and nozzles to accurately position components onto the PCB. Precision during this step is essential to avoid misalignment, which could lead to defects like solder bridges. The placement accuracy directly impacts the overall quality of the assembly.
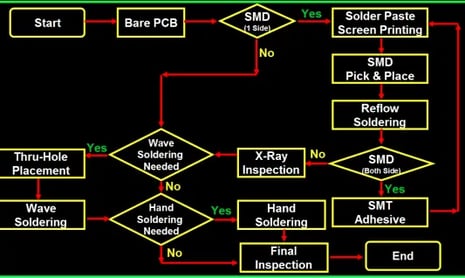
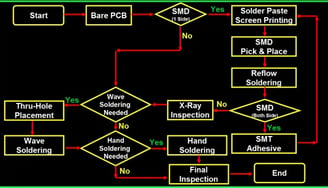
3. Reflow Process
The PCB, with components attached to wet solder paste, passes through a reflow oven. The process includes preheating, soaking, reflow, and cooling stages. The goal is to activate flux, melt the solder paste, and create strong, reliable joints. Inert Nitrogen gas is often used inside the oven to prevent contamination and ensure the best results.
4. Inspection Techniques
Inspection ensures that any quality issues are detected early. Automated Optical Inspection (AOI) uses high-resolution cameras to quickly check the PCB’s surface for defects. X-ray inspection, available in 2D and 3D, offers a non-destructive method to inspect solder joints and internal structures. These techniques help maintain high-quality standards throughout the assembly process.
5. Electrical TestingTo verify functionality, Electrical Testing is performed using methods like In-Circuit Testing (ICT) or Flying Probe Testing. ICT is ideal for high-volume production, utilizing fixtures for electrical measurements. Flying Probe Testing uses robotic arms for flexible, on-demand testing. Functional testing can also simulate real-world conditions to ensure the PCB performs as expected.
Why Choose Omini as Your PCB Assembly Partner?
With numerous SMT assembly manufacturers available, why should you choose Omini? As a leading provider of SMT PCB assembly services in China, Omini combines advanced technology, high-quality standards, and cost-effective solutions. Here are the key reasons why our customers choose us:
1. State-of-the-Art Equipment & Technical Expertise
At omini, we operate a cutting-edge assembly line featuring the latest technology to ensure high-speed production and reliable, high-quality products.
2. Proven Experience & Track Record
With years of experience in PCB manufacturing, our assembly line consistently delivers a high yield. We are actively involved in every phase of production, from design and assembly to testing, ensuring top-tier results.
3. Cost-Effective Solutions
We understand the importance of affordability in business. omini offers competitive pricing and flexible cost structures, ensuring that you receive quality products at a reasonable price, tailored to your budget and needs.
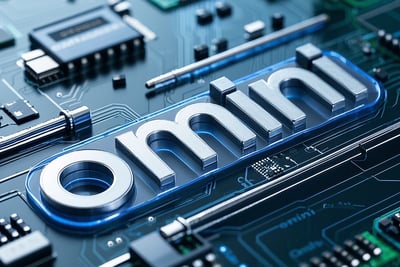
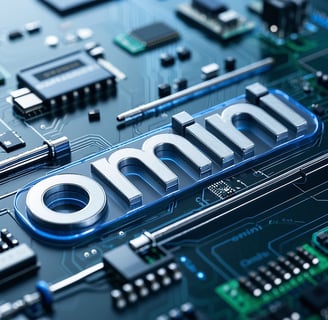
4. Uncompromising Quality
Quality is our top priority. We adhere to international standards and implement rigorous internal controls to deliver high-quality, reliable SMT PCB assemblies that meet the most demanding specifications.
Partner with omini for high-performance, cost-effective SMT PCB assembly services that deliver consistent, high-quality results.
Contacts
Email: sales@ominipcba.com
Mobile: +86-185-7640-5228
Copyright © 2007-2025. Omini Electronics Limited. All rights reserved.
Head Office: +86-755-2357-1819
Products & Services
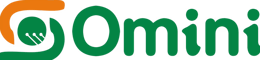
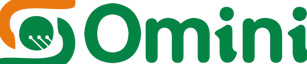
Office Address: No. 605, Tongxin Technology Building, Bao’an Avenue, Bao’an District, Shenzhen, Guangdong, China.
SMT Plant: A Building, Longwangmiao Industrial Park, Baishixia Community, Fuyong Street, Bao'an District, Shenzhen, China.
Omini Electronics Limited is an expert in trusted PCB Fabricaton and PCB Assembly in China since 2007. We have served over 1000 global customers with high-quality, low to medium-volume production. Certified by UL (E532498), ISO9001:2015, and ISO13485:2016, we offer expert electronics manufacturing services, including PCB manufacturing, assembly, and contract manufacturing, ensuring top-tier quality and precision in every project.