Phone: +86-755-2357-1819 Mobile: +86-185-7640-5228 Email: sales@ominipcba.com whatsapp: +8618576405228
Omini Bare PCB Solutions
With over 16 years of experience in PCB manufacturing, Omini offers a comprehensive range of bare PCB solutions tailored to your specific needs.
1-40 Layers: Rigid, flex, and rigid-flex PCBs, perfect for diverse applications, ensuring optimal performance and reliability across multiple industries.
High-Quality Materials: Omini uses top-grade materials like FR4, high-speed, high-frequency, Metcal core, ceramic, and PTFE, ensuring consistent, high-performance PCBs.
Advanced Via Technology: Blind & buried vias, micro vias, and any-layer HDI provide flexible, high-density solutions for intricate, high-performance PCB designs.
Via Plugging: Conductive and non-conductive via plugging ensures superior electrical performance, reliability, and quality in complex PCB designs and assemblies.
Specialized PCB Designs: From back drilling and backplanes to embedded devices and IC substrates, Omini delivers tailored PCB designs that meet specific requirements.
Quick Turnaround: With our quick-turn bare PCB service, we deliver high-quality PCBs within 24 hours, ensuring timely solutions for urgent projects.
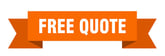
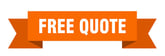
What is a Bare PCB?
A bare PCB, also known as a PCB bare board, is a fully fabricated printed circuit board (PCB) with copper traces and vias, enabling electronic connections. A bare PCB can be defined as a PCB without components mounted on it, or a raw PCB. While a bare PCB might seem useless by itself, it plays a crucial role in the manufacturing and testing process. Most tests and procedures are performed on the bare PCB before components are added, as they cannot be executed on fully assembled PCBs. However, a bare PCB cannot function on its own; functional testing and performance evaluations are only possible once components are placed on the bare board.
A bare PCB consists of:
1. Substrate or Base Material: The substrate or base material of the PCB maintains insulation between copper layers, providing structural integrity.
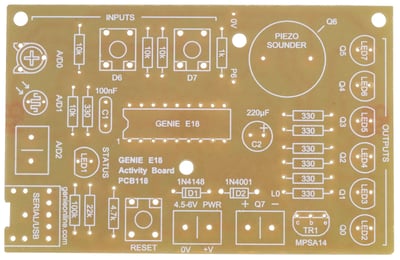
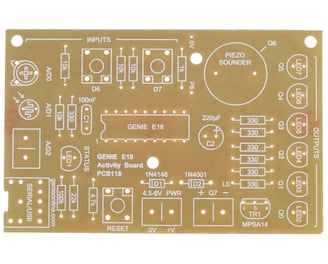
2. Copper Layer: The copper layer is where traces and nets are routed, facilitating the electronic connections between components.
3. Solder Mask: This protective layer covers the copper traces, safeguarding them during the PCB assembly process.
4. Silkscreen: The silkscreen consists of text and symbol markings, typically in white, which provide important identification and alignment information.
5. Surface Finishes: These protective layers are applied to copper pads that are not covered by solder mask, ensuring optimal solderability. Common surface finishes include HAL, ENIG, OSP, immersion silver, immersion tin, and ENEPIG.
Omini specializes in providing high-quality bare PCB solutions, ensuring reliable performance in diverse applications across various industries. With over 16 years of experience, Omini excels in delivering tailored PCB services that meet rigorous industry standards.
Difference Between Bare PCB and Zero PCB
It is important to note that while bare PCB and zero PCB might seem similar, they are completely different. A bare PCB is a custom PCB without components, designed for specific applications. On the other hand, a zero PCB is a general-purpose board made for versatile small applications. Zero PCBs feature small holes arranged in a grid pattern, with no solder mask or silkscreen, designed to accommodate components in a manner similar to a breadboard. These are used primarily for testing and evaluation of small circuits or circuit snippets.
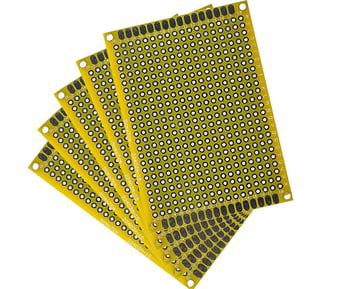
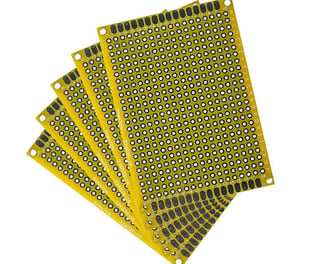
Bare PCB Manufacturing Process
Bare PCB manufacturing, or fabrication, is a systematic and precise process. The steps involved in the production of a bare PCB include:
1. Generating Design and Output File: The schematic design is created using EDA tools, and a PCB layout file is generated. After design rule checks (DRC) and signal integrity (SI) simulations, the Gerber file is created along with fabrication notes. The Gerber file is sent to the manufacturer for quotation, and fabrication begins once the price and terms are agreed upon.
2. Generating Films: The Gerber file undergoes DFM checks, and a plotter creates detailed films of the PCB design. These films are printed on plastic sheets with photo-negative images for each layer and solder mask.
3. Printing the Layers: The copper-clad laminate is covered with a photoresist layer, which hardens under ultraviolet radiation. A photo-negative sheet shields the areas not meant to be hardened, which are then washed out to reveal the copper traces.
4. Removing Unwanted Copper: The unwanted copper is removed with an alkaline solution, leaving the desired copper protected by the hardened photoresist. The remaining photoresist is washed off, preparing the layers for inspection.
5. Visual Inspection: All layers are visually inspected to ensure accuracy and quality before proceeding. Any errors detected after bonding require the process to be repeated.
6. Layer Bonding: The prepared layers are stacked with core and prepreg material between them, following the stack-up specified in the fabrication note. The stack is then heated and pressed using a computer-controlled press.
7. Drilling: A machine identifies drilling coordinates and drills precise holes. The board is cleaned, and the bare PCB begins to take shape, though it is still incomplete.
8. Copper Plating: Electroplating is used to apply copper to the drilled holes, and the board is plated with tin to protect the copper during etching.
9. Final Etching: The tin layer is dissolved along with the exposed copper, finalizing the copper traces and connections. The board is then cleaned thoroughly.
10. Applying Solder Mask: The solder mask ink is applied, and the PCB is exposed to UV radiation before being baked in an oven.
11. Surface Finishing: The surface finish is applied based on the fabrication notes or the designer’s specifications, enhancing the PCB’s solderability and durability.
12. Printing Silkscreen: Silkscreen text and symbols are printed on the top and bottom surfaces of the PCB using an inkjet printer, as specified in the Gerber file. The bare PCB is now distinguishable, though still part of a panel.
13. Testing: Electrical testing is conducted on the panel according to the manufacturer’s protocols. Additional tests may be requested by the designer for an extra cost.
14. Separating Bare PCB from the Panel: After passing all tests, the bare PCB is separated from the panel. The PCBs are cut along the edges using either a V-groove or router, allowing for easy separation. The single bare PCB is now ready.
Omini offers advanced bare PCB manufacturing solutions, specializing in high-quality, customized PCB designs for a wide range of applications across various industries. With over 16 years of expertise in PCB fabrication, Omini ensures the highest standards in quality, reliability, and precision.
Different Electrical Tests on Bare PCBs
Electrical testing plays a crucial role in ensuring the quality and functionality of bare PCBs before they are commissioned. All bare circuit boards must adhere to IPC 9252 standards, which provide guidelines for electrical testing of “unpopulated PCBs.”
There are several electrical tests that a bare PCB must undergo. Some of the key tests include:
1. Resistance Test: This test measures the resistance of nets on the bare circuit board to ensure proper functionality and performance.
2. Isolation Test: Also known as isolation resistance testing, this test ensures there is sufficient insulation between nets to prevent any chance of shorting.
3. Capacitance Test: Capacitance tests are performed to determine the capacitance between various points on the PCB, ensuring proper circuit behavior.
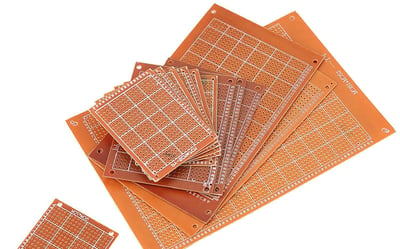
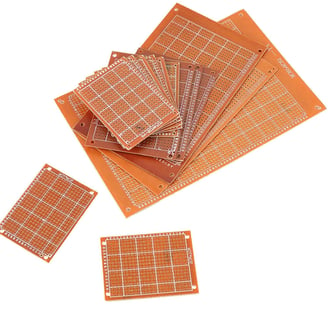
4. Continuity Testing: This test checks whether the resistance between nodes within the same netlist is below the continuity threshold, verifying that there are no unintended disconnections.
5. Flying Probe Test: A popular and reliable test, the flying probe test is used to perform the above checks quickly and accurately, making it highly favored among PCB manufacturers.
6. 4-wire Kelvin Test: The 4-wire Kelvin test is used to measure very low resistances with high accuracy. This test is typically not performed on basic PCBs but is essential for advanced PCBs with tight tolerances and small vias. This test is generally requested separately, as it is not part of standard procedures.
Once the bare PCB successfully passes all of these tests, it is marked with the “OK tested” status, signaling that it is ready for the next stage of assembly.
Omini specializes in providing high-quality, customized PCB manufacturing services with rigorous electrical testing procedures to ensure optimal performance and reliability. With over 16 years of expertise in PCB fabrication, Omini guarantees that all PCBs meet industry standards and client specifications before they are assembled.
Omini: Your Trusted Partner in Fabricating Bare PCB Boards
Omini’s bare PCB product line offers a smooth and efficient development process, ensuring high-quality results for your projects. Our expertise in PCB fabrication guarantees reliability and precision, making us your go-to partner for all your bare PCB needs.
1. Expert Design Review
Our skilled engineering team thoroughly evaluates your design files to ensure the feasibility of bare PCB manufacturing, addressing any potential issues before production begins.
2. High-Quality Production
At Omini, we manufacture your bare PCBs to the highest standards, utilizing a trusted network of suppliers and vendors. This ensures that each board meets industry requirements for performance and durability.
3. Advanced Fabrication Processes
We employ cutting-edge PCB fabrication techniques, such as plated slots, impedance control, and advanced via technologies like blind, buried, and micro-drilled vias. These processes allow us to meet the complex requirements of your design.
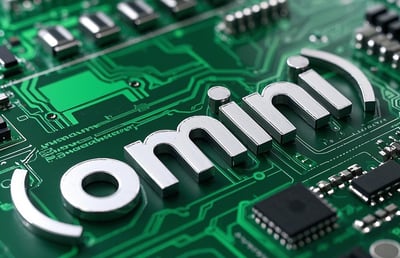
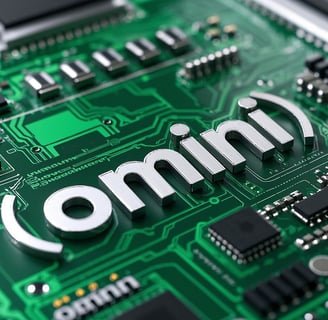
4. Full Assembly Integration
Transition seamlessly from unassembled PCBs to fully assembled boards. With Omini’s streamlined approach, you can move from design to production effortlessly, making design revisions and adjustments easy and efficient.
Omini is dedicated to delivering exceptional bare PCB fabrication services, providing the precision and reliability you need for your projects. With over 16 years of experience in the PCB industry, we are committed to helping you bring your designs to life.
Contacts
Email: sales@ominipcba.com
Mobile: +86-185-7640-5228
Copyright © 2007-2025. Omini Electronics Limited. All rights reserved.
Head Office: +86-755-2357-1819
Products & Services
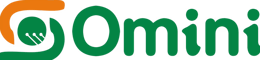
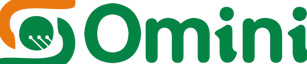
Office Address: No. 605, Tongxin Technology Building, Bao’an Avenue, Bao’an District, Shenzhen, Guangdong, China.
SMT Plant: A Building, Longwangmiao Industrial Park, Baishixia Community, Fuyong Street, Bao'an District, Shenzhen, China.
Omini Electronics Limited is an expert in trusted PCB Fabricaton and PCB Assembly in China since 2007. We have served over 1000 global customers with high-quality, low to medium-volume production. Certified by UL (E532498), ISO9001:2015, and ISO13485:2016, we offer expert electronics manufacturing services, including PCB manufacturing, assembly, and contract manufacturing, ensuring top-tier quality and precision in every project.