Phone: +86-755-2357-1819 Mobile: +86-185-7640-5228 Email: sales@ominipcba.com whatsapp: +8618576405228
Omini PCB Stencil Solutions
Omini offers a one-stop solution for PCB and assembly services, providing high-quality, industry-standard PCB stencil solutions. Our services include:
Laser Cut and Electropolishing Stencil (E.P. Stencil) for precision and durability.
Surface Mount Technology (SMT), Thru-hole (PTH), and Mixed Technology to accommodate various assembly needs.
Rigid, Flexible PCB, and Rigid-Flex PCB Assembly for diverse design requirements.
Small to Medium Volume Production offering flexible manufacturing options and quick turnaround times.
ISO9001:2015, ISO 13485:2016 Certified & UL Listed ensuring services meet international quality standards.
100% E-test, AOI, X-RAY, ICT & FCT for comprehensive quality control and product reliability.
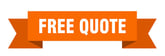
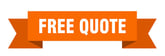
Omini: What is a PCB Stencil?
A PCB stencil is a critical tool in Surface Mount Technology (SMT), used to deposit the correct amount of solder paste onto printed circuit boards (PCBs) at precise locations. Omini specializes in providing high-quality PCB stencils for efficient and accurate assembly. Key features of PCB stencils include:
1. Flat and Thick Metal Construction with apertures matching the solder pads on the PCB, ensuring accurate solder paste deposition.
2. Fiducial Marks included on the stencil for proper alignment during the soldering process, improving precision and reducing errors.
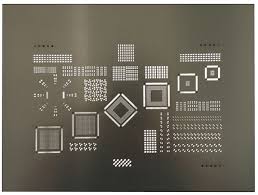
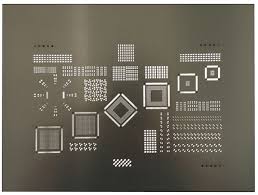
3. Efficient Solder Paste Deposition through stencil printing, enabling fast and consistent paste application, ideal for mass production.
4. SMT Process Optimization by utilizing PCB stencils, which ensures high-quality and repeatable results in large-scale assembly operations.
At Omini, we provide advanced PCB stencils that support precision and reliability in SMT applications, ensuring faster, more efficient assembly for all your production needs.
Omini: Paste Printing Steps with PCB Stencils
The PCB stencil printing process is a critical first step in Surface Mount Technology (SMT), often used in both single-sided PCB assembly and double-sided PCB assembly. A successful SMT process relies on optimizing key variables, such as stencil thickness, aperture sizes, solder paste condition, metal filler sizes, squeegee speed, pressure, and angle. Here’s an overview of the solder paste printing process using PCB stencils, an essential aspect of quality PCB assembly.
1: Set up PCB Stencil on the Printing Machine
To begin, place the PCB on the paste printing machine. The PCB stencil is then fastened and clamped securely to prevent any movement. Both automated and manual printing machines can be used, depending on production needs.
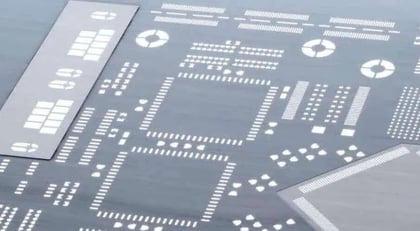
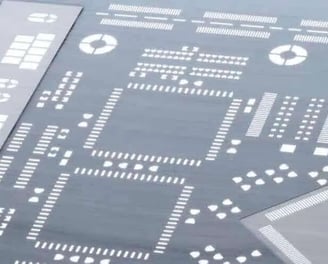
2: Add Solder Paste onto the Stencil
Once the PCB stencil is in place, the appropriate amount of solder paste is applied to the stencil. Ensure that the solder paste has been properly mixed and stored at a temperature of 4°C to 10°C to maintain its optimal condition.
3: Align PCB and PCB Stencil
The PCB board is then clamped and aligned with the PCB stencil so that the apertures match the contact pads where the solder paste will be deposited. Accurate alignment is crucial to ensure correct paste placement.
4: Squeegee Move and Push Solder Paste onto PCBs
Next, the squeegee moves across the stencil, evenly distributing the solder paste into the PCB stencil apertures. The paste is pushed through the apertures, adhering to the corresponding pads on the PCB.
5: Separate Circuit Board Stencil and PCB
After the paste has been applied, the PCB stencil is carefully separated from the PCB. The PCB is then unclamped and moves to the next step in the process. For fine-pitched solder pads, a straight-motion separation is recommended for precise solder paste printing.
6: Inspection after Solder Paste Printing
Optical inspections are performed after solder paste printing to verify that the correct amount of paste has been applied and properly aligned. A camera system may be used to automatically inspect the paste deposits. Some PCB printing machines include built-in inspection features, or a separate inspection machine can be used for additional quality checks.
7: Circuit Board Stencil Cleaning
To ensure consistent solder printing quality, it is essential to clean the PCB stencil regularly. Cleaning removes solder paste residues from the stencil apertures, preventing hardened deposits that could affect future printing. Regular cleaning is especially critical for fine-pitch components. Stencil cleaning can be done manually or automatically, with modern PCB printing machines featuring spray tanks for automatic cleaning.
Omini: Key Considerations in PCB Stencil Design
When designing PCB stencils for assembly manufacturing, several key factors and techniques must be considered to ensure optimal performance. Omini specializes in providing high-quality, precision-engineered PCBs and stencils to meet the needs of various assembly processes. Below are the critical considerations in PCB stencil design:
1. Stencil Geometry
The geometry of PCB stencils plays a crucial role in the accuracy and quality of the solder paste deposition process. Omini designs stencils in various shapes and sizes for both single-sided and double-sided PCB assembly. Common shapes include circular and rectangular apertures, with custom designs made to match component shapes. Key factors in stencil geometry include:
• Aperture Size and Shape: Must be designed according to solder pad sizes, component pitch, and paste type.
• Thickness: Influences solder paste volume; thinner stencils may be required for fine-pitch components to minimize solder overflow and bridging.
• Area Ratio and Aspect Ratio: IPC standards specify two important ratios: area ratio (PCB pad area to aperture wall area) and aspect ratio (aperture width to stencil thickness).
• Solder Paste Considerations: The metal filler size and solder ball size of the paste influence stencil design dimensions.
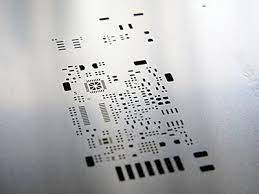
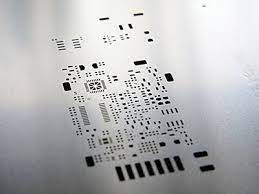
2. PCB Stencil Materials
The material of the PCB stencil directly affects the durability, performance, and precision of the stencil in PCB assembly. Omini uses high-quality materials to produce stencils that meet various production requirements:
• Stainless Steel Stencils: The most commonly used material in double-sided PCB assembly due to its resistance to corrosion, high durability, and dimensional stability, making it ideal for high-volume production.
• Polymer Stencils: Less commonly used, these flexible stencils, often made from Kapton, are suitable for low-volume or prototype PCB assembly, but they are less durable and accurate than stainless steel stencils.
3. Multi-Level Stencils
For more complex PCB assemblies, multi-level stencils or stepped stencils may be necessary. These stencils have varying thicknesses within a single aperture, making them ideal for fine-pitched components. Omini offers multi-level stencils designed to improve paste deposition accuracy in challenging designs. Key features include:
• Variable Thickness: Each aperture can have different thicknesses to accommodate specific component requirements.
• Manufacturing Process: Multi-level stencils are often created using an initial chemical etching process followed by laser etching to achieve precise control over the aperture dimensions.
At Omini, we ensure that every PCB stencil is meticulously designed and manufactured to meet the specific needs of your PCB assembly process, helping to optimize production quality and efficiency.
PCB Stencil Manufacturing Techniques by Omini
Stencils for PCB assembly manufacturing are essential tools, made by referencing the PCB’s design layout through Gerber file data. The quality of the aperture walls varies depending on the stencil manufacturing technique used. The precision and roughness of the apertures dictate the stencil’s overall quality. At Omini, we provide advanced PCB stencil solutions, ensuring high precision and reliability for your assembly needs. Below are the different stencil manufacturing techniques employed in the PCB industry.
1. Laser Cutting
Laser cutting is ideal for forming precise apertures with clean edges, especially in fine-pitched and high-density designs. This technique creates trapezoidal apertures that allow for smoother solder paste release, making laser-cut PCB stencils a popular choice in the industry. Omini utilizes laser cutting technology to deliver high-quality stencils that meet the strictest design specifications.
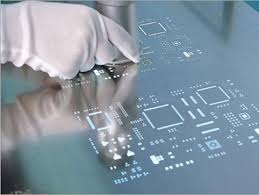
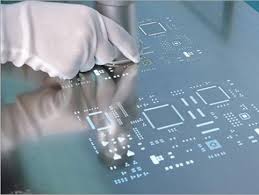
2. Chemical Etching
Chemical etching is a subtractive process used to create patterns on the stencil. In this method, the metal surface is first cleaned, followed by the application of a photoresist layer. The photoresist is developed, and unwanted metal is removed using an etchant spray. This process results in precise stencil apertures, ideal for standard PCB assembly. Omini applies this method to achieve clean and accurate stencils for various PCB designs.
3. Electroforming
Electroforming is an additive method that involves the use of nickel to form stencil apertures. It is often combined with laser cutting for enhanced precision. This technique is beneficial for creating high-quality stencils with complex aperture designs. Omini employs electroforming to deliver stencils that provide excellent performance and durability.
Solder Paste Printing Issues and Solutions by Omini
Improperly designed circuit board stencils can lead to various issues during solder paste printing. Below, we outline some common problems and the solutions from our experience at Omini.
1. Misaligned Printing
• Reason: Inaccurate alignment between the PCB and the stencil can result in misaligned printing.
• Solution: Ensure that the stencil is 100% accurate, and carefully align it with the PCB for optimal results. Proper alignment is crucial to achieve precise solder paste placement.
2. Solder Bridging
• Reason: Incorrect aperture geometry can cause solder overflow and bridging during the printing and reflow processes.
• Solution: Double-check the aperture geometry before printing and align the stencil correctly with the PCB. This ensures that solder paste is applied in the right amount and avoids bridging.
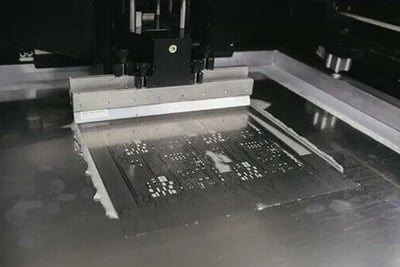
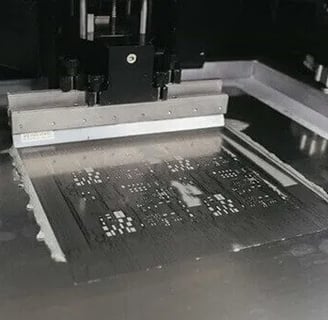
3. Incomplete Solder Coverage
• Reason: Narrow stencil openings may lead to insufficient solder volume, resulting in incomplete coverage on the PCB.
• Solution: Use stencil files designed by experienced engineers, ensuring that aperture sizes are correct. Compare the stencil design with the PCB pads to ensure full solder coverage.
4. Solder Balls
• Reason: Stencil thickness and aperture sizes can contribute to solder ball formation during reflow.
• Solution: Choose the appropriate stencil thickness and aperture sizes. Omini recommends using anti-solder ball stencils to minimize the risk of solder balls forming during the soldering process.
At Omini, we specialize in providing high-quality PCB stencils and addressing solder paste printing challenges. Our goal is to help you achieve perfect solder paste deposition for reliable and durable PCB assemblies.
Reasons to Choose Omini as Your PCB Stencil Supplier
When using surface mount technology (SMT), selecting a reliable PCB stencil manufacturer is essential to achieving high precision in PCB assembly. Omini, as a leading PCB stencil supplier, provides high-quality stencils tailored to your needs. Here are some key advantages of choosing Omini for your PCB stencil solutions:
1. Expertise in PCB Stencil Design and Manufacturing
Omini has extensive experience with a variety of PCB types and can deliver the most effective stencil solutions, particularly for PCB assembly. Our expert team understands the unique requirements of different PCB designs, ensuring that the stencil fits perfectly for your project.
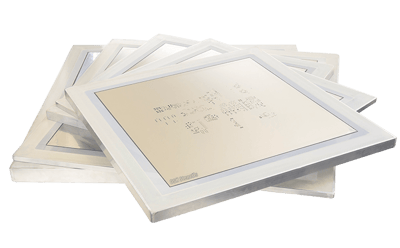
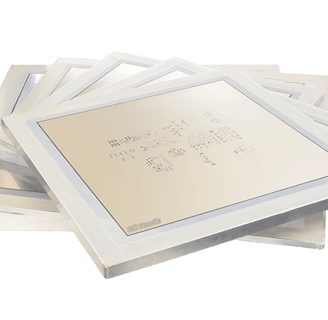
2. End-to-End Quality Assurance for PCB Stencils
At Omini, we oversee the entire process of PCB stencil production, from design to delivery. Our commitment to quality ensures that every stencil meets the highest standards, providing you with reliable results for superior PCB assembly.
3. Customized PCB Stencil Production Services
We offer bespoke PCB stencil services, catering to your specific needs. Whether you require a unique design or precise specifications, Omini guarantees timely delivery of custom stencils that meet your production requirements.
4. Support for Small and Medium Batch Production
Omini specializes in small to medium batch production of stencils for PCB assembly. Our tailored approach allows us to provide cost-effective solutions for both low-volume and high-volume production needs, ensuring flexibility for your business.
5. Comprehensive Communication and Technical Support
From the initial inquiry to the final delivery, Omini provides effective communication and technical support throughout the entire PCB stencil manufacturing process. Our team is always available to assist with any technical concerns and ensure a smooth experience.
At Omini, we combine cutting-edge technology and expert craftsmanship to deliver premium PCB stencils for your assembly projects. Contact us today to learn more about how we can meet your specific needs and place your order for customized PCB stencils.
Contacts
Email: sales@ominipcba.com
Mobile: +86-185-7640-5228
Copyright © 2007-2025. Omini Electronics Limited. All rights reserved.
Head Office: +86-755-2357-1819
Products & Services
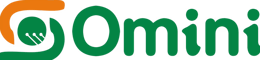
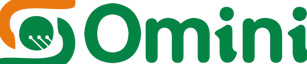
Office Address: No. 605, Tongxin Technology Building, Bao’an Avenue, Bao’an District, Shenzhen, Guangdong, China.
SMT Plant: A Building, Longwangmiao Industrial Park, Baishixia Community, Fuyong Street, Bao'an District, Shenzhen, China.
Omini Electronics Limited is an expert in trusted PCB Fabricaton and PCB Assembly in China since 2007. We have served over 1000 global customers with high-quality, low to medium-volume production. Certified by UL (E532498), ISO9001:2015, and ISO13485:2016, we offer expert electronics manufacturing services, including PCB manufacturing, assembly, and contract manufacturing, ensuring top-tier quality and precision in every project.